Food, Beverages & CPG
Simulating Flavor, Engineering Success: CFD Solutions for Food, Beverage, and CPG Innovation.
Advance Modeling & Simulation (CFD/FEA)
Industry Overview
CFD offers opportunities in the Food & Beverage and Consumer Packaged Goods industries by optimizing processes like mixing and packaging, ensuring food safety through airflow simulations, aiding product development, supporting sustainability goals, and enhancing quality assurance and compliance efforts. It improves efficiency, product quality, and sustainability while ensuring regulatory compliance.
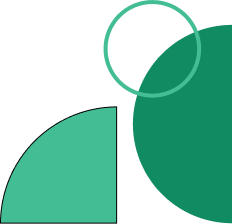
Simulation Opportunities
Tridiagonal is actively involved in R&D projects and Joint-Industry-Programs (JIP) with global companies. Following are the Simulation Opportunities to collaborate with us.
- Food Processing Optimization
- Product Development and Innovation
- Quality Assurance and Compliance
- Sustainability Initiatives
- Heat Transfer in Thermal Processing
Computational Fluid Dynamics
CFD offers opportunities in the Food & Beverage and Consumer Packaged Goods industries by optimizing processes like mixing and packaging, ensuring food safety through airflow simulations, aiding product development, supporting sustainability goals, and enhancing quality assurance and compliance efforts. It improves efficiency, product quality, and sustainability while ensuring regulatory compliance.
.jpg?width=398&height=393&name=Computational%20Fluid%20Dynamics%20(CFD).jpg)
.png?width=176&height=176&name=Deep%20learning%20process%20control%20(minute%20by%20minute%20optimization).png)
CFD can be used to simulate and optimize various food processing operations such as mixing, blending, heating, and cooling. By modeling fluid flow, heat transfer, and mass transfer within processing equipment like mixers, blenders, heat exchangers, and ovens, manufacturers can improve efficiency, reduce energy consumption, and ensure uniform product quality.

CFD can be used in the development and optimization of new food products and processes. For example, it can simulate fluid flow and heat transfer in food extrusion processes to optimize product texture and quality, or model fluid dynamics in packaging systems to develop innovative packaging designs that enhance product freshness and appeal.
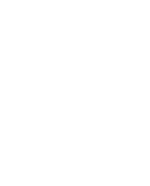
CFD can aid in quality assurance and compliance efforts by simulating fluid flow and heat transfer in food processing equipment to ensure compliance with regulatory standards and industry guidelines. It can help identify potential areas of concern, such as hot spots or uneven heating, and optimize processes to ensure consistent product quality and safety.
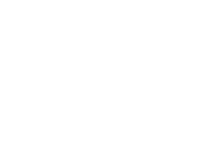
CFD can support sustainability initiatives within the F&B and CPG industries by optimizing processes to reduce water and energy consumption, minimizing waste generation, and improving overall process efficiency. By modeling fluid flow and heat transfer in manufacturing processes, companies can identify opportunities for resource conservation and environmental impact reduction.
In industries like dairy and beverage, CFD can help optimize heat exchanger designs and thermal processing conditions to ensure product safety and quality while minimizing energy consumption.
- Powder Handling and Processing
- Product Development and Innovation
- Food Processing Equipment Design
- Ingredient Mixing and Segregation
- Safety and Hygiene Compliance
Discrete Element Method
DEM presents numerous opportunities for optimization and innovation in the Food & Beverage (F&B) and Consumer Packaged Goods (CPG) industries. It allows for simulating granular material behavior, aiding in processes like powder handling, packaging design, equipment optimization, ingredient mixing, and supply chain management. DEM facilitates product development, quality control, safety compliance, and troubleshooting, leading to enhanced efficiency, quality, and competitiveness in these industries.
.jpg?width=398&height=393&name=Discrete%20Element%20Method%20(DEM).jpg)
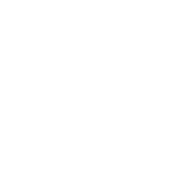
DEM can simulate the behavior of granular materials such as powders, grains, and particles during handling, mixing, conveying, and processing operations. In the F&B and CPG industries, this is particularly relevant for optimizing processes like powder blending, tablet pressing, packaging, and bulk material handling.

DEM can aid in the development of new food products and formulations by simulating how ingredients interact and behave during processing and packaging. This allows for faster prototyping, optimization of recipes, and identification of potential issues before physical trials.
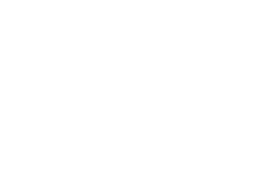
DEM can be used in the design and optimization of food processing equipment such as mixers, mills, crushers, and extruders. By simulating particle behavior and interactions within these machines, engineers can improve performance, reduce energy consumption, and minimize wear and tear.

DEM enables the analysis of mixing processes to ensure uniform distribution of ingredients and minimize segregation effects. This is crucial for ensuring product consistency and quality in applications like baking, confectionery, and snack manufacturing.

DEM simulations can also be utilized to ensure compliance with safety and hygiene regulations by evaluating the risk of contamination, dust generation, and product degradation during processing and handling operations.
- Equipment Design and Optimization
- Heat Transfer Analysis
- Product Development and Innovation
- Fluid Flow Analysis
- Safety and Compliance
Finite Element Analysis
FEA plays a vital role in the Food & Beverage and Consumer Packaged Goods industries. FEA aids in designing equipment that can withstand mechanical stresses while enhancing performance and durability. Moreover, it plays a crucial role in analyzing heat transfer and fluid flow, optimizing thermal systems and ensuring efficient processing. Overall, FEA proves instrumental in enhancing efficiency, safety, and compliance across various stages of production, packaging, and distribution in these industries.
.jpg?width=398&height=393&name=Finite%20Element%20Analysis(FEA).jpg)
In food processing plants and beverage manufacturing facilities, equipment such as mixers, conveyors, and storage tanks are subjected to various mechanical stresses. FEA can aid in the design and optimization of such equipment to enhance durability, reliability, and performance.

FEA can be utilized to analyze heat transfer phenomena in food processing equipment such as ovens, refrigerators, and pasteurizers. This helps in optimizing the design of thermal systems to ensure efficient heating or cooling of food products while maintaining uniform temperatures and minimizing energy consumption.

FEA can play a crucial role in the development of new food and beverage products by simulating mechanical interactions during processing, packaging, and distribution. It aids in predicting product behavior under different conditions and optimizing formulations to meet desired performance criteria.

FEA coupled with CFD can be employed to simulate fluid flow behavior in food processing equipment like pumps, valves, and piping systems. This enables engineers to optimize flow patterns, minimize pressure losses, and ensure hygienic processing conditions.

FEA can be used to assess the safety and compliance of food processing equipment and packaging materials with industry standards and regulations. It helps in identifying potential hazards, mitigating risks, and ensuring product quality and consumer safety.
- Fluid Flow Optimization
- Improved Mixing Efficiency
- Product Design Optimization
- Packaging Optimization
- Heat Transfer Analysis
Process Optimization
Process Optimization enables improvements in fluid flow, particle behavior, and structural integrity, leading to cost savings, enhanced product quality, and operational efficiency. It also supports innovation by allowing virtual testing of new designs and formulations.
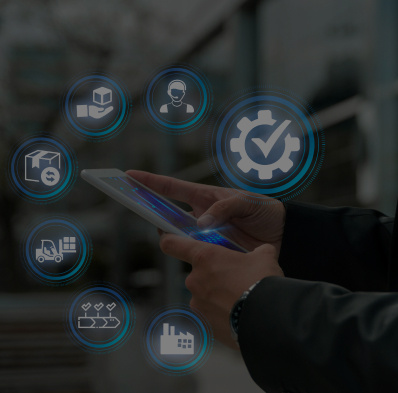
CFD can simulate fluid flow, heat transfer, and mass transfer within various process equipment such as mixing tanks, reactors, and heat exchangers. By optimizing fluid flow patterns, F&B and CPG manufacturers can improve mixing efficiency, reduce energy consumption, and ensure uniform distribution of ingredients.

DEM coupled with CFD can optimize mixing processes by simulating the interaction between fluid flow and particle motion, leading to improved mixing uniformity and reduced processing times.
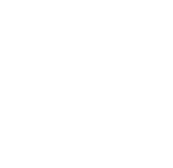
FEA can optimize the design of equipment components and packaging materials to withstand mechanical stresses and optimize performance while reducing material usage and manufacturing costs.

CFD can simulate airflow around packaging designs to optimize shelf life, reduce packaging material usage, and minimize transportation costs.
CFD can analyze heat transfer mechanisms within processing equipment to optimize thermal processing conditions such as pasteurization, sterilization, and drying. This ensures consistent product quality and safety while minimizing energy usage.
Use Cases
At Tridiagonal, we pride ourselves on staying at the forefront of technological advancements. Our team is dedicated to incorporating the latest developments in the Food & Beverage and CPG industry, such as mixing analysis, product development and ensuring food safety by leveraging state-of-the-art simulation tools into our consulting services. To realize our experience of CFD, DEM, FEA and Process Optimization in detail, please refer our case-studies.
Why Tridiagonal?

Proven track record of working for more than two decades in space of CAE consulting

30+ experts having masters & PHD

Flexible options including time and material, dedicated centers, and project-specific arrangements

Coupling of CFD, FEA & DEM gives a holistic approach of problem solving

We are astute at using tools like Openfoam, ANSYS, Star CCM+, LS Dyna and Rocky,

Capable to develop a dedicated GUI to run higher number simulation in single area.
Looking for Trusted Partner for executing your programs?
We bring together unparalleled expertise with combination of skillsets and technology to address your digital, computational and testing needs