Technology Validation & Scale-up Centre
& Scale-up Centre
About Practice
Tridiagonal Solutions Pvt. Ltd., leveraging one of the Asia's largest experimentation lab and field-scale flow testing facilities to access indispensable production enhancement data. For over 15+ years, we've been catering to the needs of Fortune 500 companies, to bridge the gap between data and informed decision-making, providing validation and proof of concept for optimal field operations.
About Practice
Tridiagonal Solutions Pvt. Ltd., leveraging one of the Asia's largest experimentation lab and field-scale flow testing facilities to access indispensable production enhancement data. For over 15+ years, we've been catering to the needs of Fortune 500 companies, to bridge the gap between data and informed decision-making, providing validation and proof of concept for optimal field operations.
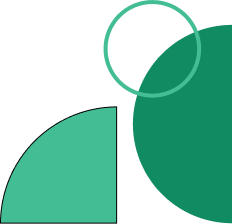
Capabilities
As a distinguished centre of excellence, with a strong process background, a combination of skill sets, and a sturdy partner eco-system, we have been quite capably supporting corporate R&D groups, Process Technologists, Plant Operations, and Maintenance teams with a multitude of services and solutions. We are specialized in a comprehensive range of multiphase flow testing and process optimization ranging from wax and asphaltene deposition, transportation of sand, liquid metal, hydrate & CO2. Our expertise extends to corrosion testing on both lab and pilot scale, Erosion testing for screens, elbows, valves, burst collapse, sand blast, sand retention, ICD testing and new technology scaling up solution form TRL3 to TRL10 for CCUS, H2, and EOR.
Improve the productivity of process by incorporating optimal Wax Mitigation, Asphaltene Management, Sand Management, Liquid Metal, Hydrate & CO2.
Transport, Pipeline Flow Analysis, Flow Regime Identification, Inhibitor Screening, Modeling Validation, Slurry Rheology, and Erosion testing.
Flow Assurance
With a focus on proactive testing and innovative solutions, Tridiagonal Solutions is a trusted partner for smooth flow of operation from reservoir to processing facilities, minimizing downtime and maximizing production efficiency for of oil and gas. Our state-of-the-art facilities allow us to assess and mitigate issues such as wax deposition, asphaltene precipitation, transportation of sand, liquid metal, CO2 hydrate.
.gif?width=768&height=432&name=Blue%20and%20Gold%20Traditional%20Indian%20Wedding%20Save%20the%20Date%20Video%20(7).gif)
Explore our cutting-edge facilities for wax research:
- Pipeline restart, large-scale experiments, and inhibitor impact in Wax Deposition Loop.
- Investigate wax removal, optimize stripping, and mitigate buildup in Wax Testing.
- Holistic exploration in one comprehensive facility.
- Brochure Link
Enhance asphaltene management with our unique global testing facility. We offer:
- Large Pipeline: Assesses asphaltene dynamics in 1-inch or larger pipelines.
- High P&T: 40 barg pressure and 80°C temperature.
- Full Flow Coverage: Ranges from laminar to fully turbulent conditions.
- Custom Strategies: Creates tailored solutions from precise test results.
- Brochure Link
Our capability to mimic the on-field conditions allow us to execute sand transport study at various conditions. We offer:
- Study of well shutdown and well restart phase.
- Critical sand transport velocity in horizontal and inclined wells.
- Sand transport study in oil-water emulsion.
- Brochure Link
For mitigation of mercury accumulation from oil & gas pipeline in hilly terrain, our solution is
- Development of undulating pipeline rig with various inclinations.
- Entrainment of liquid metal at critical gas velocity.
- Visualization of multiphase flow phenomena using high-speed camera.
- Brochure Link
As experts in CO2 hydrate management, our Test Facility offers:
- Analyse hydrate formation under various conditions.
- Assess effectiveness of chemical inhibitors.
- Develop efficient hydrate management techniques.
- Brochure Link
Comprehensive assessment for Component Wear Analysis (Screen, Valve, elbows, joints, pipes, etc), Erosion Resistance Evaluation, Surface Damage Assessment, Erosion Rate Measurement, Validation and Correction of Models, Mechanism Investigation, Protective Coating Performance Testing, Equipment Integrity Assurance, Sand Blast, Sand Retention, and ICD Testing.
Erosion Testing
Our cutting-edge facilities include Screen, Elbow, Valve, and other pipeline components Erosion Testing, along with Burst Collapse, Sand Blast, Sand Retention, and Inflow Control Device Testing. Through rigorous evaluation, we ensure the durability and reliability of oil and gas production equipment in challenging environments.
.gif?width=700&height=394&name=Blue%20and%20Gold%20Traditional%20Indian%20Wedding%20Save%20the%20Date%20Video%20(5).gif)
We offer sand control screen erosion and flow performance testing for both Dry Gas and Slurry.
- Capable to operate at 70 m/s of gas superficial velocity in 4" line.
- Silica flour/sand used as erodent.
- Screen erosion assessed via weight loss, MPP (API 19 SS), microscopic, and light table images
- Brochure Link
- Conduct AICD flow performance, cavitation and erosion test.
- Plugging Test as per API 19 ICD.
- Capable to operate at high pressure of 150 bar with multiphase & single-phase flow, even with high-viscosity fluids
- Brochure Link
- Evaluates sand screen effectiveness and performs slurry and sand pack testing.
- It utilizes a 2" screen holder, flow of 100-5000 ml/min, up to 1000 psig.
- Slurry tests range from 1000 to 5000 ppm concentration.
- Deliverables include flow, pressure data, PSDs, and master curves.
- Brochure Link
Major pipeline erosion occurs at elbows, tees, and reducers. We offer:
- Field-Scale Testing: 30m pipeline length.
- Variety of Pipe Sizes: From 1" to 8".
- High Flow Rates: Up to 2200 SCFM for gas, 150 Nm³/h for water.
- Brochure Link
Our facility offers control valve erosion study at field condition:
- Evaluate and monitor erosion rate and profile of valves in 1”to 4”.
- Perform test at high temperatures, pressure and flow rate with a constant sand feeding rate.
- Brochure Link
- Sand blast testing evaluates steel specimen coatings in a sand impingement cell.
- Assess coating thickness loss via weight and thickness gauge.
- Allows airflow (10-50 m/s), particle size (> 100 μm), sand rate (> 1 Kg/h), and impingement angle (0-90o) variations.
- Determine the burst and collapse pressure rating of sand screen as per API 19SS.
- Conduct test up to (but not limited to) 1000 bar.
- Formulation of Fluid Loss Control pill and Provision for Push – off test.
Lab and field scale assessment to ensure material integrity at each stage of development.
Corrosion Testing
We offer testing range which includes both pilot scale and lab scale corrosion testing. Pilot scale testing allows customers to evaluate corrosion inhibitors and develop models based on the actual flow behavior inside the pipeline. Lab scale testing, on the other hand, helps us test various products in a cost-effective manner. Our expertise spans diverse methodologies to evaluate material vulnerability in varied operational scenarios by conducting precise experiments.
.gif?width=700&height=394&name=Blue%20and%20Gold%20Traditional%20Indian%20Wedding%20Save%20the%20Date%20Video%20(6).gif)
- Our field scale corrosion facility offers both corrosion and erosion studies in a 4-inch pipeline at CO2 partial pressure up to 1 barg.
- It can handle the gas flow up to 1500 scfm and liquid flowrate up to 30 Nm3/hr at 10,000 ppm sand concentration.
- Brochure Link
We offer the corrosion inhibition testing in various environments:
- Rotating Cage Method: The rotating cage method can be used at temperatures up to 70°C and rotation speeds up to 1000 rpm.
- Wheel Test Method: Wheel test setup can be used at temperatures up to 90°C and rotation speeds up to 20 - 90 rpm.
- Autoclave method: The autoclave design pressure and temperature can go up to 350 bar and 650°C respectively and the volume ranges from 500 ml to 25 liters.
- Jet Impingement: The impingement angle generally varies from 10°C to 90°C, impingement velocity can go up to 30 m/s. The nozzle diameter depends on the specimen and the distance between them.
Advancing Technology from TRL3 to TRL 10, CCUS-Carbon Capture Utilization and Storage, Enhanced Oil Recovery (EOR), Sustainable Energy Transition, Carbon Offset Implementation, Green Hydrogen Technology Testing & Validation, Renewable Power Integration Battery Testing.
New Energy Validation
Tridiagonal Solutions leads the validation of new energy technologies, bridging the gap from TRL3 to TRL10 with precision. Specializing in Carbon Capture, Utilization, and Storage (CCUS), Green Hydrogen, and Battery Testing, Electrolyser & Membrane Testing, Material Synthesis & Testing, and Enhanced Oil Recovery & Reservoir Characterization. We scale up technologies seamlessly, ensuring their readiness for real-world application.
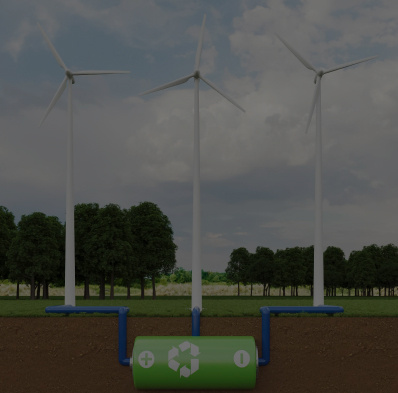
Explore our advanced CCUS facility:
- Study carbon capture (100 TPD CO2) efficiency and storage mechanisms.
- Explore utilization strategies and optimize storage techniques.
- Experience comprehensive CCUS research under one advanced facility.
As experts in hydrogen technology, we offer:
- Assess green hydrogen production's economic viability.
- Evaluate Electrolyser and membrane performance and durability in real-world conditions.
- Safety and performance tests for hydrogen storage and transport.
We offer solutions which include:
- Rock Analysis, Fluid Analysis, & Routine Core Analysis
- Core Flooding experiments, Liquid Permeability, Rock Porosity.
- Micro-PIV Technique, Minimum Miscibility Pressure, Interfacial Tension & Rheology
- Fully automated cutting-edge test process for data measurement and analysis.
- Battery capacity test and pulse power test.
- Measurement of volume-change effects in cells and modules.
- Battery cell, module and pack testing ranges:
- Cell: up to 6V; up to 4000A.
- Module and pack: up to 1200V; up 4000A.
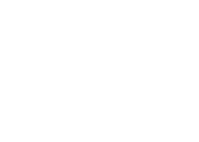
Step into innovation at our lab:
- Fabricate materials precisely with unique properties & enhanced functionality
- Utilize advanced techniques and Analyse properties comprehensively
- Maintain stringent quality control
- Validate performance to industry standards
Who We Are
Flow Assurance
With a focus on proactive testing and innovative solutions, Tridiagonal Solutions is a trusted partner for smooth flow of operation from reservoir to processing facilities, minimizing downtime and maximizing production efficiency for oil and gas. Our state-of-the-art facilities allow us to assess and mitigate issues such as wax deposition, asphaltene precipitation, transportation of sand, liquid metal, CO2 hydrate.
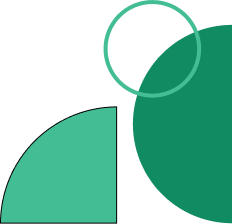
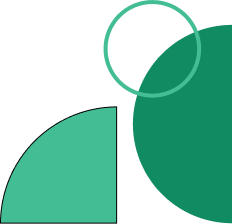
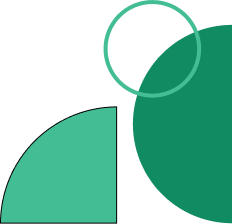
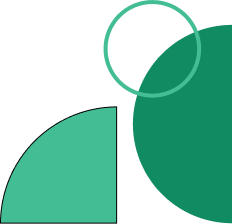
Flow Assurance
With a focus on proactive testing and innovative solutions, Tridiagonal Solutions is a trusted partner for smooth flow of operation from reservoir to processing facilities, minimizing downtime and maximizing production efficiency for oil and gas. Our state-of-the-art facilities allow us to assess and mitigate issues such as wax deposition, asphaltene precipitation, transportation of sand, liquid metal, CO2 hydrate.
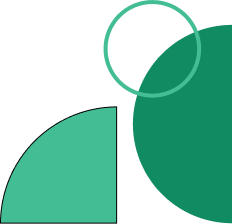
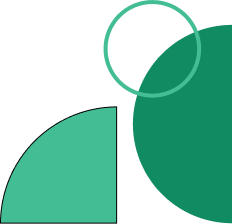
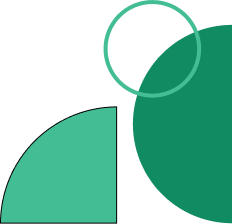
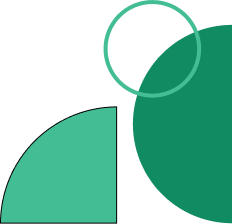
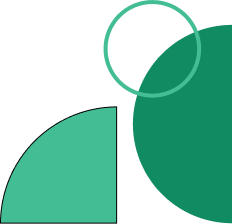
Flow Assurance
With a focus on proactive testing and innovative solutions, Tridiagonal Solutions is a trusted partner for smooth flow of operation from reservoir to processing facilities, minimizing downtime and maximizing production efficiency for oil and gas. Our state-of-the-art facilities allow us to assess and mitigate issues such as wax deposition, asphaltene precipitation, transportation of sand, liquid metal, CO2 hydrate.
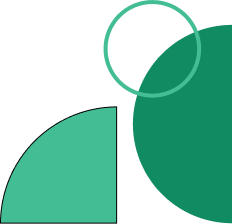
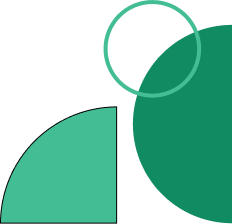
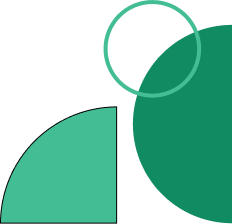
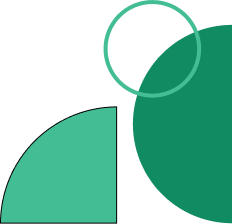
Industries
Your Trusted Partner in Technology Validation & Scale-up Centre
Oil & Gas
Tridiagonal pioneers advanced solutions for oil and gas industries, optimizing processes with cutting-edge flow assurance techniques, erosion-corrosion resilience, and precise multiphase flow analysis, ensuring robust operations and asset longevity.
Life Sciences/Pharma
At Tridiagonal, we revolutionize pharmaceutical manufacturing, mastering intricate mixing dynamics, anti-foaming agent efficacy, granulator efficiency assessment, and seamless scale-up strategies, ensuring precision and excellence in drug formulation.
Food & Beverage (F&B)
Tridiagonal offers expertise in Mixing Solutions, Preservative and Emulsifier Testing, Additive Analysis, Heating and Cooling Efficiency Assessment, and Bottle Testing for enhanced F&B processing.
Chemicals & Petrochemicals
Tridiagonal pioneers' resilience in chemical processes, safeguarding against corrosion, optimizing mixing intricacies, scaling up productions seamlessly, engineering efficient reactors and distillation columns, and maximizing heat exchange efficiency, ensuring chemical excellence and reliability.
Power & Renewables
Tridiagonal pioneers in emerging areas such as Renewable Energy Integration, Carbon Capture Utilization and Storage (CCUS), Green Hydrogen, Sustainable Energy Transition, and driving innovation for a greener future.
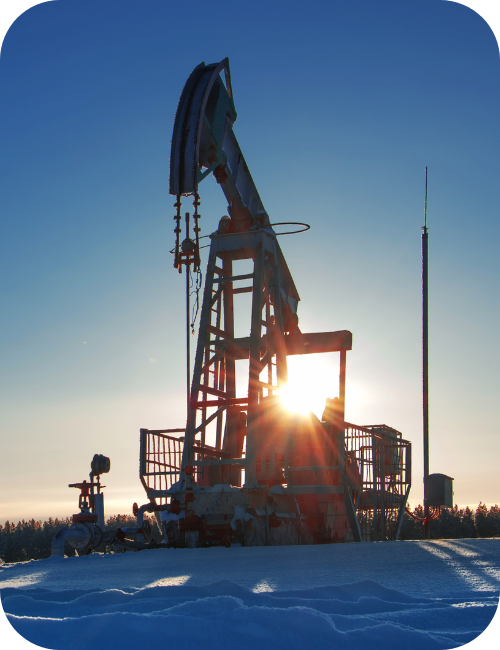
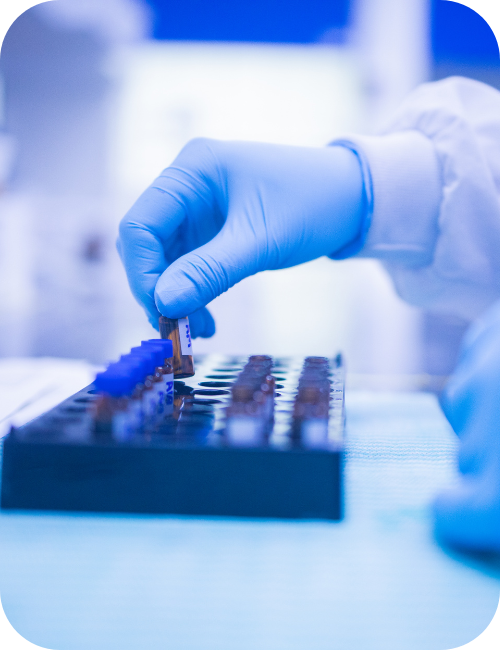
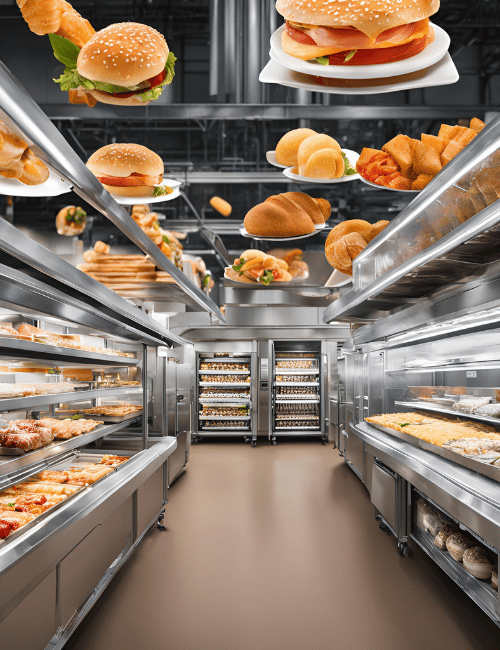
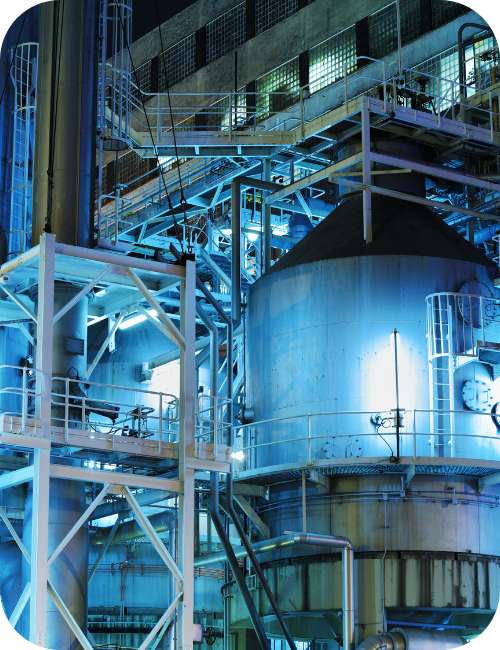
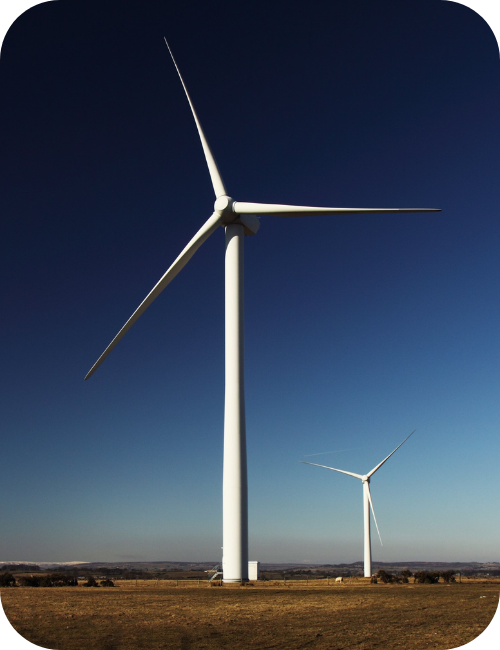
Mixing Studies
Embark on a journey into the heart of our technological expertise, Mixing Facility. In the realm of the Chemical sector, optimizing tank configurations for increased yields is paramount. Challenges arise in determining the optimum configuration of mixing tanks, selecting the appropriate impeller type, impeller position, and impeller clearance to enhance yields through the mixing process without generating unwanted vortex.
Aeration and foaming during bottle filling
Aeration and foaming during the bottle filling process can lead to significant product losses, underfilling, and operational inefficiencies. This case study presents experimental investigations conducted to understand the fundamental mechanics of aeration and foaming under various liquid properties and operating conditions.
Foam Transportation Loop
In the realm of multiphase flow dynamics, understanding the intricate behavior of foams is essential for numerous industrial applications, particularly in the oil and gas sector.
Tridiagonal's Foam Transport Facility stands at the forefront of this research, providing a state-of-the-art platform designed to delve into the complexities of foam generation and breaking mechanisms.
This facility features a substantial 16-inch diameter, -foot-long flow loop, incorporating advanced mesh-type assemblies and comprehensive visualization sections. By generating foams using various surfactants and studying their behavior under diverse flow conditions, the facility offers unparalleled insights into foam dynamics.
Resources
Explore the breadth and depth of our Tridiagonal Solutions technology validation & scale-up solutions in production enhancement.
Why Tridiagonal?
Tridiagonal Solutions, a top facility in Asia, offers cost-effective flow assurance testing for Oil & Gas majors. We are specialized in multiphase flow, erosion-corrosion, wax deposition, and sand management, etc. We collaborate with industry leaders, consultants, EPCs, OEMs and service providers, with flexible business models.

250k+ sq. ft. facility, Advanced equipment's, Lab & field scale testing, 24/7 utility


Leverage cheap labour and pre-built loops tailored to client needs.


Our EPC team creates custom skids quickly. Local network accelerates projects.

Deploying sustainable practices to efficiently create and deliver value for customers.
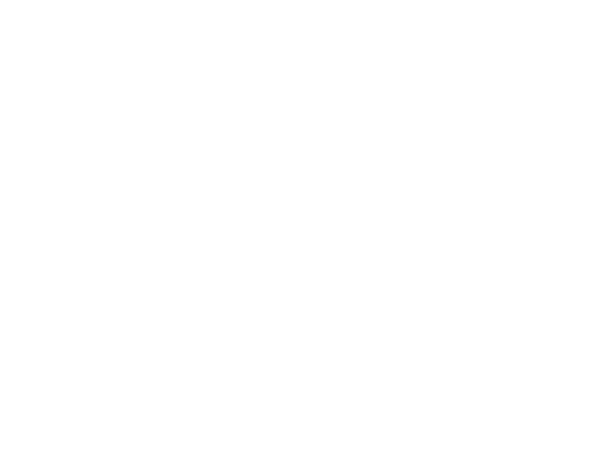
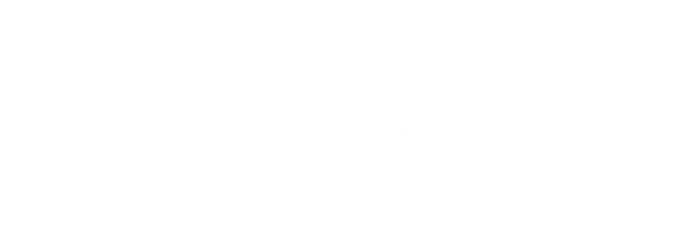
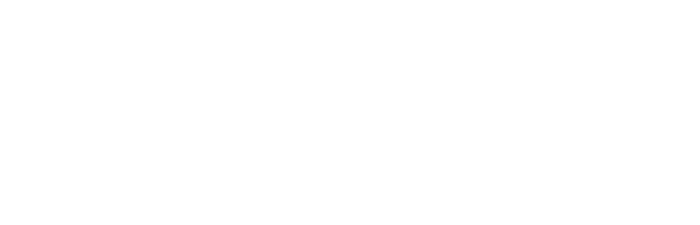
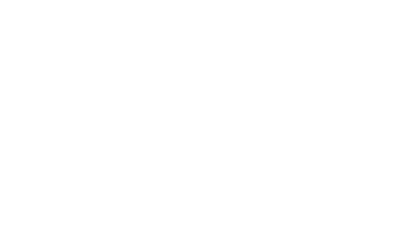
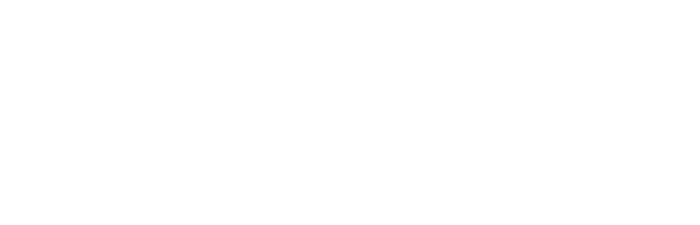
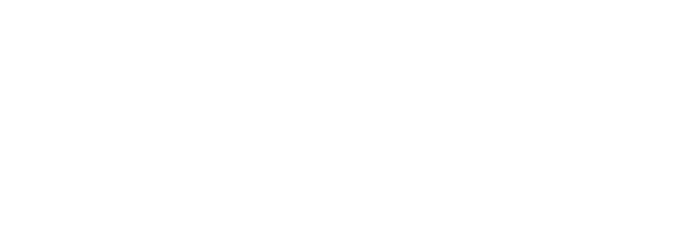
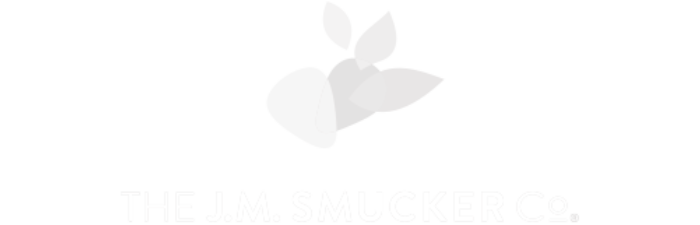
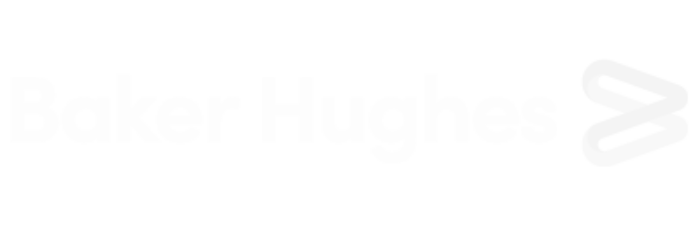
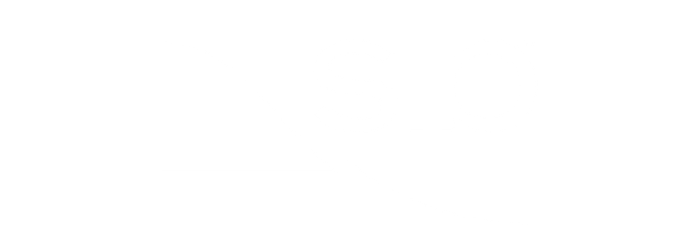
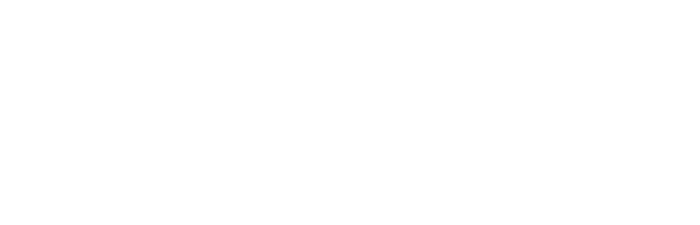
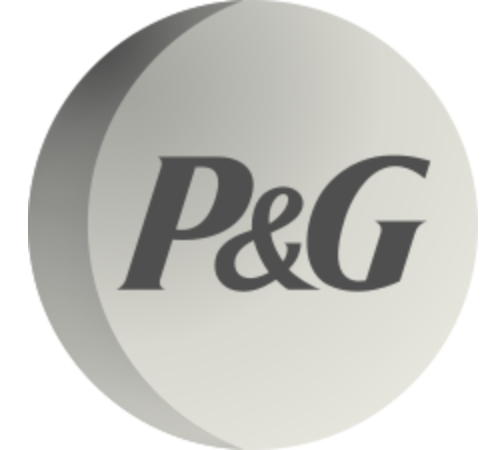
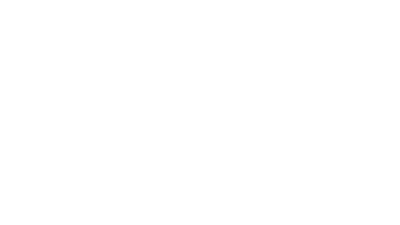
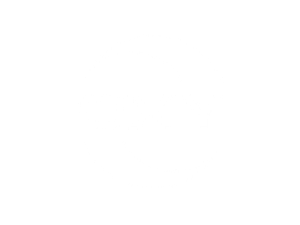
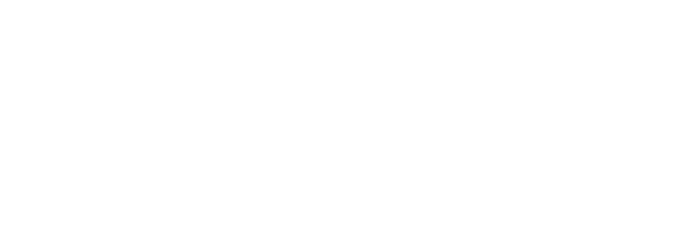
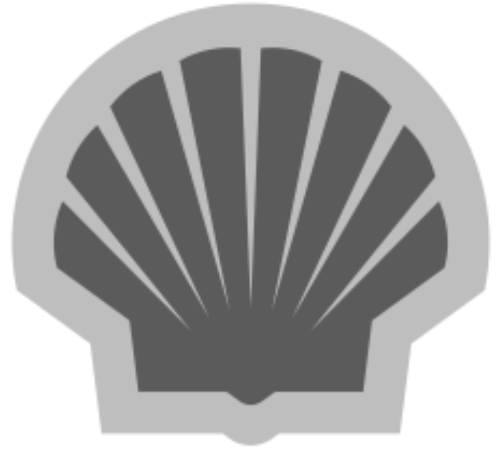
Practice Heads
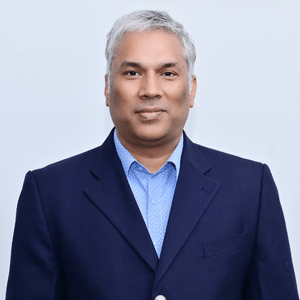
Dr. Damo Vedapuri is the Head of North American Operations at Tridiagonal Solutions. He has 20+ years of experience in solving a wide range of fluid flow problems in the Oil and Gas industry. Some of his core focus areas are Erosion, Erosion – Corrosion, Sand Management, and Slurry Multiphase Flow. Dr. Damo has graduated from the Institute of Corrosion and Multiphase Technology at Ohio University with a Ph.D. degree in Chemical Engineering. He is a member of SPE and actively publishes his group’s research in SPE, OTC, NACE and BHR conferences.
.jpg?width=2000&height=2000&name=RTP_4433%20(2).jpg)
.png?width=501&height=498&name=Image__1_-removebg-preview%20(1).png)
With 44+ years experience, Dr. Lee is working as consultant and earned his Ph.D. in Organic Chemistry from the University of North Carolina. Dr. Lee has worked on flow problems with Chevron in upstream, midstream, refining, LNG, and chemical areas such as Heat Transfer, Sand Transport, Sand Management, Erosion, Multiphase Separation.
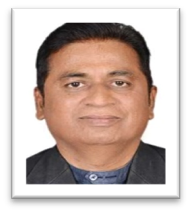
With 33+ years experience, Dr. Ravindra serves as a Consultant overseeing operations, maintenance, and construction of new facilities. Dr. Ravindra holds MS degree in Civil Engineering from Pune University and Ph.D. in the energy sector. His expertise lies in erecting large chemical plants, operational excellence, EPCM, modular engineering.
Schedule a Call today!
Uncover how our capabilities can propel your organization forward. Provide your focus areas, and we will deliver tailored solutions designed to meet your unique objectives.