Chemical & Process
Advance Modeling & Simulation (CFD/FEA)
Industry Overview
The Chemical Process Industries team at Tridiagonal specializes in supporting chemical and bioenergy companies by optimizing reactor design, transitioning batch processes to continuous ones, and solving flow, heat, and mass transfer problems in ancillary equipment. We excel in developing high-fidelity process models to reduce R&D costs, minimize environmental impact, conserve energy, and improve corporate profitability.
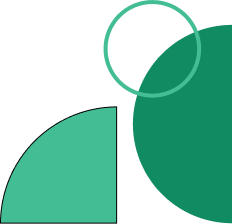
Simulation Opportunities
Tridiagonal is actively involved in R&D projects and Joint-Industry-Programs (JIP) with global companies. Following are the Simulation Opportunities to collaborate with us.
- Mixing Processes
- Scale-Up Studies
- Reaction Engineering
- Fluidized Bed Systems
- Equipment Design and Optimization
Computational Fluid Dynamics
CFD is crucial in the Chemical and Process Industry for simulating fluid flow, heat transfer, and chemical reactions. It optimizes mixing processes, heat transfer equipment, and reactor designs, while also aiding in understanding fluidized bed systems, pollutant dispersion, safety analysis, and equipment design optimization. CFD accelerates development, ensuring operational efficiency and compliance with environmental regulations.
.jpg?width=398&height=393&name=Computational%20Fluid%20Dynamics%20(CFD).jpg)

CFD can simulate the mixing of fluids in tanks, reactors, and pipelines. This is crucial in industries such as pharmaceuticals, food and beverage, and chemical processing, where uniform mixing is essential for product quality and process efficiency.
CFD can aid in scaling up processes from lab-scale to industrial-scale by simulating fluid behavior under different operating conditions and geometries. It provides insights into how process parameters may change with scale, facilitating smoother transitions during process development.

CFD models can simulate chemical reactions occurring within reactors, furnaces, and combustion chambers. By predicting reaction rates, species concentrations, and temperature profiles, CFD aids in optimizing reactor designs and operating conditions for desired product yields and quality.

CFD is widely used to study fluidized bed reactors and dryers commonly employed in the chemical and petrochemical industries. It helps in understanding particle-fluid interactions, heat transfer, and mixing within the bed, leading to improved process efficiency and product quality.
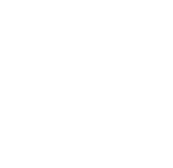
CFD enables engineers to iterate through various designs and operating parameters virtually, reducing the need for costly physical prototypes and experiments. This accelerates the development process and leads to more optimized equipment designs.
- Granular flow simulations
- Particle-particle interactions
- Mixing and blending
- Fluidized bed reactors
- Spray drying and granulation
Discrete Element Method
Discrete Element Method, is widely utilized in the Chemical and Process Industry to simulate the behavior of particulate systems. Its applications include modeling granular flow in equipment like silos and conveyors, studying particle interactions for equipment design, optimizing mixing processes, controlling crystallization, simulating fluidized bed reactors, analyzing spray drying and granulation, optimizing pneumatic conveying, and designing packed beds. DEM enhances process efficiency, reliability, and safety by providing insights into particulate system behavior.
.jpg?width=398&height=393&name=Discrete%20Element%20Method%20(DEM).jpg)

DEM can model the flow of granular materials such as powders, pellets, and grains within processing equipment like silos, hoppers, mixers, and conveyors. Understanding flow behavior is crucial for optimizing processes and preventing issues like blockages or segregation.

DEM helps in studying how particles interact with each other and with equipment surfaces. This is vital for designing equipment with appropriate material properties and surface coatings to minimize wear and abrasion.

DEM simulations aid in optimizing mixing and blending processes by analyzing particle trajectories, mixing efficiencies, and residence times. This is crucial in industries like pharmaceuticals, where homogeneity is critical for product quality.
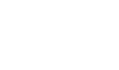
DEM is used to simulate the behavior of particles in fluidized bed reactors, which are widely used in chemical processing for reactions like catalysis, drying, and gas-solid contacting. These simulations help in optimizing reactor design and operation.
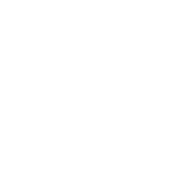
DEM can model the formation of droplets and the behavior of particles in spray drying and granulation processes. This is essential for optimizing particle size distribution, morphology, and process efficiency.
- Structural Integrity Analysis
- Heat Transfer and Thermal Analysis
- Fatigue and Fracture Analysis
- Equipment Design and Optimization
- Chemical Reaction Engineering
Finite Element Analysis
Finite Element Analysis (FEA) is widely used in the chemical and process industry to simulate and analyze complex systems. Its applications include structural integrity analysis of equipment like pressure vessels, thermal analysis for heat exchange optimization, fluid flow simulation for designing pumps and reactors, and modeling chemical reactions. FEA also predicts fatigue life, facilitates multiphysics analysis, aids in equipment design and safety assessment, and contributes to overall process optimization and risk mitigation.
.jpg?width=398&height=393&name=Finite%20Element%20Analysis(FEA).jpg)

FEA can be used to assess the structural integrity of equipment and components such as pressure vessels, pipelines, reactors, and storage tanks. It helps in predicting stresses, strains, and deformations under different operating conditions and loads, ensuring compliance with safety standards and regulations.

In processes involving heat exchange, FEA can model thermal behavior, including conduction, convection, and radiation. It helps in optimizing heat exchangers, reactors, furnaces, and other thermal equipment for efficient heat transfer and temperature control.

FEA can predict fatigue life and fracture behavior of components subjected to cyclic loading or thermal cycling, such as piping systems, pressure vessels, and rotating equipment. It assists in identifying potential failure modes and optimizing designs to enhance durability and reliability.
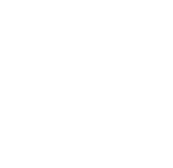
FEA aids in the design and optimization of equipment and systems to meet performance, safety, and regulatory requirements. It facilitates the evaluation of different design alternatives, material selections, and operating conditions before physical prototyping, thereby reducing development costs and time-to-market.

FEA can aid in modeling chemical reactions within reactors and other vessels, considering factors such as kinetics, heat generation or absorption, and mass transfer. This helps in optimizing reaction conditions, reactor design, and scaling up processes.
- Process Simulation and Modeling
- Mixing Processes Optimization
- Fluidized Bed Reactor Design
- Optimization of Distillation Columns
- Reacting Flow Simulations
Process Optimization
Process Optimization plays a vital role in the Chemical and Process Industry. It helps in improving mixing efficiency, enhancing heat transfer, designing fluidized bed reactors, studying pollutant dispersion, optimizing distillation columns, pipeline design, simulating reacting flows, and refining equipment design and scale-up. CFD enables industries to enhance efficiency, reduce costs, and ensure sustainability through detailed fluid flow, heat transfer, and chemical reaction simulations.
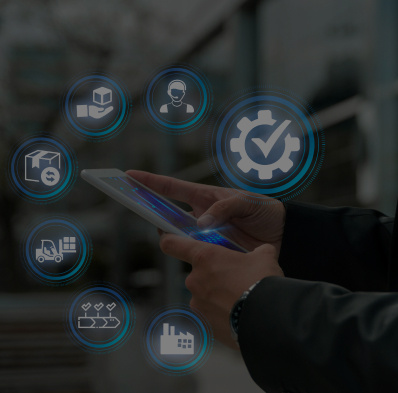
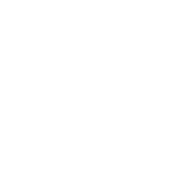
Utilizing CFD software tools to simulate and model chemical processes allows for the analysis of various operating conditions, equipment configurations, and raw material inputs. This helps in identifying the optimal parameters for maximizing production while minimizing energy consumption and waste generation.

CFD simulations can optimize mixing processes by analyzing fluid flow patterns and turbulence within mixing vessels or reactors. This helps in designing efficient mixing systems, reducing energy consumption, and ensuring uniform mixing of reactants, which is critical for chemical reactions.

CFD simulations are used to optimize the design and operation of fluidized bed reactors, which are commonly employed in processes like catalytic cracking and gas-solid reactions. By analyzing particle-fluid interactions and flow dynamics, CFD helps in improving reactor performance, maximizing conversion rates, and minimizing particle attrition.
CFD can model the complex fluid dynamics and heat transfer phenomena occurring within distillation columns. By optimizing column configurations, tray designs, and operating conditions, CFD helps in improving separation efficiency, reducing energy consumption, and maximizing product purity.

CFD can simulate reacting flow systems such as combustion chambers and chemical reactors. By modeling chemical reactions and fluid dynamics simultaneously, CFD assists in optimizing reaction conditions, improving yield and selectivity, and reducing by-product formation.
Use Cases
At Tridiagonal, we pride ourselves on staying at the forefront of technological advancements. Our team is dedicated to incorporating the latest developments in the Chemical and Process industries, such as Product Design and Development by leveraging state-of-the-art simulation tools into our consulting services. To realize our experience of CFD, DEM, FEA and Process Optimization in detail, please refer our case-studies.
Why Tridiagonal?

Proven track record of working for more than two decades in space of CAE consulting

30+ experts having masters & PHD

Flexible options including time and material, dedicated centers, and project-specific arrangements

Coupling of CFD, FEA & DEM gives a holistic approach of problem solving

We are astute at using tools like Openfoam, ANSYS, Star CCM+, LS Dyna and Rocky,

Capable to develop a dedicated GUI to run higher number simulation in single area.
Looking for Trusted Partner for executing your programs?
We bring together unparalleled expertise with combination of skillsets and technology to address your digital, computational and testing needs