Advance Modeling & Simulation (CFD/FEA)
Industry Overview
The oil and gas industry is vast and encompasses various streams, each specializing in different aspects of exploration, production, refining, and distribution. Tridiagonal Solutions has extensive work experience of working for each stream of companies using its exclusive capabilities of CFD(Computational Fluid Dynamics) & FEA(Finite Element Analysis). Our engineers are passionate to address complex engineering problems with their exclusive analytical and mathematical skills. Having good hands on several latest CAE(Computer Aided Engineering) tools. We deliver ultimate solution instead of just Simulation results.
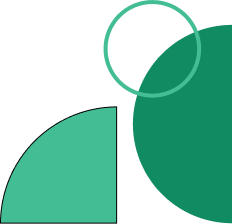
What we do
Tridiagonal is actively involved in R&D projects and Joint-Industry-Programs (JIP) with global companies. We work with oil and gas industry majors like National oil companies, global owner-operators, Engineering service providers, process equipment designers, and Engineering Procurement Construction(EPC) firms.
- Multiphase Simulation
- Separation
- Blending
- Phase Change
- Crystallization
- Combustion modeling
- Gas and Oil combustion
- Reaction Modeling
Computational Fluid Dynamics
Computational Fluid Dynamics (CFD) empowers you to visualize and analyze complex fluid flow phenomena within your designs. Our team of CFD specialists leverage cutting-edge tools and proven methodologies to provide comprehensive solutions for a wide range of applications, including heat transfer analysis for equipment design, Multiphase flow modeling and Combustion analysis for emission control. We are trusted partners of renowned companies since last two decades. We work on a wide range of applications making considerable contributions to design & process optimization.
.jpg?width=398&height=393&name=Computational%20Fluid%20Dynamics%20(CFD).jpg)

Our CFD engineers can analyze oil blending & suggest appropriate jet-mixture position for optimal performance. Homogenization time can also be predicted to take inferred decisions. Separation is an essential process in Oil & Gas industry, here we can evaluate and enhance performance of various separation equipment like two/three-phase separators, vertical/horizontal and spherical separators, Cyclone and pre-treaters with simulation.

Tridiagonal has considerable experience on modeling burner arrangements, flame interactions, NOx and SOx predictions and Flame impingement on radiant tube section to avoid rupture. Our engineers also worked on processed heaters used in reformers. We help optimize flow of fluid and air to Burner using CFD as well as improve combustion efficiency by optimizing fuel and air flow

Tridiagonal engineers work on both onshore & offshore oil extraction applications. Our team can analyze pressure drop patterns & erosion modeling of downhole tools using CFD as well as equipment & tools involved in other processes like completion, cementing & plugging and abandonment to understand fluid displacement. Other applications include sand screens, submersible pumps, steel catenary riser(SCR) & exhaust gas dispersion from offshore platforms.
.png?width=152&height=164&name=Dynamic%20Simulation%20(Operator%20training%20simulation).png)
Tridiagonal's CFD capabilities cover a wide range of equipment & processes under oil refining. Our simulation assessment helps solve coking issues in fractionators by tracking particle & liquid distribution. Insights provided from our M&S team are useful in selection of Fixed bed reactors to get improved temperature distribution & flow uniformity.

Through incorporation of coupled FEA-CFD analysis we offer more realistic solutions on various oil & gas equipment. Synergizing both these domains our experts help you solve problems related to Fluid Structure Interaction(FSI) & Thermal Structural interaction.
- Fatigue failure analysis
- Thermal , Static analysis
- Dynamic analysis and Non-linear
- Acoustic induced Vibration
- Buckling Analysis
Finite Element Analysis
Finite Element Analysis (FEA) has become an indispensable technology within the oil and gas industry. This sophisticated computer-aided engineering technique allows engineers to perform simulations of various components and structures and predict their behavior under real-world operating conditions.
This capability to analyze stress, strain, and deformations across a wide range of scenarios strengthens safety protocols, optimizes designs, and ultimately reduces costs throughout production, and transportation phases./p>
.jpg?width=398&height=393&name=Finite%20Element%20Analysis(FEA).jpg)

Our FEA engineers can do static structural analysis to assess the structural integrity of different pressure vessels broadly classified as Vertical Pressure Vessels and Horizontal Pressure Vessels used in Oil refineries. We do these analyses using industry standards like ASME and API for stress classification and ASCE for Seismic analysis. We also frequently analyze separators & coke drums for deformations.

From wellheads to offshore rigs our engineers can perform stress analysis to ensure safe & reliable operations. We can replicate the response of offshore platforms under combined forces of waves, wind, and sea currents. Under energy extraction operations, Tridiagonal works on a wide range of applications including Centrifugal compressors & gate valves.

Leveraging FEA, Tridiagonal can do a static analysis to capture stiffness of Distillation column to avoid collapse due to buckling loads. We have extensive experience in analyzing structural integrity of Storage tanks at component level such as Tank Roof Nozzle, Baffle Plate and bottom plate nozzle.

Tridiagonal engineers have considerable experience in predicting fatigue life of piping by calculating stress intensities at critical locations. We can simulate vortices and acoustic resonances and their effect on pipe wall structure to predict resonance frequency and high stress region in piping structures.
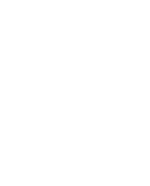
Through incorporation of coupled FEA-CFD analysis we offer more realistic solutions on various oil & gas equipment. Synergizing both these domains our experts help you solve problems related to Fluid Structure Interaction(FSI) & Thermal Structural interaction.
- Drill-bit interaction analysis
- Simulating Wellbore Stability
- Analyzing Fluid-Particle Interactions
Discrete Element Method
Discrete Element Modeling (DEM) is a technique used in oil and gas industry for simulating the behavior of granular materials, particularly in drilling processes
.jpg?width=398&height=393&name=Discrete%20Element%20Method%20(DEM).jpg)

Tridiagonal can simulate how drill bit interacts with the rock formations at various depths. Our engineers predict wear and tear of drill bits, optimize drilling parameters, and improve drilling efficiency.
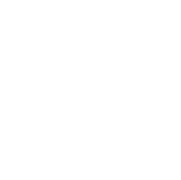
Wellbore instability can cause significant problems during drilling. Tridiagonal can model the movement of formation particles around the wellbore, helping to predict potential wellbore collapse and design strategies to prevent it.


- Predictive model based on Experimental and Simulation data.
- Response Surface Models.
- Reduced Order Modeling.
Digital Twin
Tridiagonal tech experts can build a virtual replica of assets & processes in various industries to reduce simulation iterations using data interpolation. Methods like CFD, FEA & DEM can make predictions that may not be practically achievable through physical sensors.
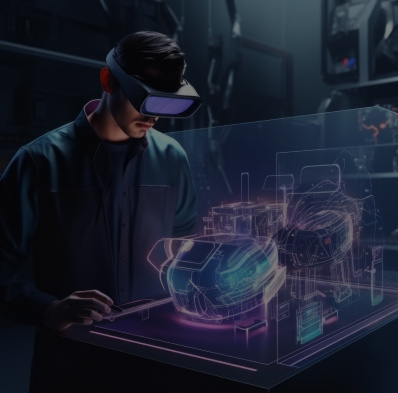
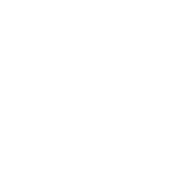
Areas where full-scale Simulation is computationally expensive & impractical, Tridiagonal can build ROMs by creating a lower-dimensional model that captures the essential behavior of the system. It not only speeds up simulations but also develops a straightforward approach for analysis.
%E2%80%8B.png?width=92&height=92&name=Creating%20Response%20surface%20models(RSM)%E2%80%8B.png)
In today's competitive world, Industry wants to save cost on simulations. Tridiagonal is addressing this requirement using a statistical technique called Response surface models(RSM). Here, our engineers are analyzing the relationship between several input variables and a desired output response variable. These response surface models are built using an appropriate set of CAE results, accurately predict the output variable for various input combinations without running individual Simulations. This technique is considerably reducing research and development cost in industries like oil refining and oil recovery.
- Fluid Structure Interaction.
- Thermoelectric Interaction.
- CFD-DEM coupling.
- Acoustic structural interaction.
- DEM-FEA coupling.
Multiphysics Simulation
As Oil and Gas industry includes many complex processes & equipment. It is always important to know the dynamics of internal processes & their effect on the equipment to enhance overall performance. Tridiagonal has developed capabilities to couple different disciplines to solve complex real life issues using computational methods.
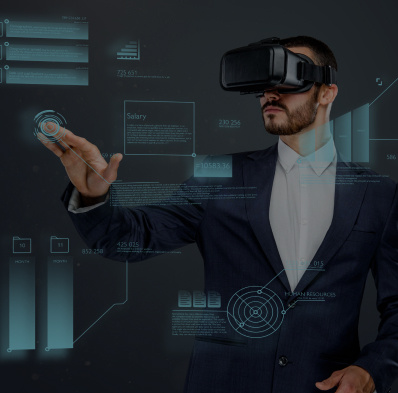

Tridiagonal uses the coupling of Computational Fluid Dynamics(CFD) and Finite Element Analysis(FEA) to analyze the interplay between fluids & structures. Our experts can analyze flow induced stresses, vibrations, and other dynamic effects. Our range of applications covers equipment like liquid seal drums, heat exchangers etc.

Our CFD engineers can provide boundary conditions for FE analysis by simulating fluid flow & heat transfer which can help understand mechanical deformations in fired pressure vessels.

What we do
Tridiagonal is actively involved in R&D projects and Joint-Industry-Programs (JIP) with global companies. We work with oil and gas industry majors like National oil companies, global owner-operators, Engineering service providers, process equipment designers, and Engineering Procurement Construction(EPC) firms.
- Multiphase Simulation
- Separation
- Blending
- Phase Change
- Crystallization
- Combustion modeling
- Gas and Oil combustion
- Reaction Modeling
Computational Fluid Dynamics
Computational Fluid Dynamics (CFD) empowers you to visualize and analyze complex fluid flow phenomena within your designs. Our team of CFD specialists leverage cutting-edge tools and proven methodologies to provide comprehensive solutions for a wide range of applications, including heat transfer analysis for equipment design, Multiphase flow modeling and Combustion analysis for emission control. We are trusted partners of renowned companies since last two decades. We work on a wide range of applications making considerable contributions to design & process optimization.
.jpg?width=398&height=393&name=Computational%20Fluid%20Dynamics%20(CFD).jpg)

Our CFD engineers can analyze oil blending & suggest appropriate jet-mixture position for optimal performance. Homogenization time can also be predicted to take inferred decisions. Separation is an essential process in Oil & Gas industry, here we can evaluate and enhance performance of various separation equipment like two/three-phase separators, vertical/horizontal and spherical separators, Cyclone and pre-treaters with simulation.

Tridiagonal has considerable experience on modeling burner arrangements, flame interactions, NOx and SOx predictions and Flame impingement on radiant tube section to avoid rupture. Our engineers also worked on processed heaters used in reformers. We help optimize flow of fluid and air to Burner using CFD as well as improve combustion efficiency by optimizing fuel and air flow

Tridiagonal engineers work on both onshore & offshore oil extraction applications. Our team can analyze pressure drop patterns & erosion modeling of downhole tools using CFD as well as equipment & tools involved in other processes like completion, cementing & plugging and abandonment to understand fluid displacement. Other applications include sand screens, submersible pumps, steel catenary riser(SCR) & exhaust gas dispersion from offshore platforms.

Tridiagonal's CFD capabilities cover a wide range of equipment & processes under oil refining. Our simulation assessment helps solve coking issues in fractionators by tracking particle & liquid distribution. Insights provided from our M&S team are useful in selection of Fixed bed reactors to get improved temperature distribution & flow uniformity.

Through incorporation of coupled FEA-CFD analysis we offer more realistic solutions on various oil & gas equipment. Synergizing both these domains our experts help you solve problems related to Fluid Structure Interaction(FSI) & Thermal Structural interaction.
- Fatigue failure analysis
- Thermal , Static analysis
- Dynamic analysis and Non-linear
- Acoustic induced Vibration
- Buckling Analysis
Finite Element Analysis
Finite Element Analysis (FEA) has become an indispensable technology within the oil and gas industry. This sophisticated computer-aided engineering technique allows engineers to perform simulations of various components and structures and predict their behavior under real-world operating conditions.
This capability to analyze stress, strain, and deformations across a wide range of scenarios strengthens safety protocols, optimizes designs, and ultimately reduces costs throughout production, and transportation phases./p>
.jpg?width=398&height=393&name=Finite%20Element%20Analysis(FEA).jpg)

Our FEA engineers can do static structural analysis to assess the structural integrity of different pressure vessels broadly classified as Vertical Pressure Vessels and Horizontal Pressure Vessels used in Oil refineries. We do these analyses using industry standards like ASME and API for stress classification and ASCE for Seismic analysis. We also frequently analyze separators & coke drums for deformations.

From wellheads to offshore rigs our engineers can perform stress analysis to ensure safe & reliable operations. We can replicate the response of offshore platforms under combined forces of waves, wind, and sea currents. Under energy extraction operations, Tridiagonal works on a wide range of applications including Centrifugal compressors & gate valves.

Leveraging FEA, Tridiagonal can do a static analysis to capture stiffness of Distillation column to avoid collapse due to buckling loads. We have extensive experience in analyzing structural integrity of Storage tanks at component level such as Tank Roof Nozzle, Baffle Plate and bottom plate nozzle.

Tridiagonal engineers have considerable experience in predicting fatigue life of piping by calculating stress intensities at critical locations. We can simulate vortices and acoustic resonances and their effect on pipe wall structure to predict resonance frequency and high stress region in piping structures.

Through incorporation of coupled FEA-CFD analysis we offer more realistic solutions on various oil & gas equipment. Synergizing both these domains our experts help you solve problems related to Fluid Structure Interaction(FSI) & Thermal Structural interaction.
- Drill-bit interaction analysis
- Simulating Wellbore Stability
- Analyzing Fluid-Particle Interactions
Discrete Element Method
FDiscrete Element Modeling (DEM) is a technique used in oil and gas industry for simulating the behavior of granular materials, particularly in drilling processes
.jpg?width=398&height=393&name=Discrete%20Element%20Method%20(DEM).jpg)
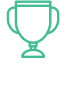
Tridiagonal can simulate how drill bit interacts with the rock formations at various depths. Our engineers predict wear and tear of drill bits, optimize drilling parameters, and improve drilling efficiency.
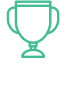
Wellbore instability can cause significant problems during drilling. Tridiagonal can model the movement of formation particles around the wellbore, helping to predict potential wellbore collapse and design strategies to prevent it.
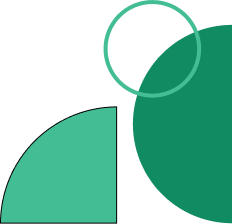
- Predictive model based on Experimental and Simulation data
- Response Surface Models
- Reduced Order Modeling
- Fluid Structure Interaction
- Thermoelectric Interaction
- CFD-DEM coupling
- Acoustic structural interaction
- DEM-FEA coupling
Use Cases
At Tridiagonal, we pride ourselves on staying at the forefront of technological advancements. Our team is dedicated to incorporating the latest applications in Oil & Gas, such as hydrogen production, storage, and transportation, into our consulting services. By leveraging state-of-the-art simulation tools, we empower our clients to navigate the evolving energy landscape with confidence. To learn more about our experience of CFD & FEA please refer our case studies.
Why Tridiagonal?






Looking for Trusted Partner for executing your programs?
We bring together unparalleled expertise with combination of skillsets and technology to address your digital, computational and testing needs