Dx in Process Manufacturing
Industry Overview
In the face of rising global demand for raw materials, the metals, minerals, and cement industry faces the challenge of handling dynamic demand patterns while prioritizing environmental responsibility and cost reduction. Digital technologies become a key enabler to optimize processes intricately. AI algorithms analyze vast amounts of data to identify inefficiencies, predict equipment failures, and optimize production schedules, leading to reduced energy consumption, minimized waste, and increased resource efficiency. This fosters sustainable production practices while enhancing operational performances, profitability and ensures competitiveness in an ever-evolving market landscape.
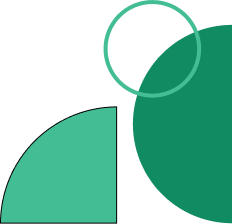
Dx Opportunities
The convergence of digitization, vast data volumes, and large-scale operations presents an expansive opportunity. Despite the expanding potential, this sector faces disparity between digital aspirations and actual implementation impacting the digital effectiveness. Tridiagonal specialize at implementing these technologies at scale and helps can unlock the full potential of their operations, by driving efficiency, innovation, and environmental stewardship simultaneously.
Leverage predictive models to reduce the carbon footprint of the overall processing facility by maintaining the optimal consumption of fuel and other resources such as water, steam and air
Energy optimization of air compressors, CIP cycle water consumption optimization, Optimization of chillers, Energy consumption optimization for critical drives.
Energy Management
Energy prediction and management across site including the utilities is key for improving the overall energy efficiency of the operations. For a production facility, it is important to operate at the optimal level to ensure that overall energy, steam, water consumption per unit production are minimum as per the predictions. Tridiagonal solutions tailored frameworks enables the organizations to have a deeper and meaningful insights about energy KPIs across the facilities. Thes solutions are curated to deliver the best-in-class solution to bring about the visibility of various energy sources and sinks using the hybrid approach leveraging first principles and data driven techniques.
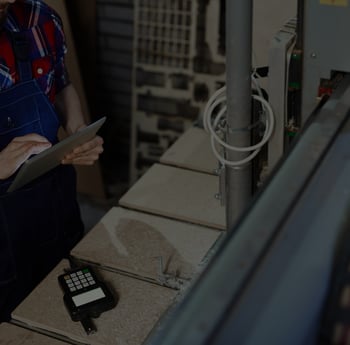
KPIs such as steam to fuel ratio is an important metric to allow the frameworks to identify the opportunities for optimization. Correlate the best possible fuel combination strategy with the predicted CV against the target steam production.

Changeovers and workovers in the batch operations are critical to determine the performances of the future production. It is important to manage the effectiveness of the steam and solvent cleaning to ensure the consumption of the resources are consumed optimally without compensating on the quality and production targets

Monitor the emission across the operations against the benchmark emission and specific energy consumption. Correlate the emissions against the set of operating variables to improve the control strategy to keep the emissions at the best possible level
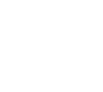
Track and monitor the steam efficiency at equipment and site level operations. Predict the required amount of steam using first principles and benchmark it against the actual steam consumption. Track the overall steam economy across various unit operations and process across site, starting with Boilers to turbines and reactors in processing facilities.

For more details on the use cases focusing on energy, steam, water and other resources please click here.
Improve the availability, maintainability of critical assets through the digital intervention. Improve the performance of batch reactors, motors, compressors and heat exchangers
Compressors performance prediction, Predictive maintenance of heat exchangers, bearing failure prediction motors, Asset utilization and OEE
Predictive maintenance
Maintaining the availability for the desired period of uptime is one of the most important task for the production to run continuously to meet the market requirements. Critical assets spans from compressors to exchangers to reactors and ovens. Unforeseen operating conditions makes it difficult for the operators to understand the dynamics around the health of the equipment. Several factors including deviations in KPIs to seasonality variations lead to unplanned downtimes in the critical assets. With our expertise in dealing with rotating assets, it has been made possible to leverage the physics augmented data driven techniques to track the anomalies and deviations in the assets which can cause the chances of failures. With the predictions organizations can see multiple benefits in planning the maintenance activities to reducing the overall inventory costs.
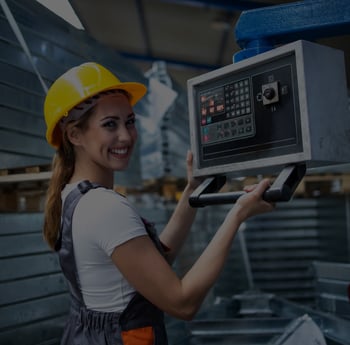

Process and air compressors are one of the most critical operations to ensure the production is met at their desired level of targets at minimum operating cost. Using this solution reliability team can predict the performance (Isentropic and polytropic) and health in real time. These modules helps the team to predict the possibilities of failures with the deeper insights about the failure modes and prescriptions.
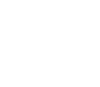
Critical failures due to fouling of the tubes can lead to large unplanned downtimes accounting for production losses. Using first principles and thermodynamics estimation of the fouling level against the best operating regime and the minimum level of operations can be established. This approach when scaled across the train of heat exchangers can help the maintenance team to plan and prioritize the maintenance activities for the critical equipment.

Using the batch unfolding techniques, transform the times series parameters to batch wise sequences. Correlate the transformed dataset with the health score of the batch to determine the performance of the next batch providing the information about the maintenance needs required before next production batch.

For CPG manufacturers maintaining the availability of the batch assets is second to none. Maximum availability enables them to produce more with the same resources. OEE and utilization KPIs derived based on predictive algorithms provides the visibility of the these in real time and allows the operators to continuously improve their operations.
Using non-linear inferentials for predicting the feed, fuel and product quality in real time. Prediction of batch product quality with consideration of the feed stock changes and operating conditions in real time to ensure the quality specifications are met
Prediction of product yield in batch reactors, Prediction of water quality in cooling tower operations
AI based inferentials
Quality management for various entities including feedstocks to fuels and product is important to produce with satisfactory level of quality standards. Most of quality variables are recorded based on the lab sampling at certain low frequent intervals, which makes it difficult for the control room operators to take the real time corrective actions. With inferential modeling process operators can gain deeper insights about the set point control changes required for achieving the optimal quality specifications. Physics driven inferentials can enable with real time prediction of quality variables for critical batch, drying and other processes.
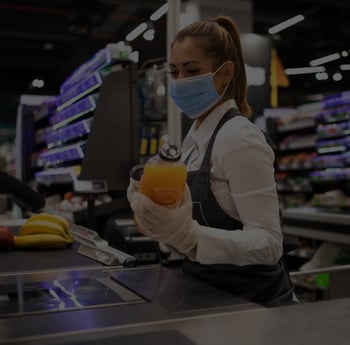
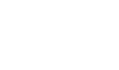
Using physics-based AI to predict the quality parameters such as yield and conversion in real time. Model using the historical low frequency lab reading against the set of operating variables to develop the correlation between the two. Use the recommended changes in the set points to control the quality variations.

Predict the %LOD in real time to estimate the moisture content in real time. Prediction of LOD with respect to the initial moisture content using physics incorporated AI models allows the operators to make changes to the operating conditions while batch is in progression. This helps the manufacturers to reduce the batch rejections.

Multi-effect evaporators are important to concentrate the solvent to desired levels at optimal consumption of steam. Overall economy of steam depends on the steam consumed to production achieved with specified product concentration. AI predicts the concentration in real time at various operating conditions helping to minimize the iterations to resort at the right combination of input parameters.
Minimize the grade transition period and product off-specifications through AI based prescriptive analytics. Operate at the maximum possible efficiency with optimal cycle time in order to improve continuously.
Raw material consumption optimization, golden batch analytics, OEE, Yield improvement
Process optimization
Minimize the grade transition period and product off-specifications through AI based prescriptive analytics. Operate at the maximum possible efficiency with optimal cycle time in order to improve continuously. Optimize the cycle time and yield of batch and continuous processes through AI-based optimization toolbox. Leverage the AI based simulators to continuously identify the opportunities to optimize the control strategy to meet the desired product specifications at minimum operating costs.


Cycle time optimization paves the way to identify the opportunities to improve the operations. AI with the embedded information about the batch recipe enables tracking of the KPI deviations in real time. Operators can benchmark the real time batch activities against the threshold duration to correct the deviations in real time to prevent batch rejections and optimize the batch KPIs
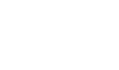
Hybrid models enables physics informed AI to identify the opportunities in improving the product yield in real time. Model captures the non-linearities, intermittent feed addition to dynamically recommend the set point changes to predict the incremental yield.
Batch operations demand for optimal raw material utilization, optimal cycle time and optimal levels of yield. Golden batch analysis allows the operators to benchmark the batch KPIs against the best historical batches enabling them to run at the closed possibility against the golden runs.
Leverage the zero shot and few shots LLMs to interpret and analyze the unstructured dimensions. Integrate the interpretation from quality reports, product compliance report, incident reports and many others for improving the productivity and gaining deeper insights about the operational dynamics.
Alarm report analytics, RCA/Incident reports correlation with real time process anomalies, conversational AI for real-time production information.
Generative AI
More than a quarter of data remains unused as it becomes difficult to access and interpret them due to its unstructured and non-standard formats. Documentation spans from raw materials information, production reports to quality and compliance records. Generative AI can be leveraged to automate the interpretation of the information using the zero shot and few shots LLMs to interpret and analyze the unstructured dimensions. Integrate the interpretation from quality reports, product compliance report, incident reports and many others for improving the productivity and gaining deeper insights about the operational dynamics.
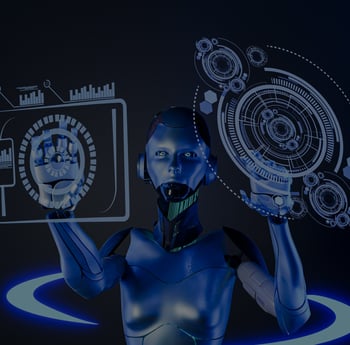

In order to continuously improve the batch performances it is important to extract many unstructured information such as visual and physical characteristics of the product. Usually such information are available in siloed unstructured documents. LLM models can be leveraged to extract and derive meaningful insights from these documents to provide the intelligence to the operations team

Alarms are critical to be monitored and categorized in several priorities. With the LLMs unstructured alarm reports can be segregated based on its criticality and frequency. These models can augment advanced analysis intelligence to estimate and correlate the information with process parameters

Improve the interpretability with meaningful insights derived from the historical RCA reports. Real time anomalies can be correlated with the historically similar events with the added intelligence about the indicators and corrective actions.
Use Cases
In the Food, Beverages and CPG industry, digital solutions are critical for addressing increasing difficulties across the value chain. By embracing technology, firms may improve efficiency, streamline operations, and respond to changing market dynamics, assuring long-term growth and competitiveness in today's fast changing world:
Accelerate your Dx transformation projects with Smart Apps and Time-to-value (TTV) program
Integrate ready-to-deploy smart apps with your existing IT-OT infrastructure and scale across plants.
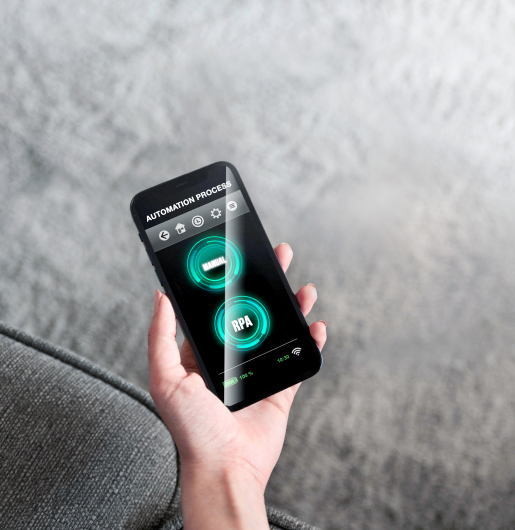
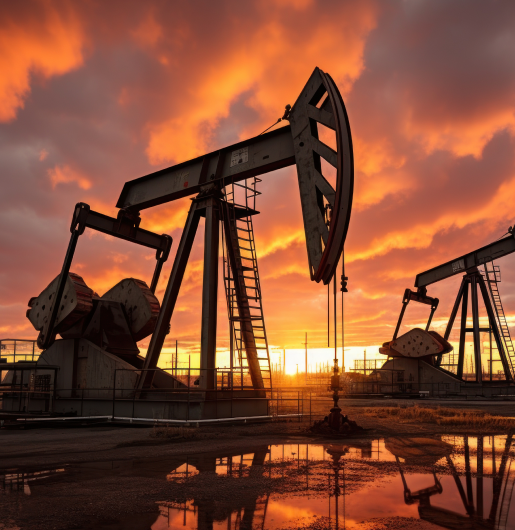
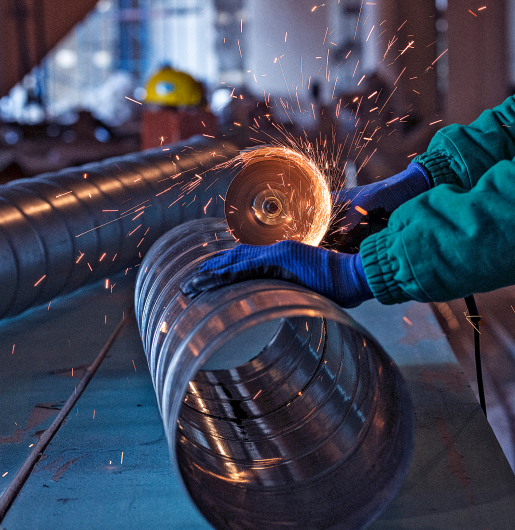
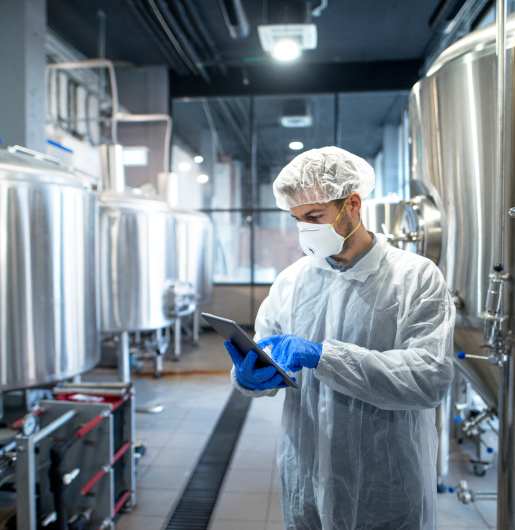
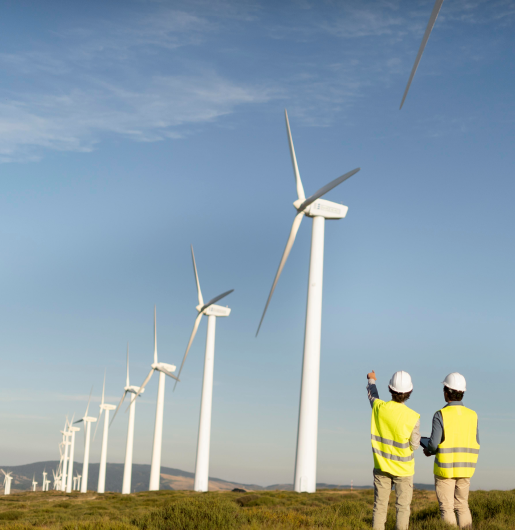
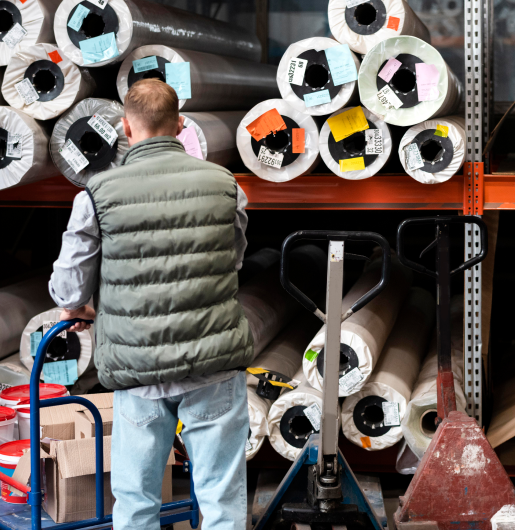
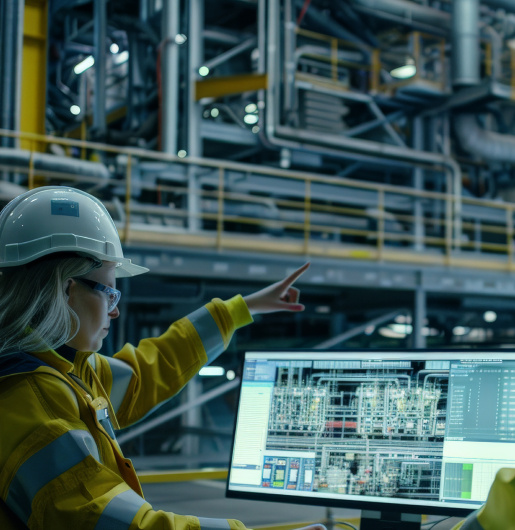
- Smart Apps
- TTV A-33 Program
Tridiagonal Solutions launches ‘Process optimization framework’ for manufacturing industry. We optimize processes for energy, efficiency, quality using cutting-edge technology and engineering expertise. From custom column design to process intensification, we're driving innovation for a sustainable future.
Leveraging these frameworks allows the industry to implement the ML models at scale.
Time to Value program leverages advanced scalability frameworks to deliver superior analytics solutions to manufacturing industries. Designed for rapid implementation, our program ensures larger delivery with unparalleled speed and efficiency. By utilizing scalability frameworks, we significantly reduce the time and cost associated for standard approaches. and accelerates deployment, allowing manufacturers to quickly gain insights and drive improvements in their operations. With our program, clients benefit from faster, data-driven decision-making, enhanced productivity, and a swift return on investment, making it the optimal choice for modern manufacturing analytics projects.
Why Tridiagonal?






Team having exposure and expertise of developing scalable solutions across multiple platforms.
Looking for Trusted Partner for executing your programs?
We bring together unparalleled expertise with combination of skillsets and technology to address your digital, computational and testing needs