Dx in Process Manufacturing
Industry Overview
With the growing demand of global oil and gas market, industries face the necessity to optimize their overall costs to sustain and meet market needs. Additionally, market dynamics require continuous improvement through the identification of opportunities to optimize equipment running costs and raw material expenses by maximizing utilization to achieve optimal production levels. Data-driven techniques have proven effective in enabling companies to enhance the performance of their shop floor processes and assets in real-time.
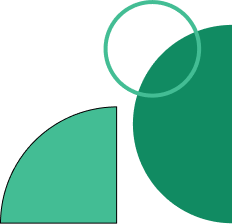
Dx Opportunities
Ensuring quality assurance and optimal production levels is often challenging, subordinated with lot of dependencies associated with the nature of the batch operations itself. “Quality is never in real-time!” – makes it even more difficult for the engineers to make effective decision. Informed decision making is critical to prioritize and ensure maximum productivity at minimum operating cost. This demands for continuous monitoring and tracking of the KPIs of which some are measured, some are siloed and some are derived. Using our value based offerings for life-sciences, organization can reap the benefits in the following areas below:
Reduce the overall carbon footprint through digital intervention by optimizing the fuel, water and steam consumption across entire site operations. Real time optimization of the utilities operations including boilers, steam turbines and cooling towers.
Use Cases: Optimal make up water consumption in cooling tower operations, Prediction of optimal steam to fuel ratio in boiler operations, energy optimization of compressed air networks, optimization of flared gas in VRU operations
Energy Management
Energy prediction and management across site including the utilities is key for improving the overall energy efficiency of the operations. From CDU to crackers and furnaces, it is important to operate at the optimal level to ensure that overall energy, steam, water consumption are minimum as per the predictions. Tridiagonal solutions tailored frameworks enables the organizations to have a deeper and meaningful insights about energy KPIs across the facilities. Thes solutions are curated to deliver the best-in-class solution to bring about the visibility of various energy sources and sinks using the hybrid approach leveraging first principles and data driven techniques.
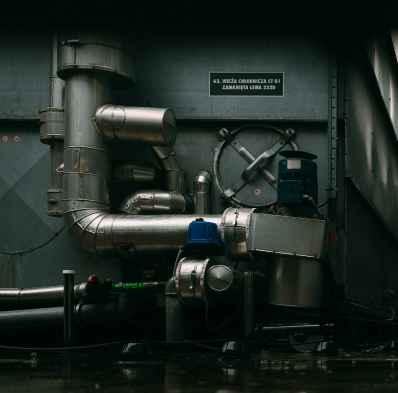

Changing crude composition and equipment performances can lead to variations in the energy consumption through reboiler or condensers. AI model can help the operators with the required set point changes in order to keep the energy consumption at the minimum level without compensating on the fractional cut yields.

Hydrocracker unit has several energy consumers including furnace, compressors and distillation units. Hybrid models based on AI can help in controlling the combustion to optimize the fuel consumption to control the operating conditions to control the reaction dynamics under the continuous influence of changing feed and fuel quality.

Energy consumption of VRU compressors are required to be maintain at optimal level to minimize the gas flaring. AI can predict and help in increasing the availability of the compressors to minimize the energy consumption and gas flared.

KPIs such as steam to fuel ratio is an important metric to allow the frameworks to identify the opportunities for optimization. Correlate the best possible fuel combination strategy with the predicted CV against the target steam production.

For more details on the use cases focusing on energy, steam, water and other resources please click here.
Predicting the failures of critical refinery assets such as compressors, heat exchangers, cooling towers, turbine operations. Predicting the coking and scaling events in furnace operations for end of cycle prediction.
Use Cases: Booster compressors performance prediction, End of cycle prediction of heat exchanger train, Catalyst deactivation rate prediction for Hydrotreater units, prediction of decoke requirements in furnace operations, predictive maintenance of power fluid pumps
Predictive Maintenance
Detect the future unwanted failures due to unplanned downtime and overhauls for the critical rotating assets. Estimate the critical process parameters correlated with the failure modes in real time operations. Unforeseen operating conditions makes it difficult for the operators to understand the dynamics around the health of the equipment. Several factors including deviations in KPIs to seasonality variations lead to unplanned downtimes in the critical assets. With our expertise in dealing with rotating assets, it has been made possible to leverage the physics augmented data driven techniques to track the anomalies and deviations in the assets which can cause the chances of failures. With the predictions organizations can see multiple benefits in planning the maintenance activities to reducing the overall inventory costs.
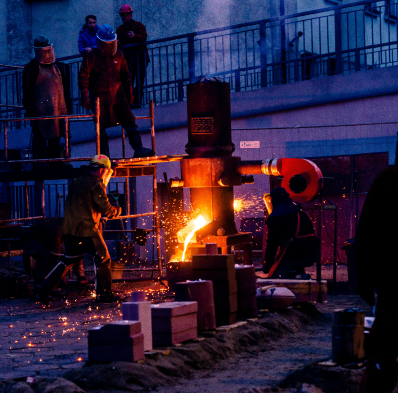

Process and air compressors are one of the most critical operations to ensure the production is met at their desired level of targets at minimum operating cost. Using this solution reliability team can predict the performance (Isentropic and polytropic) and health in real time. These modules helps the team to predict the possibilities of failures with the deeper insights about the failure modes and prescriptions.

Critical failures modes in cooling tower operations are difficult to estimate due to variations in the fan speed, quality of water and seasonality factors. Leveraging the historical data, AI can predict the unforeseen scenarios which may increase the anomaly score of the asset.

Steam turbines are critical components in power generation, where downtime can lead to significant operational disruptions and financial losses. AI based on vibrations and oil analysis information can provide operators with early indicators reflecting any deviations in the signature patterns leading to unwanted failures.

Soiling on solar panels can be the outcome of dirt or particulate matter accumulation on the photovoltaic (PV) module surfaces. This significantly reduce the efficiency and power output of solar energy systems. Predicting soiling rates and patterns is critical for optimizing the cleaning schedule and maintenance of solar panels to ensure they operate at optimal efficiency.
Improve the process efficiency by prediction the lab measurements in real time. Correlate lab parameters such as %sulphur, Oxygen level in flue gas, hydrocarbon composition and conversion in the catalytic reactors.
Use Cases: Inferential for prediction of C4 prediction in debutanizer columns, Top product quality prediction in distillation columns, %O2 in hydrocracker unit, Prediction of oil in water in skimmers
Predictive quality
Quality management for various entities including feedstocks to fuels and product is important to produce with satisfactory level of quality standards. Most of quality variables are recorded based on the lab sampling at certain low frequent intervals, which makes it difficult for the control room operators to take the real time corrective actions. With inferential modeling process operators can gain deeper insights about the set point control changes required for achieving the optimal quality specifications. Physics driven inferentials can enable with real time prediction of quality variables for critical catalytic reactions, distillation and other processes.
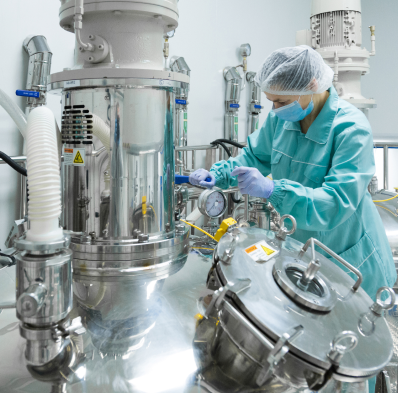
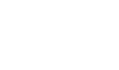
Using physics-based AI to predict the quality parameters such as yield and conversion in real time. Model using the historical low frequency lab reading against the set of operating variables to develop the correlation between the two. Use the recommended changes in the set points to control the quality variations.

Predict the sulphur content in real time to prevent any catalyst degradation and process upsets. Inferential models the % sulphur content at any given point in time to control the process dynamics promoting unwanted deviations.

Maximizing the recovery of oil in water during the skimming operations is crucial. Typically such sampling is time expensive task. AI can enable the prediction of oil in water in real time with changing operating scenarios and fluctuating crude compositions.
Optimizing the refinery operations under dynamic demanding conditions under the influence of changing fuel and feed quality. Improve the control strategies by incorporating the MVs, CVs and DVs with the appropriate constraints and process lags.
Use Cases: Improving the conversion in hydro cracking and hydro treating units, Optimization of propylene conversion in the ethylene plant operations, Optimization of CDU operations for dynamic product cuts, Virtual metering for optimal well operations, gas lift optimization
Process optimization
Optimize the conversion and yield of complex and catalytic processes through AI-based optimization toolbox. Improve the catalyst deactivation rate for efficient reaction kinetics and increased productivity of processes. Improve the productivity of the well operations through integrated well modeling strategy. Leverage the AI based simulators to continuously identify the opportunities to optimize the control strategy to meet the desired product specifications at minimum operating costs.
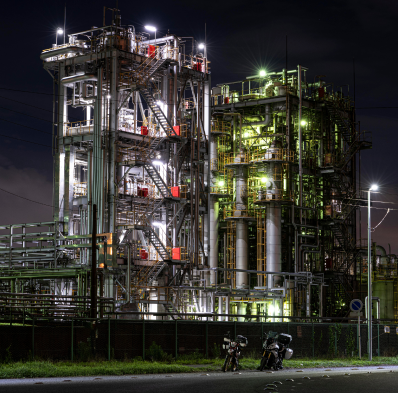

Maintain the oxygen level in the flue gas stream within the heater sections. Improve the combustion efficiency to target operations near to complete combustion scenarios.

Optimize the set point conditions in real time to predict and maintain the optimal levels of recovery and purity with changing feedstock quality. Account for the variations by making the compensatory changes in the operating variables accounting large process lags and complex chemical reaction kinetics.

Catalysts plays an important function to keep the reaction at the desired rate kinetics for maximum conversion. Impurities in feedstock can poison the catalyst eventually deactivating its performance. With AI based optimizers operators can correct the operations in real time to enhance the performance and life of catalyst.

For oil and gas operators it is important to maintain the well production at highest possible level. Changing reservoir conditions and equipment performances impacts the production rates. With hybrid models high fidelity predictions can be made for the multiphase production fluids in real time.
Leverage the zero shot and few shots LLMs to interpret and analyze the unstructured dimensions. Integrate the interpretation from quality reports, product compliance report, incident reports and many others for improving the productivity and gaining deeper insights about the operational dynamics.
Uses Cases: Alarm report analytics, RCA/Incident reports correlation with real time process anomalies, conversational AI for real-time production information.
Generative AI
More than a quarter of data remains unused as it becomes difficult to access and interpret them due to its unstructured and non-standard formats. Documentation spans from raw materials information, production reports to quality and compliance records. Generative AI can be leveraged to automate the interpretation of the information using the zero shot and few shots LLMs to interpret and analyze the unstructured dimensions. Integrate the interpretation from quality reports, product compliance report, incident reports and many others for improving the productivity and gaining deeper insights about the operational dynamics.
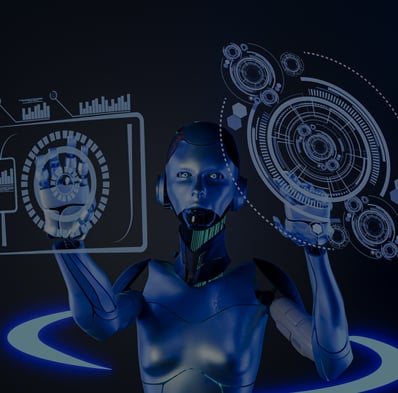

Improve the interpretability with meaningful insights derived from the historical RCA reports. Real time anomalies can be correlated with the historically similar events with the added intelligence about the indicators and corrective actions.

Alarms are critical to be monitored and categorized in several priorities. With the LLMs unstructured alarm reports can be segregated based on its criticality and frequency. These models can augment advanced analysis intelligence to estimate and correlate the information with process parameters

Information from DDRs, DPRs and compliance reports are critical for process improvement opportunities. Generative AI can be utilized to derive the information from the highly organization specific production and compliance reports
An Operator Training Simulator is a high fidelity, computerbased system that enhances operator skills, safety, and efficiency in complex industrial environments by providing a realistic, risk-free training environment. It ensures operators are well-prepared for both routine and emergency situations, contributing significantly to the overall success and safety of the organization.
Use Cases: Realistic Training Environments, Risk Free Simulations, Scenario-Based Learning, Performance Tracking, Knowledge Retention, Regulatory Compliance are the highlights of OTS.
Operator Training Simulator (OTS)
In the intricate and high-stakes world of industrial operations, ensuring the skill and readiness of operators is essential. An Operator Training Simulator (OTS) is a crucial tool in this realm, offering numerous benefits that enhance safety, efficiency, and overall operational success. Key advantages of an OTS is its ability to provide a realistic yet risk-free training environment. Operators can engage with simulations of actual industrial systems, practicing routine tasks and responding to emergency situations. This hands-on experience is vital for developing the skills needed to handle real-world operations confidently. By simulating hazardous scenarios, operators learn to manage potential crises without endangering personnel, equipment, or the environment.
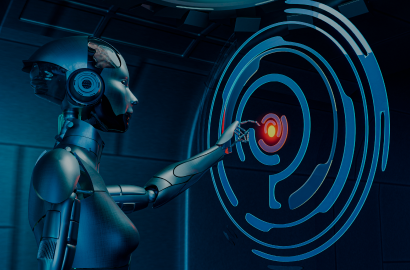

An OTS provides comprehensive scenario-based training, encompassing normal operations, startups, shutdowns, and emergency responses. This diverse array of training scenarios ensures operators are well-prepared for any situation they may face. The opportunity to repeatedly practice these scenarios helps ingrained proper procedures and quick decision-making skills, significantly reducing the likelihood of errors during actual operations.

A key feature of an OTS is its ability to continuously track and evaluate operator performance. By providing detailed feedback and pinpointing areas for improvement, it fosters a culture of continuous learning and development. This ongoing assessment ensures operators maintain high proficiency levels and can effectively adapt to new challenges.

Safety is paramount in industrial operations, and an OTS significantly raises safety standards. Well-trained operators are less prone to errors that could result in accidents, thereby safeguarding both personnel and equipment. Additionally, by minimizing operational mistakes and unplanned downtime, an OTS enhances overall efficiency, leading to more streamlined and productive operations.

Implementing an OTS is financially advantageous, as it reduces errors and downtime, leading to substantial cost savings. Additionally, an OTS ensures that operators receive consistent and comprehensive training, aiding organizations in meeting industry regulations and standards. This thorough training can be documented and audited, facilitating compliance.

Training operators on the following:
- Distillation units control and troubleshooting
- Simulate catalytic and thermal cracking operations for training on process optimization and safety
- Desulfurization and hydrogenation processes to improve product quality and safety
- Operation, control, and maintenance of gas compressors
Use Cases
Despite of the dynamic market needs and end product pricing, it is important to identify the opportunities for continuous improvement in the existing operations through effective utilization of the critical rotary assets, effective combustion of enhancing the catalyst life and optimizing the reaction kinetics and others:
Accelerate your Dx projects with Smart Apps and Time-to-value (TTV) program
Integrate ready-to-deploy smart apps with your existing IT-OT infrastructure and scale across plants.
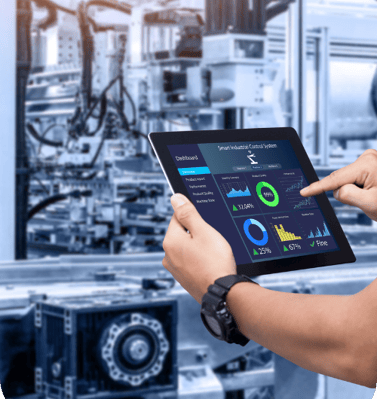
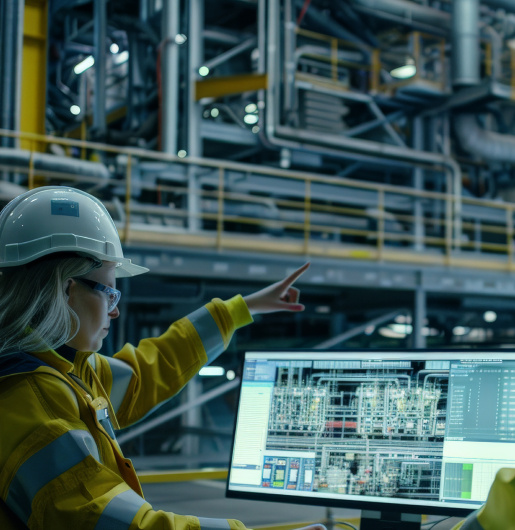
- Smart Apps
- TTV A-33 Program
Tridiagonal Solutions launches ‘Process optimization framework’ for manufacturing industry. We optimize processes for energy, efficiency, quality using cutting-edge technology and engineering expertise. From custom column design to process intensification, we're driving innovation for a sustainable future.
Leveraging these frameworks allows the industry to implement the ML models at scale.
Time to Value program leverages advanced scalability frameworks to deliver superior analytics solutions to manufacturing industries. Designed for rapid implementation, our program ensures larger delivery with unparalleled speed and efficiency. By utilizing scalability frameworks, we significantly reduce the time and cost associated for standard approaches. and accelerates deployment, allowing manufacturers to quickly gain insights and drive improvements in their operations. With our program, clients benefit from faster, data-driven decision-making, enhanced productivity, and a swift return on investment, making it the optimal choice for modern manufacturing analytics projects.
Why Tridiagonal?






Team having exposure and expertise of developing scalable solutions across multiple platforms.
Looking for Trusted Partner for executing your programs?
We bring together unparalleled expertise with combination of skillsets and technology to address your digital needs.