Dx in Process Manufacturing
Industry Overview
With ever growing demand of the consumer products, it is of utmost importance to minimize their unit manufacturing costs in real-time operations. This requires efficient operations with reduced waste, less energy consumption and increased productivity. Data-driven techniques for real-time manufacturing process optimization and monitoring are beneficial to achieve . Business can use data analytics to predict equipment problems, find inefficiencies and match production schedules to demand.
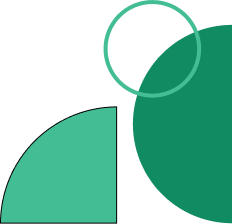
Dx Opportunities
We possess a deep understanding of the distinctive hurdles encountered within the chemicals and petrochemicals sector. From navigating intricate regulatory frameworks to managing the intricate interplay of supply chain dynamics, our holistic strategy directly confronts these industry-specific challenges. Employing advanced data analytics, machine learning, and predictive modeling, we provide actionable insights that yield tangible outcomes, propelling our clients toward enduring prosperity in an ever-evolving landscape.
Reduce the overall energy consumption of utilities including boilers, turbines and air compressors. Optimize the steam consumption across process facilities by minimizing the product off-specifications
Fuel and steam consumption optimization, minimizing the carbon footprint for the process facilities, reduction of process waste
Energy Management
Energy prediction and management across site including the utilities is key for improving the overall energy efficiency of the operations. For a chemical or a petrochemical facility, it is important to operate at the optimal level to ensure that overall energy, steam, water consumption are minimum as per the predictions. Tridiagonal solutions tailored frameworks enables the organizations to have a deeper and meaningful insights about energy KPIs across the facilities. Thes solutions are curated to deliver the best-in-class solution to bring about the visibility of various energy sources and sinks using the hybrid approach leveraging first principles and data driven techniques.
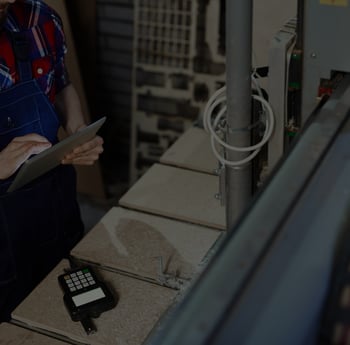
KPIs such as steam to fuel ratio is an important metric to allow the frameworks to identify the opportunities for optimization. Correlate the best possible fuel combination strategy with the predicted CV against the target steam production.

Cooling tower are the important source of water supply across process facilities. Our frameworks are devised in a way to predict the required amount of make water considering the demand of cooling water and its corresponding energy consumption.

Monitor the emission across the operations against the benchmark emission and specific energy consumption. Correlate the emissions against the set of operating variables to improve the control strategy to keep the emissions at the best possible level
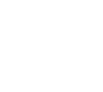
Track and monitor the steam efficiency at equipment and site level operations. Predict the required amount of steam using first principles and benchmark it against the actual steam consumption. Track the overall steam economy across various unit operations and process across site, starting with Boilers to turbines and reactors in processing facilities.

For more details on the use cases focusing on energy, steam, water and other resources please click here.
Predict the failure modes of critical rotating and static assets through early event detection. Prescribe the corrective actions by incorporating the failure mode libraries based on the historical events.
Compressors performance prediction, heat exchangers end of cycle prediction, dryers, evaporators
Improved uptime
Maintaining the availability for the desired period of uptime has always been a challenging task for the chemical and petrochemical operations. Critical assets spans from large compressors to mid-sized exchangers and static assets. Unforeseen operating conditions makes it difficult for the operators to understand the dynamics around the health of the equipment. Several factors including deviations in KPIs to seasonality variations lead to unplanned downtimes in the critical assets. With our expertise in dealing with rotating assets, it has been made possible to leverage the physics augmented data driven techniques to track the anomalies and deviations in the assets which can cause the chances of failures. With the predictions organizations can see multiple benefits in planning the maintenance activities to reducing the overall inventory costs.
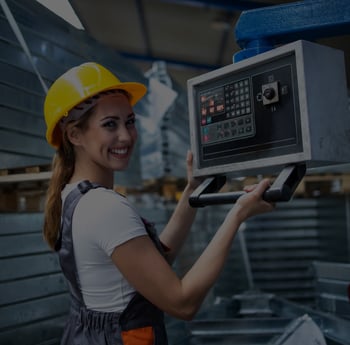

Process and air compressors are one of the most critical operations to ensure the production is met at their desired level of targets at minimum operating cost. Using this solution reliability team can predict the performance (Isentropic and polytropic) and health in real time. These modules helps the team to predict the possibilities of failures with the deeper insights about the failure modes and prescriptions.

Critical failures due to fouling of the tubes can lead to large unplanned downtimes accounting for production losses. Using first principles and thermodynamics estimation of the fouling level against the best operating regime and the minimum level of operations can be established. This approach when scaled across the train of heat exchangers can help the maintenance team to plan and prioritize the maintenance activities for the critical equipment.

Coke deposition in the internals of the furnaces are inevitable events. With predictive maintenance algorithms opportunities for better planning and control of the furnaces can be achieved. Prediction of the decoke events can help in enhancing the life of furnace tubes and improving the efficiency of cracking reactions in real time.

Chillers are important source of providing chilled water across process and building facilities. Maintaining the desired availability of chillers with optimal efficiency is of utmost importance. Using the thermodynamics and data driven techniques KPIs such as COP, end of cycle can be predicted for its critical equipment including evaporators, condensers and expansion valves.
Predict the critical quality variables such as yield, viscosity, sulphur content and product composition in real-time which are infrequently samples at low frequency.
Soft sensors for yield prediction, mass composition prediction in real time
AI based inferentials
Quality management for various entities including fuel is important to produce energy at the desired level. Most of quality variables are recorded based on the lab sampling at certain low frequent intervals, which makes it difficult for the control room operators to take the real time corrective actions. With inferential modeling process operators can gain deeper insights about the set point control changes required for achieving the optimal quality specifications.
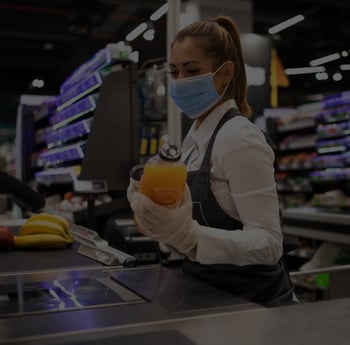

With several sources of coal, it is important to maintain the quality of the blend at a desired level to provide the optimal combustion source in the boiler operations. AI based smart inferentials can help the operators identify the best possible combination of coal and output blend quality.
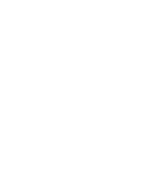
DGA involve analysis of several hydrocarbon gases. The analysis is not possible in real time. AI can be leveraged to develop the sofsensor for each of the gas analysis to predict the values in real time.

Maintaining the water quality is important to prevent any scales or deposition in the downstream processing facilities. Using inferential modeling quality parameters such as PH, Chloride content, Oxygen demand can be predicted in real time aiding the operators to manage and maintain the water quality at the desired levels.

Multi-effect evaporators are important to concentrate the solvent to desired levels at optimal consumption of steam. Overall economy of steam depends on the steam consumed to production achieved with specified product concentration. AI predicts the concentration in real time at various operating conditions helping to minimize the iterations to resort at the right combination of input parameters.
Optimize the cycle time and yield of batch and continuous processes through deep learning based optimization toolbox. Improve the catalyst deactivation rate for efficient reaction kinetics and increased productivity of processes.
Raw material consumption optimization, golden batch analytics, OEE, decision support system for efficient control of distillation columns, improved reaction for furnace operations
Process optimization
Under flexible operations mode, it is highly crucial to maintain the operations at optimal level incorporating the dynamic changes to optimize the cost of production. Maintain the operations optimally for high scale of assets as observed in power generation vertical can be a challenging task. AI can be powered to drive the innovation and improvements in the existing efforts of process optimization.


With the changing demand and fuel quality it is important to maintain the KPIs such as steam to fuel ratio and power to steam ratio for optimal operations. Using AI several influencing factors such as fuel CV, water inlet and steam generated can be correlated with the electricity generated.

Reheater spray is an important source of water utilized for steam generation. Optimization of the RH spray to improve the performance of boilers can be expensive without efficient control strategy. With AI several controlling factors and upstream variables can be accounted to get the desired amount of spray when required.

Blowdown losses impacts the overall performance of the cooling tower operations. With high blowdown there is a direct impact on the water quality and energy consumption. AI can be leveraged to optimize the blowdown losses by optimal addition of the feed make up water for given water quality in real time.

Techniques such as dissolved gas analysis (DGA) and duval’s triangle have been crucial to optimize the transformers performance. AI can be used to predict the performance and health of the transformers with the given operational parameters and gas analysis results
Leverage the zero shot and few shots LLMs to interpret and analyze the unstructured dimensions. Integrate the interpretation from quality reports, product compliance report, incident reports and many others for improving the productivity and gaining deeper insights about the operational dynamics.
Alarm report analytics, RCA/Incident reports correlation with real time process anomalies, conversational AI for real-time production information.
Generative AI
More than a quarter of data remains unused as it becomes difficult to access and interpret them due to its unstructured and non-standard formats. Documentation spans from raw materials information, production reports to quality and compliance records. Generative AI can be leveraged to automate the interpretation of the information using the zero shot and few shots LLMs to interpret and analyze the unstructured dimensions. Integrate the interpretation from quality reports, product compliance report, incident reports and many others for improving the productivity and gaining deeper insights about the operational dynamics.
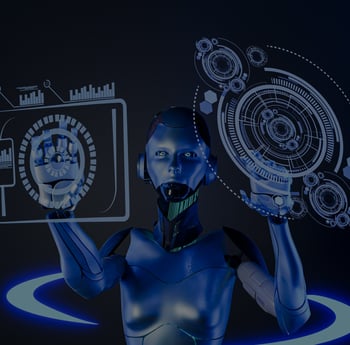

Improve the interpretability with meaningful insights derived from the historical RCA reports. Real time anomalies can be correlated with the historically similar events with the added intelligence about the indicators and corrective actions.

Alarms are critical to be monitored and categorized in several priorities. With the LLMs unstructured alarm reports can be segregated based on its criticality and frequency. These models can augment advanced analysis intelligence to estimate and correlate the information with process parameters

Information from DDRs, DPRs and compliance reports are critical for process improvement opportunities. Generative AI can be utilized to derive the information from the highly organization specific production and compliance reports
An Operator Training Simulator (OTS) is a high fidelity, computer based system that enhances operator skills, safety, and efficiency in complex industrial environments by providing a realistic, risk-free training environment. It ensures operators are well-prepared for both routine and emergency situations, contributing significantly to the overall success and safety of the organization.
Realistic Training Environments, Risk Free Simulations, Scenario-Based Learning, Performance Tracking, Knowledge Retention, Regulatory Compliance are the highlights of OTS.
Operator Training Simulator (OTS)
In the intricate and high-stakes world of industrial operations, ensuring the skill and readiness of operators is essential. An Operator Training Simulator (OTS) is a crucial tool in this realm, offering numerous benefits that enhance safety, efficiency, and overall operational success. Key advantages of an OTS is its ability to provide a realistic yet risk-free training environment. Operators can engage with simulations of actual industrial systems, practicing routine tasks and responding to emergency situations. This hands-on experience is vital for developing the skills needed to handle real-world operations confidently. By simulating hazardous scenarios, operators learn to manage potential crises without endangering personnel, equipment, or the environment.
.webp?width=350&height=230&name=Operator%20Training%20Simulator%20(OTS).webp)

An OTS provides comprehensive scenario-based training, encompassing normal operations, startups, shutdowns, and emergency responses. This diverse array of training scenarios ensures operators are well-prepared for any situation they may face. The opportunity to repeatedly practice these scenarios helps ingrained proper procedures and quick decision-making skills, significantly reducing the likelihood of errors during actual operations.

A key feature of an OTS is its ability to continuously track and evaluate operator performance. By providing detailed feedback and pinpointing areas for improvement, it fosters a culture of continuous learning and development. This ongoing assessment ensures operators maintain high proficiency levels and can effectively adapt to new challenges.

Safety is paramount in industrial operations, and an OTS significantly raises safety standards. Well-trained operators are less prone to errors that could result in accidents, thereby safeguarding both personnel and equipment. Additionally, by minimizing operational mistakes and unplanned downtime, an OTS enhances overall efficiency, leading to more streamlined and productive operations.

Implementing an OTS is financially advantageous, as it reduces errors and downtime, leading to substantial cost savings. Additionally, an OTS ensures that operators receive consistent and comprehensive training, aiding organizations in meeting industry regulations and standards. This thorough training can be documented and audited, facilitating compliance.
Use Cases
In the arena of Chemicals and Petro chemicals’ continuously expanding market landscape and dynamic shifts, digital technologies remain indispensable in boosting the solutions for a myriad of industrial challenges spanning the entire quality series within the chemical and petrochemical sectors. Here, we present a curated list of use cases specifically tailored to shop floor interests, aimed at addressing a diverse array of challenges encountered within these industries:
Accelerate your Dx projects with Smart Apps and Time-to-value (TTV) program
Integrate ready-to-deploy smart apps with your existing IT-OT infrastructure and scale across plants.
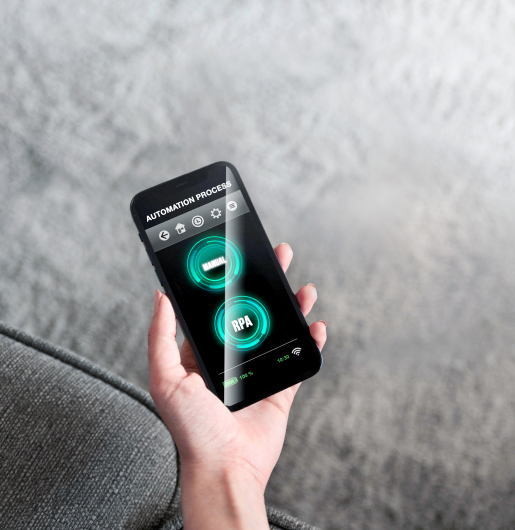
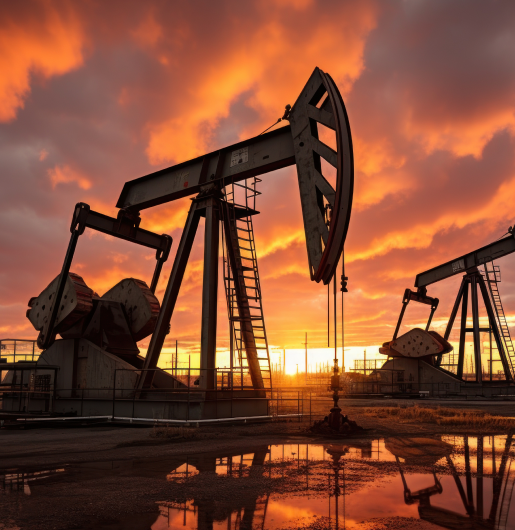
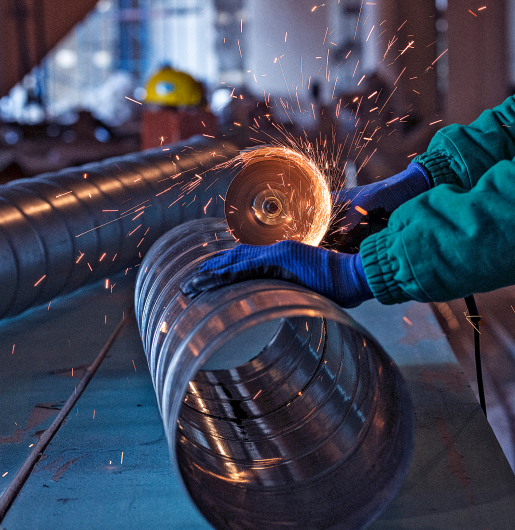
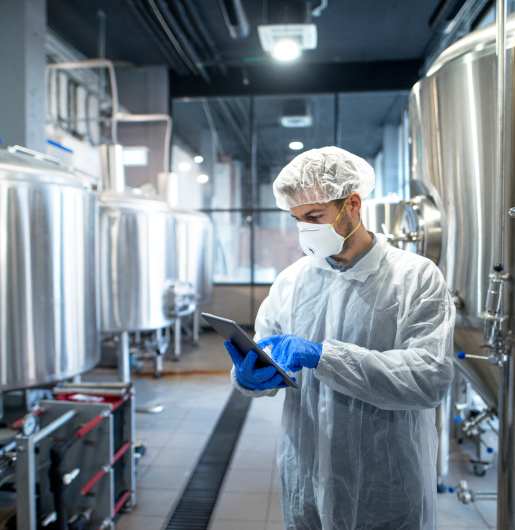
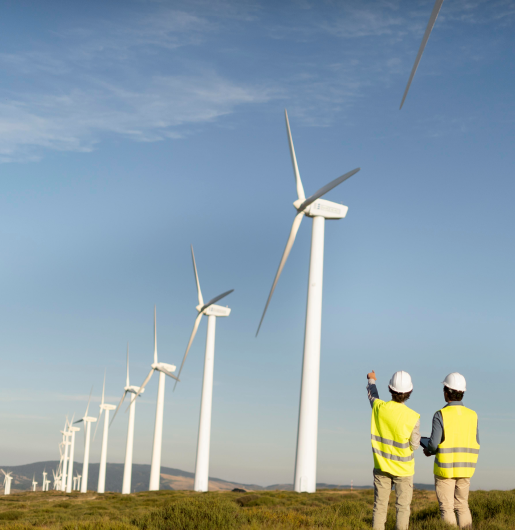
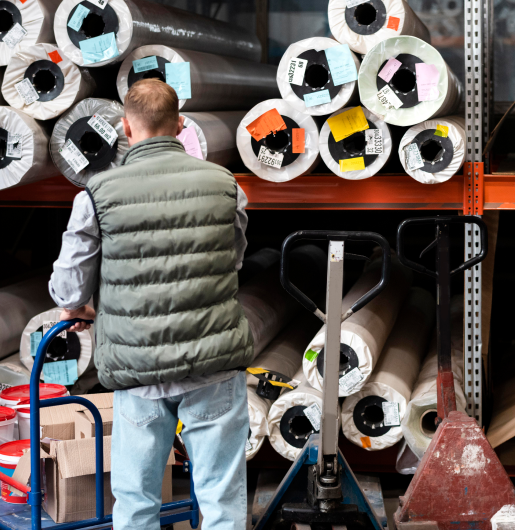
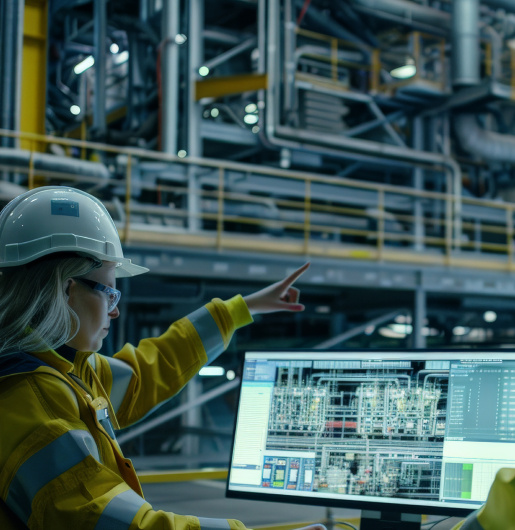
- Smart Apps
- TTV A-33 Program
Tridiagonal Solutions launches ‘Process optimization framework’ for manufacturing industry. We optimize processes for energy, efficiency, quality using cutting-edge technology and engineering expertise. From custom column design to process intensification, we're driving innovation for a sustainable future.
Leveraging these frameworks allows the industry to implement the ML models at scale.
Time to Value program leverages advanced scalability frameworks to deliver superior analytics solutions to manufacturing industries. Designed for rapid implementation, our program ensures larger delivery with unparalleled speed and efficiency. By utilizing scalability frameworks, we significantly reduce the time and cost associated for standard approaches. and accelerates deployment, allowing manufacturers to quickly gain insights and drive improvements in their operations. With our program, clients benefit from faster, data-driven decision-making, enhanced productivity, and a swift return on investment, making it the optimal choice for modern manufacturing analytics projects.
Why Tridiagonal?






Team having exposure and expertise of developing scalable solutions across multiple platforms.
Looking for Trusted Partner for executing your programs?
We bring together unparalleled expertise with combination of skillsets and technology to address your digital, computational and testing needs