Power & Renewables
Harness the power of Computational Modeling for Optimal Performance.
Advance Modeling & Simulation (CFD/FEA)
Industry Overview
Increased global power demand is driving companies to develop new processes towards improvement in efficiencies, increase in generation capacities and decrease in the overall environmental impact. Our services are used extensively within the power generation industry segment. Computational Fluid Dynamics (CFD), Discrete Element Modeling (DEM)& Finite Element Analysis(FEA) methods are used to simulate and predict fluid and solid flows, heat/mass transfer, chemical reactions & stresses. Based on solid research and application experience, Tridiagonal has developed the expertise to create computational models of various unit operations in a power generation facilities that correlate well to pilot and plant measurements.
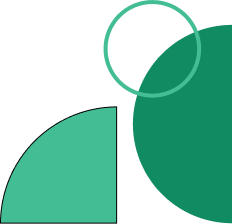
What we do
Tridiagonal has expertise in modeling a wide range of feed stocks – coal, bagasse, biomass, heavy oils, natural gas and mixed fuels. We also have expertise in modeling all of the key unit operations –feed processing and transport systems, combustion units, heat recovery and pollutant control systems. We have considerable experience on assessment of Boiler structural integrity as per industry standards like ASME. Recent regulations on NOx reduction have re-emphasized the need to improve the efficiency of the combustion processes. We are involved in numerous projects across the industry related to NOx reduction.
Tridiagonal assists clients in identifying correct process applications that benefit from CAE(CFD, DEM & FEA) modeling solutions to address routine problems in power generation industry..
- Combustion modeling
- Phase change modeling
- Optimal Scrubbing
- Flow optimization
Computational Fluid Dynamics
Computational Fluid Dynamics (CFD) empowers you to visualize and analyze complex fluid flow phenomena within your designs. Our team of CFD specialists leverage cutting-edge software and proven methodologies to provide comprehensive solutions for a wide range of applications in Power industry, including heat transfer analysis for product design and combustion analysis to predict flow & temperature distribution for example in HRSGs providing insights into emission control. We are trusted partners of power plant operators, engineering procurement construction(EPC) companies & engineering service providers. We cover a wide area of applications where we are significantly contributing at design, process optimization and troubleshooting.
%20(3).jpg?width=350&height=346&name=Computational%20Fluid%20Dynamics%20(CFD)%20(3).jpg)
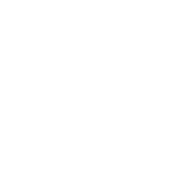
Our CFD engineers can model several units involved in Power generation to get a deep insights into internal processes to improve overall performance & retrofitting. Tridiagonal has considerable experience in modeling Flue Gas Desulphurization(FGD), Heat Recovery Steam Generator & Sulphur Recovery unit.

Tridiagonal has considerable experience in modeling burner arrangements which helps achieve more complete combustion, low pollution levels, flame stability and low thermal Stresses.
Our engineers predict pressure drops which help analyze poor flow distribution of flue gas in order to avoid wear & tear of ducts in Air pre-heaters. We are using CFD to predict effects of electric field on particle inside Electrostatic Precipitators(ESPs).
Using both CFD and FEA, Tridiagonal can help you with complete solutions for engineering problems related to different Power Generation equipment. Synergizing both these technologies our tech experts help you solve problems related to Fluid Structure Interaction(FSI) & Thermal Structural interaction.
- Structural Integrity assessment
- Seismic assessment
Finite Element Analysis
The power generation industry thrives on efficiency and reliability. From conventional fossil fuel plants to cutting-edge renewable sources, ensuring the structural integrity and performance of critical components is paramount. Tridiagonal has considerable experience to provide valuable insights using Finite element Analysis to meet the requirements of plant operators and equipment designers.
.jpg?width=350&height=346&name=Finite%20Element%20Analysis(FEA).jpg)
Identify areas prone to excessive stress or strain in critical components like turbine blades, Boilers and pipelines. Our engineers do these types of analyses using standard like ASME Section VIII and Division 2.

To achieve better strength to weight ratio, now industry is moving towards Fiber reinforced plastics from steel to construct tower structures. Our FE analyst does seismic assessment as per ICC EC AC 156 code. Here, earthquake loading that the cooling tower would have to sustain is replicated by performing response spectrum analysis.
As turbines spin at very high speeds, minor imbalances or vibrations can become magnified at these speeds, leading to catastrophic failures. Our FEA engineers can study the excessive vibrations at extremely high speeds by performing rotor dynamic analyses in order to prevent failures.

Blade undergoes various loading like gravity, centrifugal forces due to rotation and static pressure developed across inlet and outlet, studying these factors our FEA engineers analyze the root cause of failure.
- Digital Replication for quick assessment
- Response Surface Models
- Reduced Order Modeling
- Fluid Structure Interaction
- Thermal Structural interaction
Multiphysics Simulation
Power generation equipment involves complex interplay between fluids like gases or water and the structures that contain them. Traditional FEA might analyze stresses, but without considering the fluid's influence like pressure & heat transfer. Similarly, CFD might analyze flow patterns, but wouldn't account for how the structure itself deforms under those forces. Tridiagonal can bridge this gap by coupling both technologies.
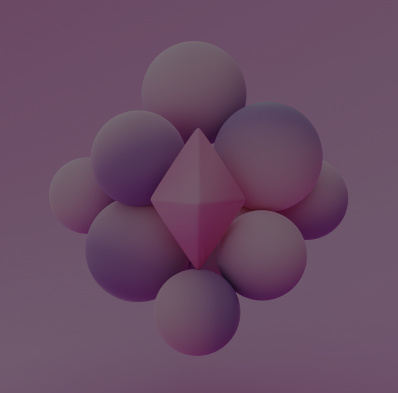
Thermal expansion and contraction can lead to stress and fatigue in boiler tubes and heat exchanger components. Our CFD engineers model the fluid flow and heat transfer within the boiler or heat exchanger. While our FEA engineers can then analyze the resulting thermal stresses and predict areas susceptible to failure or deformation.

Uneven temperature distribution and thermal stresses are observed in incinerator combustion chambers. Our engineers use CFD to simulate the combustion process and heat distribution while FEA, is used to assess the structural integrity and also to identify areas of high stress due to thermal gradients.
Wear and tear on conveyor systems, hoppers, and chutes is observed due to the abrasive nature of coal particles. Tridiagonal Discrete Element Method(DEM) engineers can simulate the movement and interaction of coal particles, while using FEA the structural wear and tear on the handling equipment can be assessed.

For more details on the use cases please click here.
Use Cases
At Tridiagonal, we strive to stay at the forefront of technological advancements. Our team is dedicated to incorporating the latest developments in Power generation, such as underground coal gasification & waste to energy incineration into our consulting services. By leveraging state-of-the-art simulation tools, we empower our clients to navigate the evolving energy landscape with confidence. To learn more about our experience of CFD, DEM and FEA in detail, please refer our case-studies.
Why Tridiagonal?

Successfully delivered 1000+ projects

25+ experts having masters & PhDs

Flexible options including time and material, dedicated centers, and project-specific engagements

To solve complex problems, we use CFD, FEA and DEM or respective coupling

We are proficient in using tools like OpenFoam, ANSYS, STAR-CCM+, LS Dyna and Rocky

Automating processes from geometry creation to Simulation in Simcenter 3D
Looking for Trusted Partner for executing your programs?
We bring together unparalleled expertise with combination of skillsets and technology to address your digital, computational and testing needs