Simulation (CFD/FEA)
About Practice
Tridiagonal Solutions is one of the leading modeling & Simulation consulting companies having strong global client base. We provide modeling services in Computational Fluid Dynamics(CFD), Finite Element Analysis(FEA), Discrete Element Method(DEM) & Multiphysics as well. Our engineers also help to develop digital twins of equipment or process. Our modeling expertise enables industry to improve & optimize processes and equipment design. Modeling & Simulation also provides deep insights to understand root cause of structural failure & troubleshoot the performance issues.
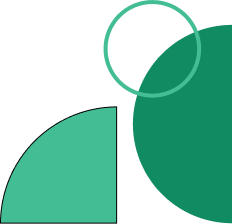
Capabilities
Tridiagonal has considerable capabilities in CFD modeling of combustion, multiphase flows and reactions. We are expertise in solving Multiphysics problems such as tightly coupled fluid structural (FSI) interaction, Flow Induced Vibration and acoustic induced vibration problems. We have expertise to assess structural integrity of equipment for thermal and physical loads as well as predicting fatigue life. Tridiagonal has expertise in developing digital twin, ROM & Response Surface Models.
Multiphase flow, Phase change, combustion and reaction modeling are our routine areas of working. We help industry to analyze root cause of the failure. Our engineers provide deep insights for troubleshooting & process improvement
Computational Fluid Dynamics (CFD)
Computational Fluid Dynamics (CFD) empowers you to visualize and analyze complex fluid flow phenomena within your designs. Our team of CFD specialists leverages cutting-edge software and proven methodologies to provide comprehensive solutions for a wide range of applications, including Aerodynamics and heat transfer analysis for product design, Multiphase flow modeling to analyze mixing & separation process and Combustion analysis for emission control. We are trusted partners of renowned companies due to our exceptional way of working since last two decades. As Tridiagonal has started the journey with CFD, hence it made us a front player in resolving flow related issues. After few years, we have extended our work area to include DEM & FEA. That makes us a one stop destination for modern industries to quench the simulation needs. To see the transformative impact of our CFD studies in various industries, please refer our case studies. For more information, please contact us.
.jpg?width=398&height=393&name=Computational%20Fluid%20Dynamics%20(CFD).jpg)

Tridiagonal engineers simulate and visualize fluid motion, pressure distribution, and forces acting on objects immersed in fluids. This helps to optimize designs for the better performance. Our engineers can simulate and analyse fluid flow around packaged goods to ensure optimal protection during transportation and storage, preventing damage and spoilage. While in Oil extraction, we simulate fluid flow during drilling to optimize wellbore placement, predict formation pressures, and ensure wellbore stability. Also we simulate the wash and cement processes to maximize the cement plug quality in Plugging and abandonment. In Process industries CFD can simulate the mixing of fluids in tanks and reactors. It can aid in scaling up processes from lab-scale to industrial-scale by simulating fluid behavior under different operating conditions and geometries. CFD models can simulate chemical reactions occurring within reactors, furnaces, and combustion chambers..

We simulate systems involving multiple fluids, solids, or gases interacting with each other. This optimizes Cyclone design, predicts behavior of slurries in pipes, and improves efficiency in separators, Knockout Drums and vapor horn.

Tridiagonal has considerable experience on modeling burner arrangements, flame interactions, NOx and SOx predictions and Flame impingement on radiant tube section to avoid rupture. Our engineers also worked on processed heaters used in reformers. We help optimize flow of fluid and air to Burner using CFD as well as improve combustion efficiency by optimizing fuel and air flow

CFD simulations are valuable across various industries, aiding in the design and optimization of products and processes. In the medical device industry, CFD enhances the development of inhalers, drug delivery systems, and surgical tools by simulating fluid flow, heat transfer, and particle dynamics to ensure efficiency, safety, and effectiveness. In the chemical and process industry, it allows engineers to iterate through multiple designs and operating parameters virtually, reducing the need for costly prototypes and accelerating the development of optimized equipment. Similarly, in the CPG industry, CFD aids in the development of food products and processes, such as optimizing fluid flow and heat transfer in food extrusion and improving packaging designs to enhance product freshness and appeal. This technology streamlines development, reduces costs, and leads to better-performing products across these sectors.CFD simulations are valuable across various industries, aiding in the design and optimization of products and processes. In the medical device industry, CFD enhances the development of inhalers, drug delivery systems, and surgical tools by simulating fluid flow, heat transfer, and particle dynamics to ensure efficiency, safety, and effectiveness. In the chemical and process industry, it allows engineers to iterate through multiple designs and operating parameters virtually, reducing the need for costly prototypes and accelerating the development of optimized equipment. Similarly, in the CPG industry, CFD aids in the development of food products and processes, such as optimizing fluid flow and heat transfer in food extrusion and improving packaging designs to enhance product freshness and appeal. This technology streamlines development, reduces costs, and leads to better-performing products across these sectors.
DEM is utilized in pharmaceuticals for powder mixing and tablet compression, in chemicals for particle handling and crystallization, and in CPG for packaging and mixing processes. It optimizes operations, ensuring uniformity and efficiency in dosage, product quality, and handling.
Discrete Element Method (DEM)
DEM offers significant advantages across various industries, including pharmaceuticals and medical devices, chemical and process engineering, and food and beverage/consumer packaged goods. In pharmaceuticals and medical devices, DEM simulates granular material behavior, optimizing processes like tablet compression, coating, and granulation, and assisting in the design of drug delivery systems. In chemical and process engineering, DEM models granular flow, particle interactions, and various processes such as mixing, crystallization, and spray drying, improving efficiency and safety. In the food and beverage/CPG industries, DEM aids in powder handling, packaging design, mixing, and supply chain management, enhancing product development, quality control, and competitiveness. Overall, DEM serves as a valuable tool for optimization and innovation, improving processes from formulation to manufacturing and packaging across diverse industries.
.jpg?width=398&height=393&name=Discrete%20Element%20Method%20(DEM).jpg)

DEM is a simulation technique crucial for optimizing tablet compression and coating processes in pharmaceutical manufacturing. In compression, it predicts granular flow patterns, compaction behavior, and aids in tooling design by modeling particle-tool interactions. It also optimizes press settings, enhancing tablet quality and reducing tool wear. In coating, DEM forecasts coating uniformity, thickness distribution, and prevents issues like agglomeration by simulating tablet movement in the coating pan or drum. It optimizes coating parameters like drum speed and spray rate, ensuring material efficiency and desired coating quality. Overall, DEM enhances product quality, process efficiency, and cost-effectiveness in pharmaceutical manufacturing./p>
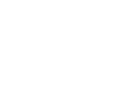
DEM is a computational technique employed to simulate the behavior of granular materials, including powders, in various handling and processing scenarios. By representing individual particles as discrete entities and modeling their interactions, DEM enables engineers to gain insights into complex phenomena such as powder flow, mixing, segregation, and packing. DEM simulations facilitate the understanding of how factors like particle size, shape, cohesion, and friction influence powder behavior within different equipment geometries and operational conditions. This computational approach aids in the optimization of equipment design, the prediction of mixing performance, the analysis of segregation phenomena, and the mitigation of flow issues, ultimately enhancing the efficiency and reliability of powder handling processes across industries.

DEM is a computational technique used to model and simulate the behavior of particulate systems, particularly valuable in studying mixing and segregation processes. DEM allows for detailed analysis of particle interactions, optimizing equipment and processes by adjusting parameters like rotation speed and fill level. It evaluates mixing efficiency and identifies poor mixing regions, aiding in systematic studies of variable impacts on mixing. For segregation, DEM identifies mechanisms like percolation and convection, quantifies segregation patterns, and guides process design to minimize segregation. Its applications span industries such as pharmaceuticals, food processing, construction materials, and mining, where it helps ensure uniformity, prevent segregation, and enhance product quality.

DEM is a powerful computational tool used extensively in the chemical, pharmaceutical, and CPG industries to simulate and optimize particulate systems. In chemical industry, DEM aids in powder processing, reactor design, and flowability studies, enhancing product consistency and process efficiency. In pharmaceuticals, it helps in tablet manufacturing, drug delivery system design, and capsule filling, ensuring precise dosing and uniformity. The CPG industry benefits from DEM in packaging, product quality control, and equipment design, improving handling, stability, and texture of goods. Overall, DEM accelerates product development, reduces costs, promotes sustainability, and allows for greater customization, driving innovation and efficiency across these sectors.
(FEA)
Our canvas covers the assessment of the structural integrity of equipment, vessels, and components under static and dynamic loads, preventing thermal failures with optimized heat transfer & temperature distribution. While analyzing the cause of failure our engineers follow industry standards like ASME & API
Finite Element Analysis (FEA)
FEA is used to analyze the behavior of complex structures and systems under various loading conditions. We have a proven track record of success in applying these analyses to a wide range of engineering challenges across the Oil & Gas, Cement Manufacturing, Chemical and CPG industries. Engineering experts with strong domain knowledge are specialized to solve intricate engineering challenges faced by modern industry. Our canvas covers the assessment of the structural integrity of equipment, vessels, and components under static and dynamic loads, preventing thermal failures with optimized heat transfer & temperature distribution. We are capable in seamless coupling of FEA with CFD or DEM when the complexity of the problem is at higher side. Visit our case study section to explore our potential. Our engineers are enthusiastic to connect with you & understand your problem./p>
.jpg?width=398&height=393&name=Finite%20Element%20Analysis(FEA).jpg)

The Oil & Gas, Power, and Cement industries rely heavily on structures and components that endure cyclic loading over extended periods. This constant stress and relaxation can lead to fatigue failure, causing significant safety hazards and operational downtime. FEA (Finite Element Analysis) plays a crucial role in analyzing and mitigating fatigue risks for equipment like pipelines supports, pressure vessels, and drilling equipment in Oil and Gas. While in power industry our engineers are working on Boilers. In cement industry we identify fatigue prone areas of Silos and Kiln. FEA is crucial in the Chemical and Process industries as well as in CPG manufacturing. It predicts fatigue life and fracture behavior under cyclic loading and thermal cycling, models chemical reactions within reactors by optimizing reaction conditions and reactor design for efficient scaling up of processes, and aids in designing durable equipment like mixers and conveyors. By identifying potential failure points and optimizing designs, FEA improves safety, efficiency, and cost-effectiveness.

Tridiagonal FEA team can predict thermal stresses caused by temperature variations. This is important in oil and gas well casings for withstanding downhole temperature changes. In power generation, it helps analyze stress in turbine blades due to high operating temperatures. Cement kilns also benefit from our FEA's ability to predict thermal stress in refractory linings, preventing cracking and ensuring structural integrity.
FEA helps assess the structural integrity of components under static loads like pressure and weight. Our engineers are using this ability to ensure structural integrity of pressure vessels in Energy sector. Our engineers have deep knowledge of industry standards like ASME and API
For process industries involving heat exchange, FEA can model thermal behavior, including conduction, convection, and radiation. It helps in optimizing heat exchangers, reactors, furnaces, and other thermal equipment for efficient heat transfer and temperature control.
In CPG, FEA can be utilized to analyze heat transfer phenomena in food processing equipment such as ovens, refrigerators, and pasteurizers.

Oil and gas pipelines, power plant structures, and cement silos can experience seismic activity or impact loads. Our FEA engineers simulate these dynamic events, predicting stress and deformation of components to assess vulnerability and design for earthquake resistance. Rotating machinery in power plants and cement factories can generate vibrations. FEA helps identify natural frequencies and potential resonance points by analyzing dynamic response.

FEA can aid in modeling chemical reactions within reactors and other vessels, considering factors such as kinetics, heat generation or absorption, and mass transfer. This helps in optimizing reaction conditions, reactor design, and scaling up processes. FEA can be used to assess the structural integrity of equipment and components such as pressure vessels, pipelines, reactors, and storage tanks. It helps in predicting stresses, strains, and deformations under different operating conditions and loads, ensuring compliance with safety standards and regulations.
Tridiagonal engineers are capable in solving fluid-structure interaction (FSI) problems, while coupling of DEM-FEA models the behavior of granular materials interacting with structures, provides a deeper understanding of stress distribution, particle flow, and potential equipment wear.
Multiphysics Simulation
In traditional engineering, each physical phenomenon is often analyzed independently. However, real-world problems rarely occur in isolation. Multiphysics simulation bridges this gap by enabling the simultaneous simulation of multiple interacting physics within a single model. This allows technology leaders to capture the true essence of complex engineering challenges and achieve more accurate and reliable results.
Our CFD, FEA & DEM engineers form strong synergy to develop this cutting-edge approach of Modeling & Simulation. Highlighting the potential with two technologies of CFD-FEA and DEM-FEA coupling. Combining CFD & FEA complex interplay between fluids and structures can be simulated to get valuable insights in problems like fluid-structure interaction (FSI)
While coupling of DEM-CFD models the behavior of granular materials interacting with structures. Gain a deeper understanding of stress distribution, particle flow, and potential equipment wear.
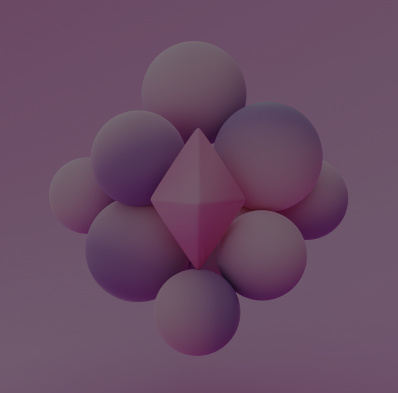

Tridiagonal simulates the complex interplay between fluids and structures. Often, the motion of fluids causes vibrations in structures. If the forcing frequency caused by fluid motion resonates with the natural frequency of the structure, it may lead to structural failure. To identify the magnitude of forces or frequencies, Computational Fluid Dynamics (CFD) is essential. Our experts calculate total deformation and von Mises stresses by considering the pressure calculated using CFD. We analyze fluid-induced stresses, vibrations, and other dynamic effects. Our engineers have analyzed equipment such as spargers, Liquid Seal Drums, Heat Exchangers, Feed Pipes, Distillation Column Piping, and Refinery Piping Support Failures.

Tridiagonal specializes in the coupled simulation of Discrete Element Method (DEM) and Finite Element Analysis (FEA), offering detailed insights into the interaction between particulate materials and structural components. By integrating DEM with FEA, we accurately model the behavior of granular materials and their impact on structural integrity, essential for applications in the oil and gas industry. Our simulations provide precise predictions of stress distribution, deformation, and wear within equipment subjected to particle interactions. This coupled approach is vital for optimizing the design and durability of critical components such as pipelines, separators, and drilling equipment. With our expertise in DEM-FEA coupling, we help clients enhance operational efficiency, safety, and longevity of their assets.

Tridiagonal excels in the coupled simulation of Computational Fluid Dynamics (CFD) and Discrete Element Method (DEM), providing comprehensive insights into fluid-particle interactions. By combining CFD with DEM, we accurately simulate the behavior of particulate systems within fluid flows, capturing complex phenomena such as particle transport, sedimentation, and erosion. Our advanced simulations enable the precise prediction of forces, velocities, and pressure distributions within multiphase systems. This integrated approach is crucial for optimizing the design and performance of equipment such as fluidized beds, cyclones, and reactors. Leveraging our expertise in CFD-DEM coupling, we help clients achieve enhanced efficiency, safety, and reliability in their processes.
Tridiagonal tech leaders can build a virtual replica of assets & processes in various industries to reduce simulation iterations using data interpolation. Methods like CFD, FEA & DEM can predict values that are not possible to gain from sensors.
Digital Twin
Tridiagonal tech experts can build a virtual replica of assets & processes in various industries to reduce simulation iterations using data interpolation. Methods like CFD, FEA & DEM can make predictions that may not be practically achievable through physical sensors.
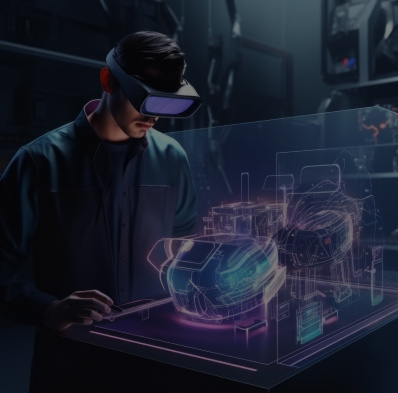

Areas where full-scale Simulation is computationally expensive & impractical, Tridiagonal can build ROMs by creating a lower-dimensional model that captures the essential behavior of the system. It not only speeds up simulations but also develops a straightforward approach for analysis.
%E2%80%8B.png?width=92&height=92&name=Creating%20Response%20surface%20models(RSM)%E2%80%8B.png)
In today's competitive world, Industry wants to save cost on simulations. Tridiagonal is addressing this requirement using a statistical technique called Response surface models(RSM). Here, our engineers are analyzing the relationship between several input variables and a desired output response variable. These response surface models are built using an appropriate set of CAE results, accurately predict the output variable for various input combinations without running individual Simulations. This technique is considerably reducing research and development cost in industries like oil refining and oil recovery.
Industries
Your Trusted Partner in Modeling & Simulation.
Oil and Gas
Tridiagonal has expertise in modeling equipment processes in upstream, midstream & downstream Industry segments. We cover wide range of applications like Burner optimization, validating Separator design, Flow uniformity of Cyclones.
Ensuring structural integrity of different Pressure vessels using codes like ASME and API. Troubleshooting and root cause analysis of structural failure. Providing insights for Retrofit solutions.
Pharmaceutical and Medical device
Tridiagonal enhances pharmaceutical manufacturing efficiency and product quality using advanced modeling techniques like CFD and DEM. They focus on scaling up batch processes, transitioning to continuous operations, and optimizing API manufacturing and formulation. Tridiagonal is also prominent in medical device manufacturing offering services for a range of applications including drug delivery system design, blood processing device design, extrusion dies for catheters, and patient-specific modeling.
Metals and Cement
Tridiagonal is specialized in modeling rotary kiln, Blast Furnace, Tundish, Blow pipe, burner arrangement, Cyclones, Bag filter & Electrostatic Precipitator(ESP) and structural analysis of Silos and thermal-structural analysis of Aluminum smelter.
Food, Beverage and CPG
Tridiagonal Solutions offers specialized support for CPG companies' process engineering and R&D teams. Our services cover a wide range of areas including mixing studies, product development, process optimization, packaging design, food drying, pneumatic transport, separation technologies, coating and granulation, controlled release, encapsulation, and software development. By leveraging our expertise, CPG companies can enhance process efficiency, product quality, and operational effectiveness.
Chemical and Process
Chemical Process Industries team at Tridiagonal provides expertise in reactor design, mixing analysis, and equipment optimization for chemical companies. Our services help reduce R&D costs, minimize environmental impact, and improve product and process performance, ultimately enhancing corporate profitability. We also address flow, heat, and mass transfer challenges in ancillary equipment.
Power and Renewables
Tridiagonal can analyze complex processes such as Sulfur recovery, Scrubbing & combustion of gas and pulverized coal through CFD to enhance the performance of various units running under power plant.
We ensure asset integrity of boilers using FEA.
Others
Tridiagonal leverage cutting-edge computational fluid dynamics (CFD) and finite element analysis (FEA) to optimize HVAC equipment design, analyze thermal comfort, assess fire suppression equipment efficiency and design effective smoke evacuation systems. Our engineers work for areas like automotive, Carbon capture and fuel cell battery cooling to play a significant role in sustainability.
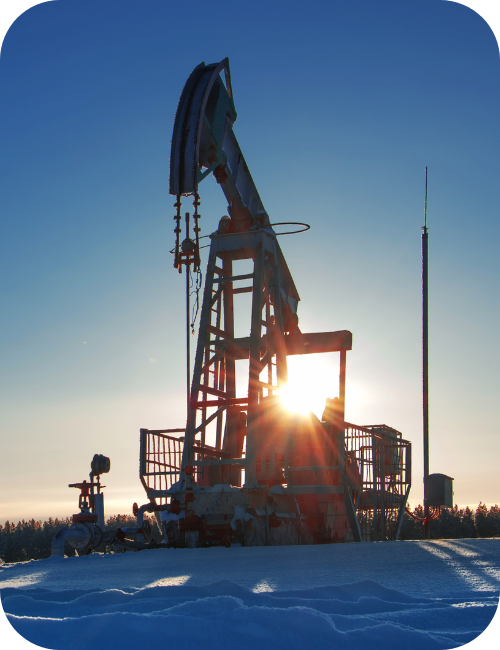
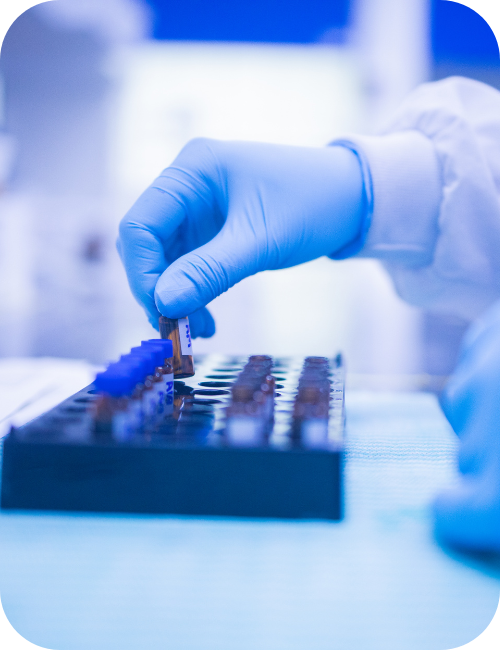
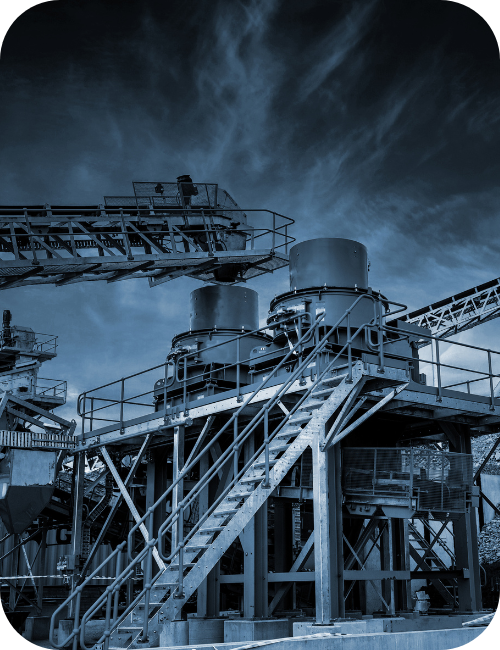
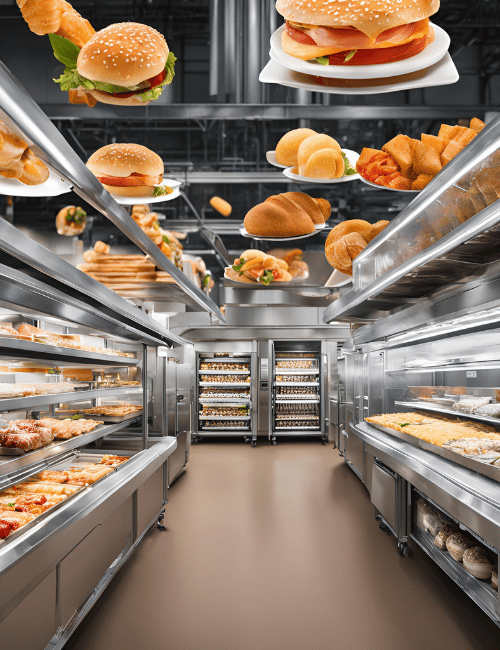
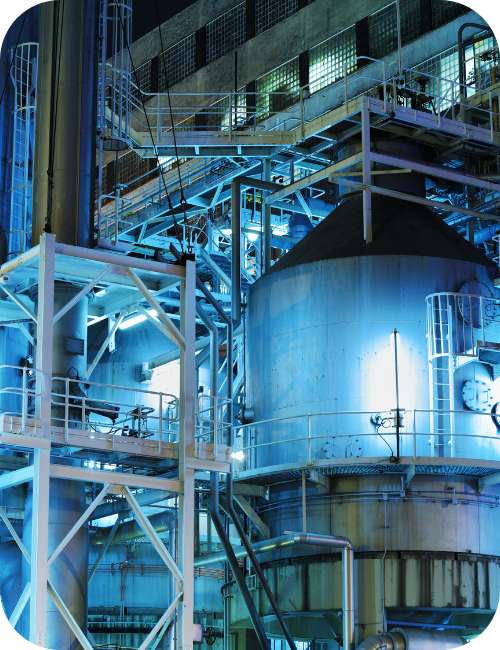
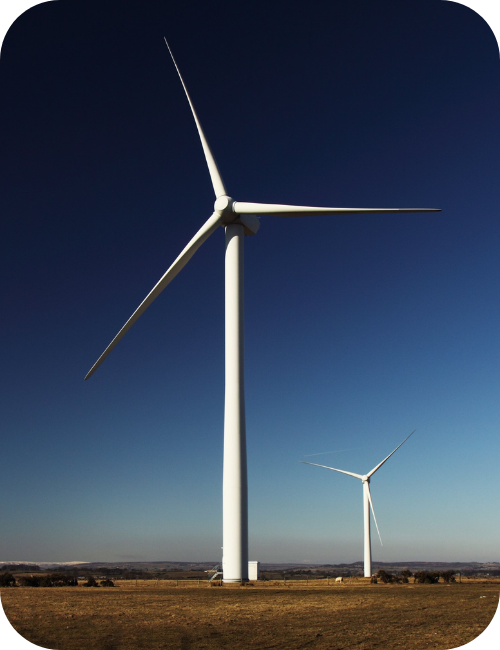
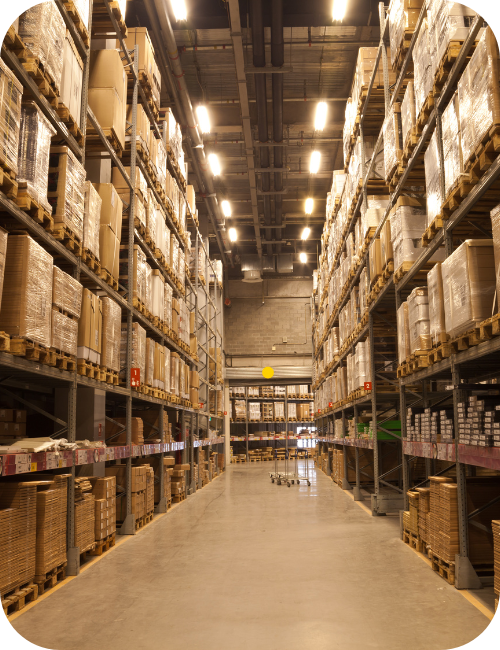
CFD-DEM applied to Catalyst-Particles in Packed Bed Reactors or Columns
Introduction:
The shape, size and packing of catalyst particles plays significant role in the performance of packed bed columns or reactors. Performing experiments is expensive and has limitations due to challenges in the measurements. The resolved-particle CFD simulations are digital replica of real setup with deeper details.
Decoding AI for Batch Process Optimization
Batch processing is one of the most common manufacturing approaches amongst many industries such as Biopharmaceuticals, Pharmaceuticals, and Specialty Chemicals.
Crafting Success Transforming Distillery Operations with IoT and AI
Join us for an exclusive webinar with AWS, where we unveil the secrets to revolutionizing the Distillery industry through the seamless integration of AWS IoT and AI solutions with Tridiagonal SMEs. Discover how this powerful combination enables the organization to improve fermentation/distillation efficiency by optimizing steam, fuel and chemical consumption.
Resources
Explore the breadth and depth of our digital transformation solutions in process manufacturing.
Why Tridiagonal?






Team having exposure and expertise of developing scalable solutions across multiple platforms.
Schedule a Call today!
Uncover how our capabilities can propel your organization forward. Provide your focus areas, and we will deliver tailored solutions designed to meet your unique objectives.