Pharmaceutical And Medical Device
Optimizing Processes and Designs for the Pharmaceutical and Medical Device Industry
Advance Modeling & Simulation (CFD/FEA)
Industry Overview
Tridiagonal utilizes advanced modeling techniques like CFD and DEM to support Quality by Design initiatives in Pharmaceutical and Medical Device industries. In Pharma, we specialize in API manufacturing, powder processing, and biologics, aiding in process optimization. In Medical Device, our expertise lies in inhaler and catheter designs, patient-specific modeling, and blood flow analysis. Our focus is on accelerating product development and ensuring quality through precise control of critical parameters.
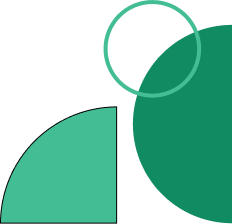
Simulation Opportunities
Tridiagonal is actively involved in R&D projects and Joint-Industry-Programs (JIP) with global companies. Following are the Simulation Opportunities to collaborate with us.
- Product Design and Development
- Drug Delivery Optimization
- Quality Control and Regulatory Compliance
- Medical Device Safety
Computational Fluid Dynamics
Computational fluid dynamics (CFD) offers pharmaceutical and medical device companies numerous advantages. It aids in product design, optimizing drug delivery systems, and ensuring product safety and regulatory compliance. By simulating fluid behavior, CFD enables better device designs, enhances drug delivery efficiency, and supports surgical planning. It also improves bioreactor design for biopharmaceutical manufacturing and assists in quality control processes. Overall, integrating CFD into operations leads to better outcomes, cost savings, and regulatory adherence for these companies.
.jpg?width=398&height=393&name=Computational%20Fluid%20Dynamics%20(CFD).jpg)
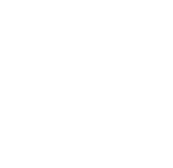
CFD simulations can aid in the design and development of medical devices such as inhalers, drug delivery systems, and surgical tools. By simulating fluid flow, heat transfer, and particle dynamics, companies can optimize product designs for efficiency, safety, and effectiveness.
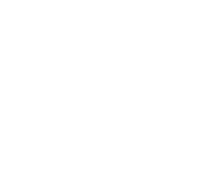
CFD can help optimize drug delivery methods by modeling the behavior of pharmaceutical formulations within the body. This includes simulating drug release from various delivery systems (e.g., inhalers, patches, implants) and predicting how the drug interacts with biological tissues and fluids.
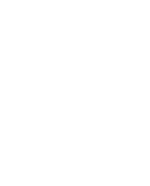
CFD simulations can assist in quality control processes by predicting product performance under various conditions. Additionally, CFD can be used to support regulatory submissions by providing detailed analyses of product behavior and safety.

CFD can assess the safety and performance of medical devices by predicting factors such as blood flow patterns, pressure distributions, and the risk of thrombosis or clotting. This is particularly relevant for devices like stents, catheters, and heart valves.
- Tablet Compression and Coating
- Granulation Processes
- Powder Flow and Handling
- Medical Device Design
Discrete Element Method
DEM offers significant advantages in pharmaceutical and medical device industries by simulating granular material behavior. By simulating the behavior of granular materials and powders, DEM aids in optimizing various processes crucial to pharmaceutical manufacturing and medical device design. This includes tablet compression, coating, and granulation processes, ensuring uniformity and efficiency. DEM also assists in the design of capsule filling systems and powder inhalers, optimizing drug delivery. Moreover, it contributes to the development of medical devices such as implants, inhalers, and drug delivery systems, enhancing their performance and safety. Overall, DEM serves as a valuable tool in the pharmaceutical and medical device industry, improving processes from formulation to manufacturing and packaging.
.jpg?width=398&height=393&name=Discrete%20Element%20Method%20(DEM).jpg)

DEM can simulate the behavior of powders during tablet compression processes, helping to optimize tablet formulation and production. It can also model the coating process to ensure uniform coating thickness and distribution.
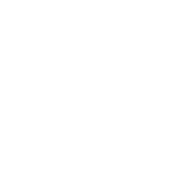
DEM can simulate granulation processes, such as wet granulation and dry granulation, to optimize granule size distribution, porosity, and flow properties of granular materials used in tablet manufacturing.
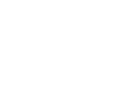
DEM can analyze the flow behavior of powders through hoppers, feeders, and other equipment, aiding in the design of efficient and reliable powder handling systems in pharmaceutical manufacturing
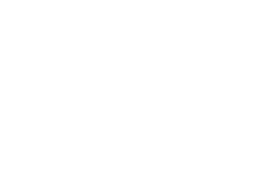
DEM can be applied in the design and development of medical devices involving particulate materials, such as inhalers, drug-eluting stents, and transdermal patches. It can simulate the interaction between particles and device components to optimize performance and ensure safety
- Drug Delivery Systems
- Bioreactors and Fermentation
- Mixing and Stirring Processes
- Heat Transfer Optimization
- Flow through Pipelines and Tubes
Process Optimization
In the pharmaceutical and medical device industry, Computational Fluid Dynamics (CFD) offers significant opportunities for process optimization. Key areas include drug delivery systems, bioreactors, mixing processes, sterilization, cleanroom design, packaging, heat transfer, and fluid flow in pipelines. By simulating fluid dynamics, heat transfer, and mass transport, CFD helps optimize processes for efficiency, quality, and regulatory compliance, reducing costs and time-to-market.
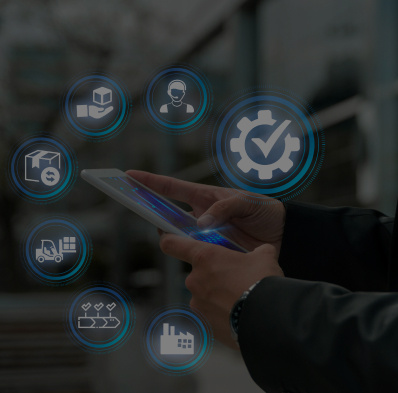
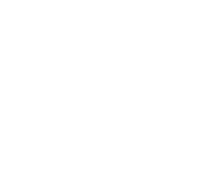
CFD can be used to model and optimize drug delivery devices such as inhalers, nebulizers, and transdermal patches. By simulating the flow of drugs through these devices, manufacturers can optimize designs to ensure effective delivery to patients.
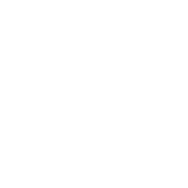
CFD can aid in the design and optimization of bioreactors used for the production of pharmaceuticals, vaccines, and biologics. By modeling fluid flow, heat transfer, and mass transport within the bioreactor, manufacturers can optimize conditions for cell growth and product yield.

CFD can optimize mixing and stirring processes used in pharmaceutical manufacturing, ensuring uniform distribution of ingredients and efficient reaction kinetics. This is crucial for processes such as blending, dissolution, and crystallization.

CFD can optimize heat transfer processes involved in pharmaceutical manufacturing, such as drying, lyophilization, and sterilization. By simulating heat transfer mechanisms within equipment, manufacturers can improve energy efficiency and product quality.

CFD can be utilized to optimize fluid flow through pipelines and tubes in pharmaceutical manufacturing processes, ensuring efficient transfer of liquids or gases while minimizing pressure drops and energy consumption.
- Medical Device Design
- Spray Drying Optimization
- Packaging Design
- Regulatory Compliances
Design Optimization
Computational Fluid Dynamics (CFD) presents multiple Design Optimization opportunities in the pharmaceutical and medical device industry. It can enhance drug delivery systems, bioreactor design, medical device functionality, mixing processes, spray drying, ventilation systems, heat transfer processes, and packaging design. By simulating fluid flow, heat transfer, and other factors, CFD helps improve product efficacy, quality, safety, and cost-effectiveness across different stages of development and manufacturing.
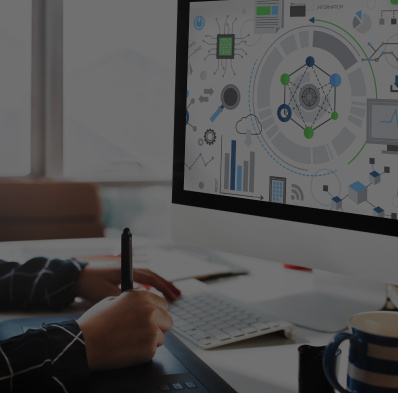
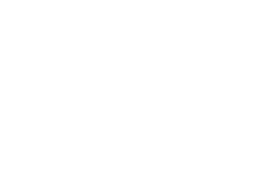
CFD simulations can aid in the design and development of medical devices such as inhalers, drug delivery systems, and surgical tools. By simulating fluid flow, heat transfer, and particle dynamics, companies can optimize product designs for efficiency, safety, and effectiveness.
CFD can help optimize drug delivery methods by modeling the behavior of pharmaceutical formulations within the body. This includes simulating drug release from various delivery systems (e.g., inhalers, patches, implants) and predicting how the drug interacts with biological tissues and fluids.
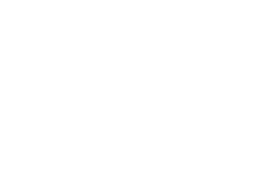
CFD can optimize the design of packaging systems used to store and transport pharmaceutical products. By simulating airflow and temperature distribution within packaging containers, designers can ensure product stability and shelf-life while minimizing packaging material usage and costs.

Computational Fluid Dynamics (CFD) is crucial for regulatory compliance in pharmaceutical and medical device industries. It helps by analyzing airflow and particle dispersion, ensuring adherence to standards. CFD also optimizes ventilation systems, designs containment for hazardous materials, and enhances sterilization processes without compromising product integrity. Ultimately, CFD is essential for meeting regulatory requirements by optimizing processes, facilities, and product designs.
Use Cases
At Tridiagonal, we pride ourselves on staying at the forefront of technological advancements. Our team is dedicated to incorporating the latest developments in Pharmaceutical and Medical devices, such as Product Design and Development by leveraging state-of-the-art simulation tools into our consulting services. To realise our experience of CFD, DEM and Process Optimization in detail, please refer our case-studies.
Why Tridiagonal?

Proven track record of working for more than two decades in space of CAE consulting

30+ experts having masters & PHD

Flexible options including time and material, dedicated centers, and project-specific arrangements

Coupling of CFD, FEA & DEM gives a holistic approach of problem solving

We are astute at using tools like Openfoam, ANSYS, Star CCM+, LS Dyna and Rocky,

Capable to develop a dedicated GUI to run higher number simulation in single area.
Looking for Trusted Partner for executing your programs?
We bring together unparalleled expertise with combination of skillsets and technology to address your digital, computational and testing needs