Advance Modeling & Simulation (CFD/FEA)
Industry Overview
Tridiagonal has considerable experience to work for Steel, Aluminum & Cement manufacturers. As these manufacturing processes are so complex and carried out using complex equipment. It is necessary to have a deep understanding of process dynamics for efficient performance. Tridiagonal engineers can provide you insights using cutting edge simulations technologies like CFD, FEA & DEM. We are working with renowned Steel, aluminum & cement manufacturing plants and plant erecting companies to facilitate troubleshooting & analyzing root cause of failure
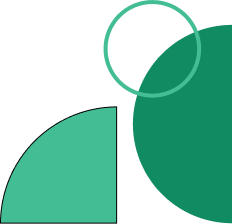
What we do
Tridiagonal has wide range of applications for Cement industry. Our CFD engineers can optimize Kiln design by studying heat transfer & modeling burner arrangements and flow in Cyclone pre-heater & calciner. We can also model flue gas cleaning systems like ESP & Bag filter to achieve better emission control. Our FEA engineers predict failure points by evaluating different types of stresses in Kiln & Mills. Also, we do structural integrity assessment of Silos to avoid potential collapse.
For Metal producing industry our capabilities are extended to model electromagnetic forces induced in metal baths
- CFD modeling of Kiln
- Flow optimization in flue gas cleaning systems,Cyclone Preheater & calciners
- FE analysis to predict failure points of kiln shell & silos
Cement Industry
The cement industry is a vital backbone of global infrastructure, providing the essential building blocks for everything from roads and bridges to houses and skyscrapers. However, traditional production methods are often energy-intensive, resource-heavy, and prone to inefficiencies. To navigate these challenges and ensure sustainable growth, Tridiagonal Solutions can support them through cutting edge technologies like CFD(Computational Fluid Dynamics) & FEA(Finite Element Analysis). Our engineers are capable to address complex engineering problems with their exclusive analytical and mathematical skills. Having good hands on several latest CAE(Computer Aided Engineering) tools, we support for root cause analysis and troubleshooting.
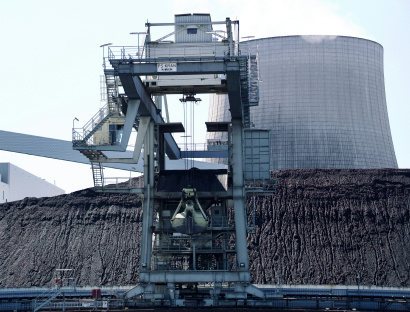

Rotary kiln carries very complex processes inside, so to enhance performance there is a need of deeper understanding & analysis of all processes happening internally. Our CFD engineers can predict fluid flow, heat transfer, mass transfer, chemical reactions, and related phenomena by solving the mathematical equations to detect bottlenecks & energy consumers. We can simulate what-if scenarios to reduce emission. Tridiagonal can evaluate ovalization in kiln using static Structural analysis.

Calciner unit is used for fuel combustion, heat exchange, and decarbonation in Cement production line. Our CFD analysis provide guidelines to enhance heat transfer. It also gives details about mass and energy profile that facilitates the troubleshooting.

An electrostatic precipitator (ESP) is a particulate collection device that removes particles from a flowing gas. ESP tend to be highly efficient filtration systems as they directly induce the charge on the particulate matter. The present work is based on customization of FLUENT’s particle modeling capabilities for simulation of ESP
- Combustion Modeling of Blast furnace
- Thermal analysis of blow pipe
- Ensuring optimal molten metal flow through tundish
- DEM for coal Hoppers & conveyer systems
Steel Industry
Steel alloy-making process includes phenomena like fluid flow, heat transfer, and chemical reactions. Tridiagonal can help steel makers to visualize process dynamics with expertise in Computational Fluid Dynamics(CFD) and Discrete Element Methods(DEM) for efficient operations. Our engineering team has experience to work for Big brands in this industry to replicate equipment like blast furnace, Fired boilers, blow pipe tundish and Coal transport and handling systems. Our recommendations are used for the optimization of complex designs and processes.
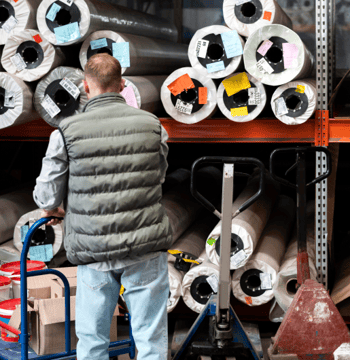
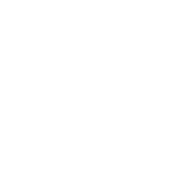
Due to high temperature, presence of liquid metal and high quantity of hazardous CO gas, there is limited scope to understand internal state of blast furnace by measurements. Computational Fluid Dynamics(CFD) is a technology that can provide insights of various process and operational parameters and also helps Operation engineers to improve fuel efficiency and reduce environmental impact.
Our engineers use flow model to analyze Gas, solid and liquid flows, Interphase exchange terms to predict reaction kinetics and phase change modeling for melting to predict temperature distribution for all phases and coal-ore layer.
In the steel industry, various equipment is used for coal transport and handling operations such as Hoppers and Conveyor Belts. Therefore, it is important to study flowability of material, Material clogging at transfer and wear of bottom belt. Our engineering team can help steel plant operators to meet this requirement using Discrete Element method. In this methodology we analyze calibrated angle of repose with the same moisture content and particle diameter with varying the coefficient of friction and cohesive energy
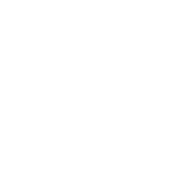
Many quality problems that originate during continuous casting can be directly attributed to poor control of fluid flow conditions. Tridiagonal CFD team can validate tundish fluid flow by simulating scaled water model. Here, the Residence time distribution (RTD) is calculated using species transport model and also roughly estimate run time for tracer so that complete tracer would exit fluid domain.

Dynamic finite element analysis (FEA) is conducted on the complex structure of a screener. Simulating the screener's motion through FEA is crucial, followed by a discrete element method (DEM) analysis aimed at enhancing its performance. This method enables detailed motion simulations for any machine using FEA. The combination of FEA and DEM offers a strong framework for analyzing and enhancing the functionality of complex mechanical systems, ensuring that our simulations closely reflect real-world conditions and results.
- Analysing electromagnetic forces for stationary metal bath flow
- Thermal & Structural Analysis Results
Aluminum Industry
Alumina to aluminum conversion process need more efficient and cost-effective operations to increase profitability and reducing downtime. There is always a higher chance of equipment failure due high heat and electricity induction. Tridiagonal can provide deep insights to aluminum process industries using technologies like Computational Fluid Dynamics(CFD) and Finite Element Analysis(FEA). Our engineers have extended the expertise to analyze electromagnetic field.
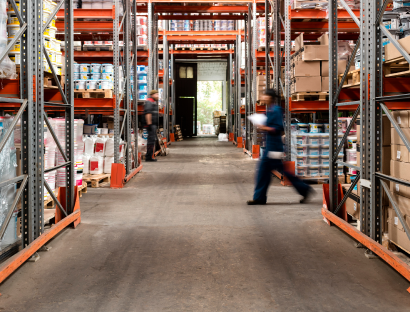
Our FE analyst can estimate stresses induced across electrodes of Aluminum pot cell using convective and radiative boundary conditions. This simulation provides useful insights to avoid thermal fatigue of electrode.

Our CFD engineers can analyze effect of electromagnetic field and electric currents within metal-bath interface to analyze interface deformation of aluminum reduction cell. Here, liquid electrolyte layer (bath), which is floating on top of the liquid metal due to density difference is considered as two-phase system of immiscible liquids. Top wall is modelled as moving deforming wall with position updated based on the dynamic metal-bath interface location while compressible liquid user function is used to model bath liquid density.
- Multiphysics Simulation
- Digital Twin
- Reduced Order Modeling
Multiphysics Simulation
Power generation equipment involves complex interplay between fluids like gases or water and the structures that contain them. Traditional FEA might analyze stresses, but without considering the fluid's influence like pressure & heat transfer. Similarly, CFD might analyze flow patterns, but wouldn't account for how the structure itself deforms under those forces. Tridiagonal can bridge this gap by coupling both technologies.
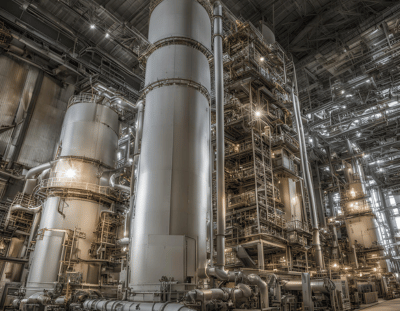

In traditional engineering, each physical phenomenon is often analyzed independently. However, real-world problems rarely occur in isolation. Multiphysics simulation bridges this gap by enabling the simultaneous simulation of multiple interacting physics within a single model. This allows analysts to capture the true essence of complex engineering challenges and achieve more accurate and reliable results.
Our CFD, FEA & DEM engineers use a synergistic approach to develop cutting-edge Modeling & Simulation solutions. Highlighting the potential with two technologies of CFD-FEA and DEM-FEA coupling. Combining CFD & FEA complex interplay between fluids and structures can be simulated to get valuable insights in problems like fluid-structure interaction (FSI)
While coupling of DEM-CFD models the behavior of granular materials interacting with structures. Gain a deeper understanding of stress distribution, particle flow, and potential equipment wear.

Dynamic finite element analysis (FEA) is conducted on the complex structure of a screener. Simulating the screener's motion through FEA is crucial, followed by a discrete element method (DEM) analysis aimed at enhancing its performance. This method enables detailed motion simulations for any machine using FEA. The combination of FEA and DEM offers a strong framework for analyzing and enhancing the functionality of complex mechanical systems, ensuring that our simulations closely reflect real-world conditions and results.

Tridiagonal tech experts can build a virtual replica of assets & processes in various industries to reduce simulation iterations using data interpolation. Methods like CFD, FEA & DEM can predict values that are not possible to gain from sensors.
Our experts can replicate equipment like calciner, Kiln.

Areas where full-scale Simulation is computationally expensive & impractical, Tridiagonal can build ROMs by creating a lower-dimensional model that captures the essential behavior of the system. In Cement and steel making process, there are many complex equipment are involved which will require numerous simulations to understand internal process completely. Here our Reduced order models can remarkably help to reduce simulation time and cost.
Use Cases
Tridiagonal has wide range of applications For Metal & Cement industry. Our engineers have considerable experience of Modeling and Simulations for different applications involved in Steel, Aluminum & Cement production using technologies like CFD, FEA and DEM. Our analyses are useful to enhance overall performance of plant and troubleshooting in case of failures.
Why Tridiagonal?

Proven track record of working for more than two decades in space of CAE consulting

30+ experts having masters & PHD

Flexible options including time and material, dedicated centers, and project-specific arrangements

Coupling of CFD, FEA & DEM gives a holistic approach of problem solving

We are astute at using tools like Openfoam, ANSYS, Star CCM+, LS Dyna and Rocky

Automating processes from geometry creation to Simulation in Simcenter 3D
Looking for Trusted Partner for executing your programs?
We bring together unparalleled expertise with combination of skillsets and technology to address your digital, computational and testing needs