Siemens Simcenter
Develop better products Faster and Operate more efficient with safer oil and Gas facilities
Predict process performance, optimize for Energy and Process efficiency
Use the Power of digitalization to boost innovation with Integrated Ship Design and Engineering.
Siemens and Tridiagonal Solutions are now into a strategic partnership to co-develop process industry verticals (primarily Oil & Energy, Pharma, Food, Spec. Chem, Metals & Material, etc.) to provide the state-of the art solutions to the customers in their digital transformation journey. Tridiagonal will bring up the entire experience in the CFD domain to empower industries in identifying and deploying latest simulation techniques with Siemens Digital Solution offerings. Below is the quick overview of Siemens Simcenter portfolio and its applications for process industry.
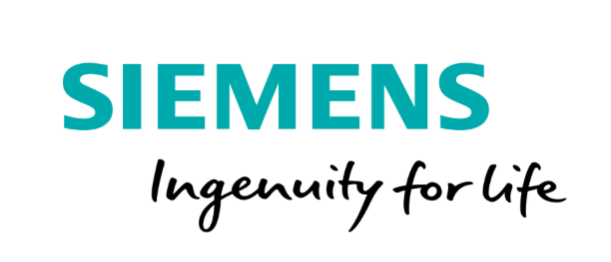
Simcenter - we help our customers avoid risk and gain a competitive edge by offering them a complete environment to effectively optimize the performance of complex products throughout the lifecycle, starting from the early stages. Simcenter allows engineers to generate a set of ultrarealistic, multi-physics models and data that can predict real product behavior. These are essential to the holistic digital twin, the industry paradigm that will help companies face today’s challenges with smart designs that combine mechanics with software, electronics, controls and new, lightweight materials. Using Simcenter will help manufacturers engineer innovation into their products faster and with greater confidence.
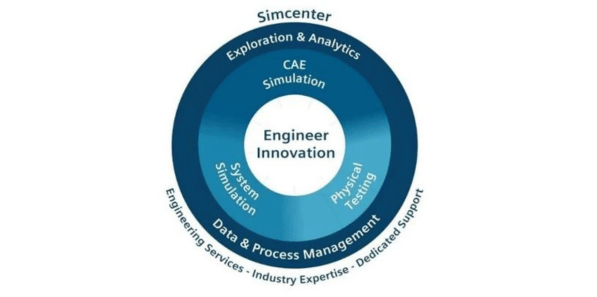
Delivering a comprehensive solutions portfolio
The strength of Simcenter is in both the excellence of its individual components and the synergies that can be achieved by combining them. The physical testing, multidisciplinary computer-aided engineering (CAE), computational fluid dynamics (CFD) and powerful multi-physics system simulation solutions are long-time industry leading applications. Simcenter solutions merge those elements with robust design exploration and data analytics, which are managed in a product lifecycle management (PLM) context powered by Teamcenter.
Oil and Gas
Our advanced simulation tools provide the insight and understanding required to design and operate systems that work together, to provide the required functionality and efficiency and help you to maintain the highest safety, environmental and performance standards needed to meet current and future industry needs.
Our solutions are capable of simulating a wide range of physical behaviors, from structural response and acoustics to heat transfer and fluid mechanics. Our solutions offer the ability to simulate system-wide behavior as well as capture the highest level of detail through its 3D computer-aided engineering (CAE) approaches such as finite element analysis (FEA) and computational fluid dynamics (CFD).
Whether you are involved in exploration and production, transportation or refining our solutions provide the simulation and data management backbone of your digital twin.
Process Industry
Operational excellence is the key to increasing profitability in the chemical process industries. With the constant demand for innovative new materials, every step of the process to convert raw materials into higher value products requires a deep understanding of complex multiphase and reaction phenomena. Your goal may be to improve under-performing equipment or to replace it with entirely new designs that reduce waste and energy consumption with increased yields. Or perhaps you’re looking to evolve your processes to be more sustainable and environmentally friendly.
To outperform in today’s competitive process industry, engineers need tools that enable them to develop the most complete understanding of the complex physical and chemical processes occurring in the equipment they design and troubleshoot; levels of understanding far beyond those provided by experiments or basic engineering principles.
Our portfolio of solutions combines:
- 1D and 3D system simulation methods
- Computational Fluid Dynamics simulation
- Discrete Element Modeling (DEM)
- Testing and Engineering Services
Together they provide a virtual engineering and analysis environment for predicting overall process performance, validating designs, or troubleshooting sub-optimal processes allowing engineering teams to achieve operational excellence, faster.
Pharma & Medical
Digitalization for the Medical Devices and Pharmaceuticals Industry
Siemens Digital Industries Software offers solutions for leading companies in the medical device and pharmaceutical industries that recognize the need for a product lifecycle management (PLM) platform to answer product development challenges. Our proven, flexible solutions help speed up innovation in the pharmaceutical and medical device development, ensure quality, reduce costs and maintain adherence to ever-changing global regulations, including FDA compliance.
Marine
Increasingly stringent emission standards and regulations are forcing improvement in all aspects of ship performance. Successfully achieving performance targets requires innovative designs to be effectively delivered in short time frames. Our solutions enable you to examine almost every aspect of ship design and meet and exceed required design standards.
- Oil and Gas
- Process Industry
- Pharma & Medical
- Marine
/Downhole%20Tols%20and%20Wellbore%20Operations-1.png?width=273&height=153&name=Downhole%20Tols%20and%20Wellbore%20Operations-1.png)
Downhole Tools & Wellbore Operations
Engineers must combine innovation and functionality in design with reliability and efficiency to ensure safe and successful drilling and production operations. Based on the digital twin approach, our solutions offer the ability to predict and assess mechanical, electronics and control behavior through the entire lifecycle of your product. Based on a combination of system simulation, 3-D Computer-Aided Engineering (including Computational Fluid Dynamics and Finite Element Analysis) and physical testing, our solutions help you lead your design and operations with simulation.
Whether involved in drilling or production operations, our solutions offer engineers a unique range of capabilities–from system-level simulation to detailed computer-aided engineering such as CFD and FEA. Embracing a digital twin approach places a predictive, simulation-based process at the center of the design and operational stages of a well’s life.
With the automated simulation workflows and physics models available in our solutions, it is possible to:
/Downhole%20Tols%20and%20Wellbore%20Operations-1.png?width=500&height=280&name=Downhole%20Tols%20and%20Wellbore%20Operations-1.png)
- Embrace a simulation-led process, putting the digital twin at the center of your design and operational decision-making
- Simulate the widest range of physics in drilling and production operations–from mechanical and structural responses, to flow, thermal and process behaviors, to electrical and control systems
- Increase your confidence in the performance, safety, and reliability of equipment and products exposed to the hostile operating conditions of the wellbore
- Innovate and explore designs faster to bring downhole and drilling products to market faster
- Use design space exploration coupled with physics-based simulation to understand real-world conditions and optimize your drilling or production system in operation
- Extend the life of operating systems through safe and effective simulation of operating conditions
- Identify the causes, and improve the performance, of under-performing equipment and processes
/Flow%20assurance%20and%20Subsea-1.png?width=273&height=153&name=Flow%20assurance%20and%20Subsea-1.png)
Flow Assurance & Subsea
Successful subsea production and processing requires safe, efficient and cost-effective designs that maximize production during operations. Our simulation and test solutions enable the creation of digital twins that offer engineers unparalleled insight into the performance of their products and systems throughout the complete asset lifecycle from design through production operations. Based on the combination of system simulation, 3D Computer Aided Engineering and Test, our solutions help you lead your design and operations with simulation.
Whether you’re involved in structural design and reliability, flow assurance, processing, integrity management or control systems, our solutions are there to increase confidence in your equipment and operations. Through the digital twin approach, our solutions offer the ability to predict performance at the system level, and in detail using 3D computer-aided engineering simulation throughout the lifecycle of an asset or system. Our solutions enable you to:
/Flow%20assurance%20and%20Subsea-1.png?width=500&height=280&name=Flow%20assurance%20and%20Subsea-1.png)
- Embrace a simulation-led process in your equipment design
- Use digital twins to collaborate with your design teams and operations
- Simulate the widest range of physics including mechanical and structural behavior, heat transfer, flow, vibration, and controls
- Simulate at both system and component level
- Innovate to bring new designs to market faster
- Simulate to improve production performance and reliability
- Simulate to extend the life of systems in operation
/Marine%20and%20Offshore.png?width=273&height=153&name=Marine%20and%20Offshore.png)
Marine & Offshore
Our solutions provide engineers with the ability to design better offshore systems through the use of simulation-based digital twins. Develop virtual representations of your offshore platforms and floating structures to inform and lead the design and operational decisions. Using simulation-based representations of your offshore structure or system it is possible to simulate real-world behaviors relating to interactions with the harsh marine environment and gain the confidence you can maximize system safety and optimize performance.
The digital twin can be used as the foundation of a simulation-led process. Our solutions give you the ability to capture behaviors such as wind and wave impact on, and interactions with, offshore structures as well as mechanical and control system responses during design, commissioning and operation.
From system-level simulations to computer-aided engineering our solutions offer the ability to:
/Marine%20and%20Offshore.png?width=500&height=280&name=Marine%20and%20Offshore.png)
- Simulate wave and current interactions using computational fluid dynamics (CFD)
- Predict structural response using Finite Element Analysis (FEA)
- Capture complex fluid-structure interaction simulation of offshore floating structures
- Perform system-level simulations of flow, thermal and control systems
- Manage storage of, and access to, large volumes of simulation data, whatever your toolset
- Automate design space exploration and optimization and combine your simulation toolset
/Process%20and%20seperation.png?width=273&height=153&name=Process%20and%20seperation.png)
Process & Separation
Maximizing efficiency and reliability is critical to process system performance. Our simulation solutions enable the creation of digital twins for your process systems, providing unparalleled insight to lead design and operational decisions. From separation and produced water to heat exchangers, compression and boosting, our solutions enable you to predict complex behaviors relating to multiphase flows, heat transfer, structural response and control systems. Whether designing new technology or operating existing facilities put simulation at the center of your process.
Process systems that are more reliable, efficient and compact are needed to meet the industry’s performance, environmental and financial needs. By placing simulation at the center of your process system design, our solutions enable you to make informed design decisions and maximize operational performance.
/Process%20and%20seperation.png?width=500&height=280&name=Process%20and%20seperation.png)
From system level simulations to detailed computer-aided engineering, our simulation solutions offer unparalleled capability for:
- Computational Fluid Dynamics with complete multiphase and multi-physics capability
- System level modelling for flow, thermal and electrical systems
- Structural analysis for predicting linear and non-linear behavior
- Complex coupled fluid structure behaviors, such as those that are vibration driven from flow and acoustic sources
- Manage and access simulation data from all disciplines in one place
Whether involved in drilling or production operations, our solutions offer engineers a unique range of capabilities–from system-level simulation to detailed computer-aided engineering such as CFD and FEA. Embracing a digital twin approach places a predictive, simulation-based process at the center of the design and operational stages of a well’s life.
With the automated simulation workflows and physics models available in our solutions, it is possible to:
- Embrace a simulation-led process, putting the digital twin at the center of your design and operational decision-making
- Simulate the widest range of physics in drilling and production operations–from mechanical and structural responses, to flow, thermal and process behaviors, to electrical and control systems
- Increase your confidence in the performance, safety, and reliability of equipment and products exposed to the hostile operating conditions of the wellbore
- Innovate and explore designs faster to bring downhole and drilling products to market faster
- Use design space exploration coupled with physics-based simulation to understand real-world conditions and optimize your drilling or production system in operation
/Process%20safety-1.png?width=273&height=153&name=Process%20safety-1.png)
Process Safety
Process safety is critical to all oil and gas production and processing facilities. Through the use of digital twins it is possible to simulate safety related events and to use the results and accompanying data to design and operate your assets with maximum insight in order to minimize process safety risks. Our solutions provide an unparalleled range of capabilities enabling you to simulate the unique behavior and responses of your systems and processes allowing your team to improve safety, maximize efficiency and optimize integrity.
Understanding, quantifying and managing risks to safety is paramount from the initial design to the end of life for a system or facility. Whether you are looking to understand system level behaviors or predict detailed component responses through computer aided engineering techniques, simulation based digital twins can provide the insight and data you need to maximize process safety.
/Process%20safety.png?width=500&height=280&name=Process%20safety.png)
Our solutions provide opportunities to:
- Create digital twins to visualize and understand real world behaviors
- Assess the impact of layout on safety related events and consequences
- Simulate real world behaviors involving flow, heat transfer, structural response and control systems
- Model planned and predict unplanned events, such as gas releases and dispersion
- Manage interactions between your facility and the environment
- Apply design space exploration to identify news methods of increasing process safety
- Manage all of your simulation and analysis data in one place.
For engineers who design or operate processes involving the extrusion or mixing of materials with complex rheological characteristics, our modeling and simulation solutions help you understand complex behavior, achieve process performance targets, and optimize operations by:
- Design and test extrusion dies virtually, then simulate the extrusion process with automatic die shape optimization before building expensive prototypes
- Lower engineering and extrusion line costs by evaluating multiple design options faster, assess “what if” strategies, and avoid issues that give rise to faulty out-of-spec products
- Accurately simulate flow in static mixers and reactors, as well as the flow in and out of commercial packaging, such as industrial lubricants and greases
- Minimize material waste and improve operational efficiency by reducing out-of-spec products ensuring consistently high product quality
/Transportation%20and%20refining-1.png?width=273&height=153&name=Transportation%20and%20refining-1.png)
Transportation & Refining
Our solutions help develop better designs and operate more efficient facilities by creating simulation-based digital twins of equipment and assets; Whether you’re simulating complex flow and heat transfer possibilities to structural response and control systems, you’ll gain the insight and data needed to stay ahead of today’s industry challenges.
Our solutions provide engineers with the ability to create digital twins capable of simulating real world behaviors. The digital twins are then used to gain the insight and data needed to improve designs and operating performance starting with the initial concept and throughout the complete lifecycle of downstream assets.
/Transportation%20and%20refining-1.png?width=500&height=280&name=Transportation%20and%20refining-1.png)
- Simulate system-level behaviors across a wide range of physics
- Combine multidisciplinary simulation with design space exploration to increase the range of options that meet your stated requirements
- Capture detailed phenomena through computational fluid dynamics and finite element analysis
- Manage all of your digital twin and simulation data in one place to eliminate silos of information.
- Perform multi-physics simulations to capture flow, thermal, mechanical and electrical phenomena
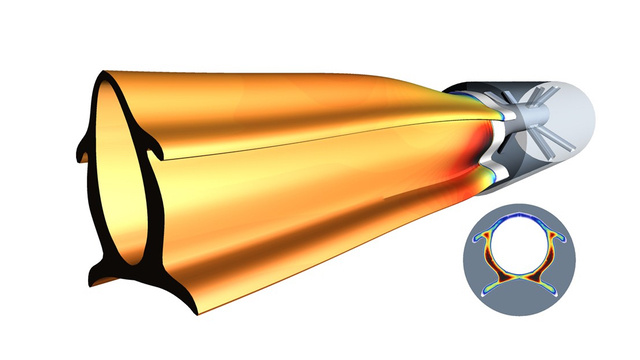
Complex Rheology
Numerous Energy & Utility industry segments work with processes that include non-Newtonian fluids with complex rheological properties. Our solutions simulate industrial mixing to design and optimize processes such as extrusion, co-extrusion, thermoforming, and static mixing for non-Newtonian materials that have complex rheological characteristics.
For engineers who design or operate processes involving the extrusion or mixing of materials with complex rheological characteristics, our modeling and simulation solutions help you understand complex behavior, achieve process performance targets, and optimize operations by:
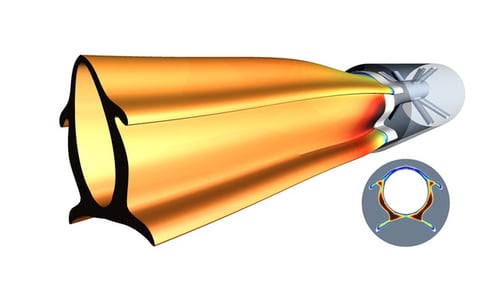
- Design and test extrusion dies virtually, then simulate the extrusion process with automatic die shape optimization before building expensive prototypes
- Minimize material waste and improve operational efficiency by reducing out-of-spec products ensuring consistently high product quality
- Lower engineering and extrusion line costs by evaluating multiple design options faster, assess “what if” strategies, and avoid issues that give rise to faulty out-of-spec products
- Accurately simulate flow in static mixers and reactors, as well as the flow in and out of commercial packaging, such as industrial lubricants and greases
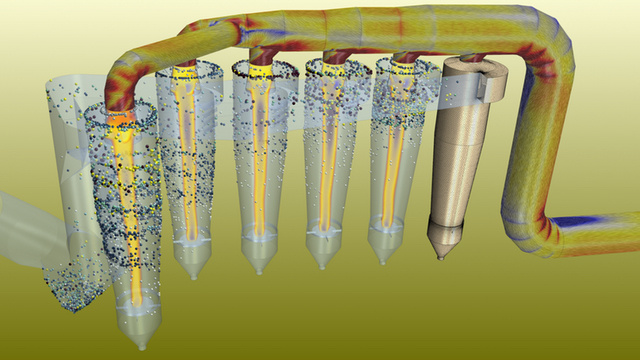
Flow Distribution & Separation Processes
From cyclone and electrostatic separators to distillation columns, our solutions allow you to optimize your flow distribution and separation technology in order to demonstrate process performance across the full range of operating conditions.
Our simulation solutions allow you to evaluate a wide range of performance indicators that are key to the design and understanding of flow distribution through separation equipment for key processes, such as:
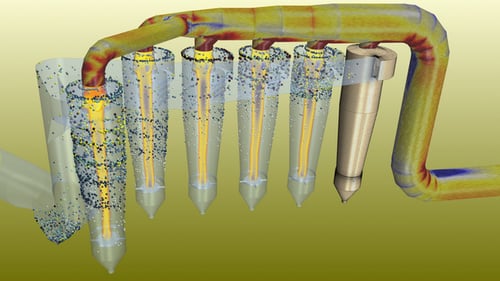
- Droplet behavior
- Particle tracks
- Erosion
- Phase distribution
- Sloshing
- Filtration
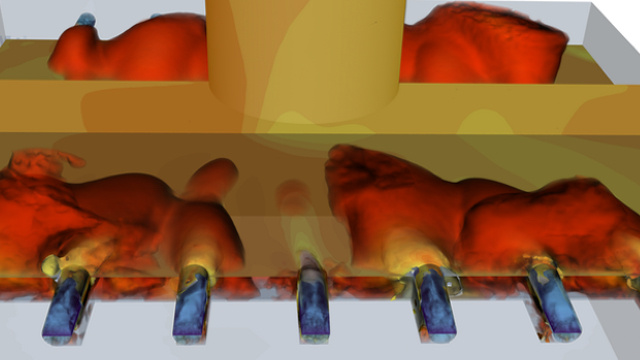
High Temperature Processes & Heat Transfer
Leverage the power of multi-physics simulation and testing to provide a more thorough understanding allowing for a better burner and furnace designs that meet process and financial performance goals, as well as government regulations.
Thermal process engineers who design or operate high-temperature equipment rely on heat transfer simulation solutions to opportunistically decrease energy costs, achieve process performance targets, reduce waste, and meet pollution regulations. Our solutions provide innovators with tools that can help overcome the challenges of achieving operational excellence in the chemical and process industries by:
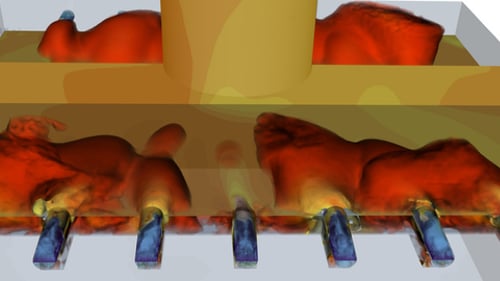
- Increasing combustion efficiency with higher heat absorption for a given amount of fuel
- Using design space exploration tools to identify undesirable process conditions, and find new configurations and operating conditions to optimize process performance.
- Increasing throughput efficiency by reducing raw material requirements while increasing yields and sustainability, as well as reducing the overall environmental impact
- Troubleshooting and improving under-performing processes or equipment in existing plants
- Increasing yield through higher conversion and selectivity
- Predicting and understanding the real-world behavior of flame dynamics, heat transfer and thermal wear, NOx, soot, CO and other emissions
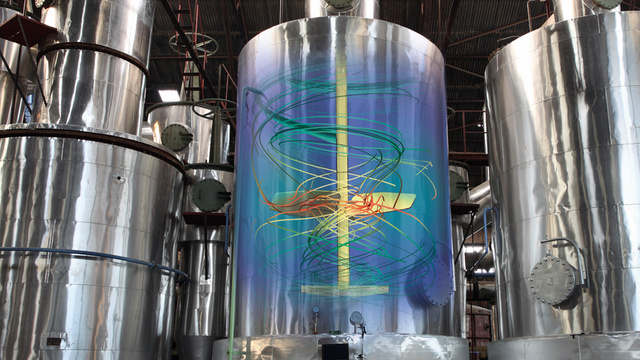
Mixing & Stirred Reactors
Leverage the power of multiphysics simulation to answer many of the questions associated with mixing and stirred reactors. Optimizing reactor performance increases margins through improved energy efficiency and throughput, higher product quality and consistency, and lowers operating costs by reducing process maintenance requirements.
With automated workflows that are purpose-built for mixing applications, our simulation solutions provide you with the tools to gain comprehensive engineering insights and overcome the challenges of achieving operational excellence in the Chemical and Process industries:
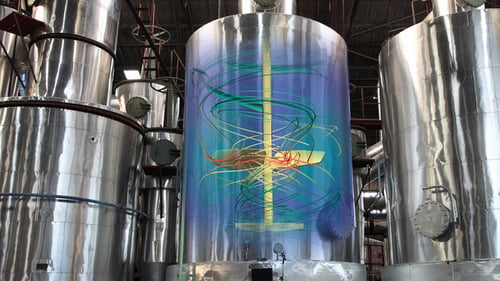
- Reduce power consumption by increasing hydraulic efficiency to achieve the same level of mixing with lower power consumption
- Troubleshoot and improve under-performing processes or equipment creating restorative value in brownfield facilities.
- Use design space exploration tools to find configurations and operating conditions that identify new levels of process performance and efficiency
- Increase productivity by reducing raw material requirements with higher throughput leading to greater environmental sustainability
- Move beyond traditional design approaches based on pilot-scale experiments, restrictive correlations, and costly production trials
- Develop a complete understanding of the internal processes, making complex phase interactions feasible through more innovative reaction schemes
- Bring new products to market faster by reducing the time and cost of development programs
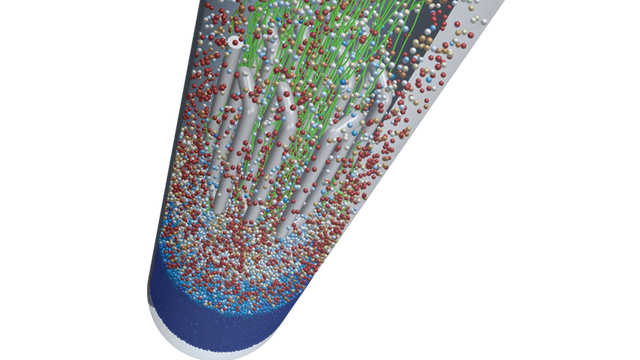
Particulate Processes
Leverage the power of high fidelity simulation and testing to model and understand all the processes involved in a coupled fluid and particulate system to optimize performance and efficiency
For engineers who design or operate processes involving particles and particulate transport, our solutions help you understand their complex behavior and meet process performance targets while optimizing operations
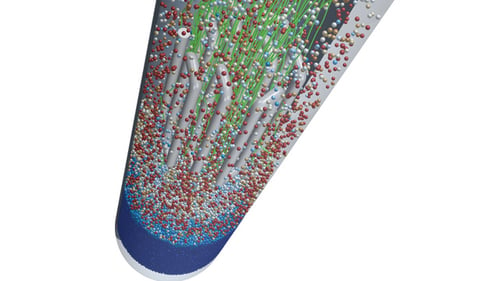
- Save time, energy and avoid over-design in particle transport systems by scaling up using virtual prototyping instead of having to rely on restrictive correlations and rules of thumb
- Increase operational efficiency by accounting for complex physics in particulate transport processes to understand and navigate the implications
- Use modern, coupled Discrete Element Method and Computational Fluid Dynamics solvers for particle and fluid flow allowing you to understand the shape, size, and surface behavior of particles during the design and engineering phases
- Reduce capital costs based on technical feasibility studies using high fidelity simulation to explore potential designs and alternatives
- Perform Computational Fluid Dynamics simulations for the pilot and at full scale under actual operating conditions
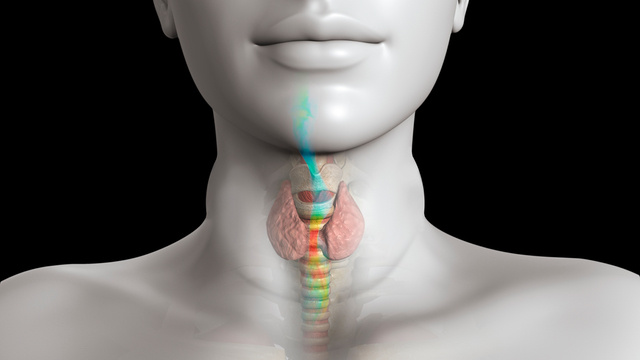
Simulation & Testing for Medical Devices
Simulation is playing an increasingly significant role in the development of medical devices, saving development costs by optimizing device performance and reliability, reducing benchtop tests and clinical trials, and helping to speed the regulatory approval process.
Developing increasingly complex medical devices requires increasingly capable tools for simulation and testing. Our deep portfolio of simulation and testing solutions allows medical device developers to generate digital evidence of device performance across a range of engineering disciplines, throughout the product life cycle.
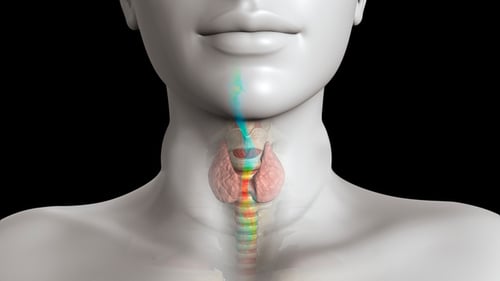
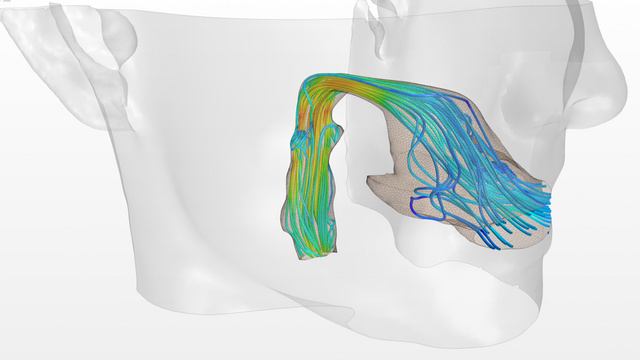
Design Analysis & Functional Performance
Simulation is already playing a prominent role in establishing product performance in the verification stages of device development. But it can also being used at every stage of the process, from concept development to design refinement and hand-off to manufacturing. Simulation and testing are not just important for generating objective evidence of device performance for regulatory agencies, they are foundational to good engineering practice.
Whether involved in drilling or production operations, our solutions offer engineers a unique range of capabilities–from system-level simulation to detailed computer-aided engineering such as CFD and FEA. Embracing a digital twin approach places a predictive, simulation-based process at the center of the design and operational stages of a well’s life.

With the automated simulation workflows and physics models available in our solutions, it is possible to:
- Embrace a simulation-led process, putting the digital twin at the center of your design and operational decision-making
- Identify the causes, and improve the performance, of under-performing equipment and processes
- Simulate the widest range of physics in drilling and production operations–from mechanical and structural responses, to flow, thermal and process behaviors, to electrical and control systems
- Extend the life of operating systems through safe and effective simulation of operating conditions
- Innovate and explore designs faster to bring downhole and drilling products to market faster
- Increase your confidence in the performance, safety, and reliability of equipment and products exposed to the hostile operating conditions of the wellbore
- Use design space exploration coupled with physics-based simulation to understand real-world conditions and optimize your drilling or production system in operation
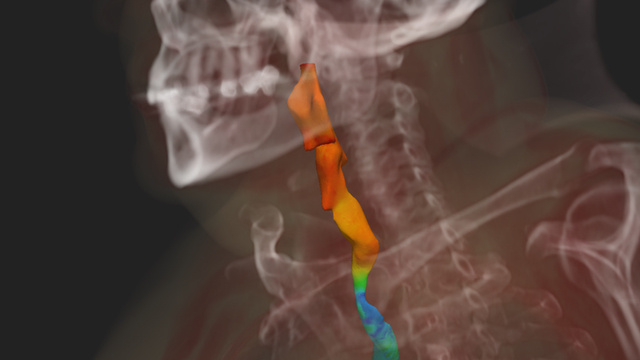
Assessing Variability & Robustness
Simulation plays a large role in predicting device performance, and helps manage risk, by allowing you to assess the response of your device to variability from multiple interacting sources: design variability, operational and usage variability, and patient variability.
At every step of the design process, a multitude of decisions are made. These decisions affect device performance. But which design decisions have the biggest impact on performance? How will a device perform when it is used across a broader patient population or operational range? Multidisciplinary design exploration provides a method for conducting systematic quantitative assessments of precisely these kinds of questions.

Our design exploration tools allow you to:
- Evaluate the robustness of designs to a wide range of operational scenarios and inputs
- Determine which design variables have the largest influence on your key performance metrics
- Predict how device performance will be affected by changes in patient characteristics/physiology
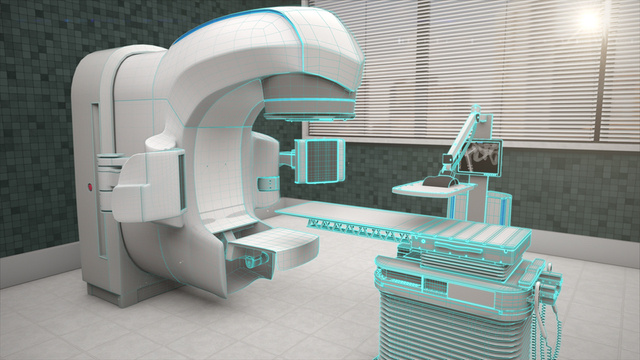
Solutions for Information & Process Management
Simulation is a powerful tool for generating digital evidence of device performance, and verifying that performance requirements are met. Simulation and test data must then become part of a structured verification plan that records and tracks results, providing traceability from requirements to engineering data.
Our solutions provide the platform for integrating simulation and test data into the broader, comprehensive database that comprises the “single source of truth” for your device, allowing you to:

- Define structured verification plans and track activity
- Create a structured definition of simulation and test contexts (what, when, who)
- Capture and record simulation and test results in context
- Provide data access, capture, storage, and reporting
Provide multi-domain traceability, change and configuration management–central requirements of sound engineering practice, and your regulatory compliance and reporting.
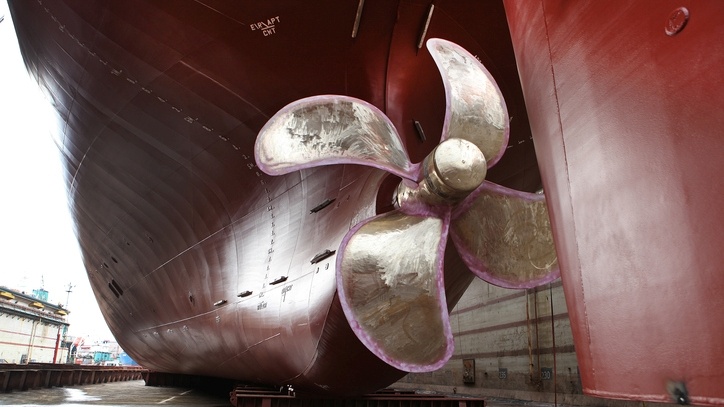
Propulsion System
Achieving an optimal propulsion system early in the design phase ensures the vessel meets contract requirements while improving sea-going capacity and reducing vessel fuel consumption. Our solutions create a propeller digital twin early in the design phase, giving understanding of propulsion effects at full scale. From propeller in isolation to sub-systems to full system performance, design an optimal, innovative propulsion system that meets contractual and regulatory obligations at a lower cost.
Use our propulsion system solutions to:
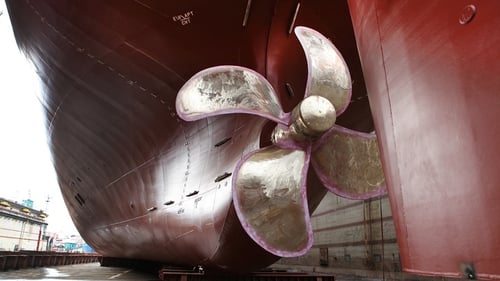
- Predict propeller performance, including the effects of cavitation and erosion.
- Optimize propeller designs for required operational efficiency.
- Simulate self-propulsion and analyze design-critical operating conditions.
- Improve existing fleet efficiency via energy saving devices and other refit options.
- Minimize vibro-acoustics, ensuring reduced environmental footprint and structural integrity.
- Provide accurate inputs to load calculations and system simulations.
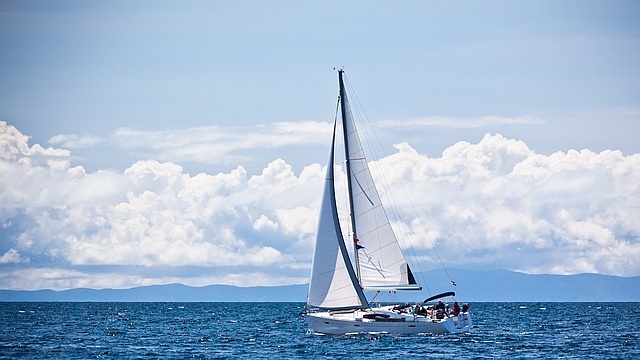
Aerodynamics
Design by testing is time-consuming, expensive, and cannot keep up with the current competitive landscape. Our simulation-based design approach to marine aerodynamics provides a streamlined, automated methodology to understanding the vessel superstructure and enables you to rapidly optimize your design for realistic operational conditions.
Our aerodynamic solutions enable you to:
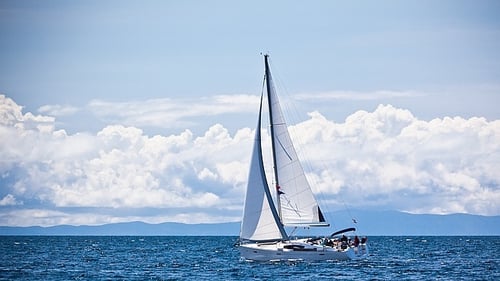
- Improve all aspects of vessel aerodynamic performance in a virtual wind tunnel
- Predict wind loading on vessel superstructure and confirm structural stability
- Minimize effects from exhaust gas emission and ensure regulatory compliance.
- Comply with helideck safety regulations and improve operational safety, including under extreme operating conditions.
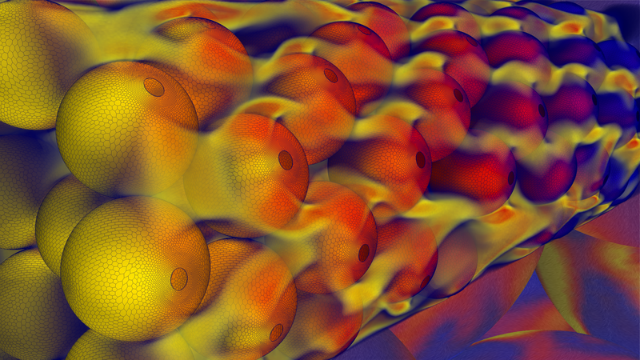
Fluid dynamics simulation
Since the real-world performance of your product depends on how it interacts with fluids, either gases, liquids or a combination of both, you need to predict how those fluids behave, and to be able to turn their influence to your product’s advantage. Simcenter provides industry leading computational fluid dynamics software that allows you to simulate almost any engineering problem that involves the fluids, structures and all of the associated physics.
Problems that involve multiple moving and interacting components can be easily simulated using overset meshing, mesh morphing, or a combination of both. The moving mesh capabilities can also be used for parametric studies and for steady or unsteady simulations, providing an easy way to reposition or replace objects to study multiple design configurations.
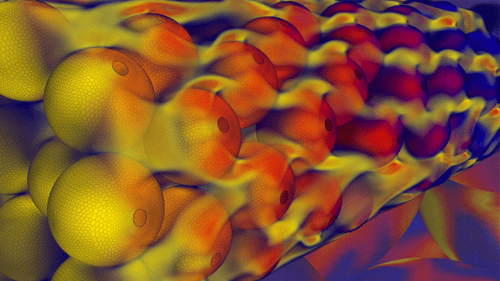
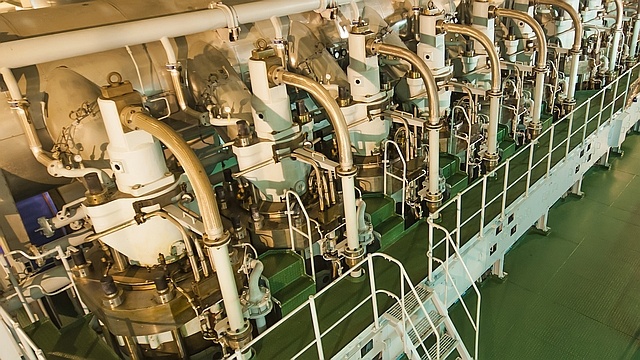
Engines & Power Generation
Improving fuel efficiency requires a holistic approach to engine and powertrain design. Our combined portfolio of testing and advanced simulation tools enables detailed component-level analysis, such as in-cylinder flow. Use integrated systems analysis to look at engines, electric generators, power electronics, and cooling systems. Critical performance areas such as component fatigue and durability, battery optimization, electrical motor design, and energy consumption can all be investigated using our simulation and testing tools.
Our solution portfolio is uniquely positioned to bring better engines to the market faster with a simulation-based design approach assessing engine performance and operation from component to full-system levels. Using a combination of simulation, testing, and optimization tools as well as specialized solutions for traditional and alternative propulsion systems, our portfolio enables you to design and integrate an optimal engine system for your vessel.
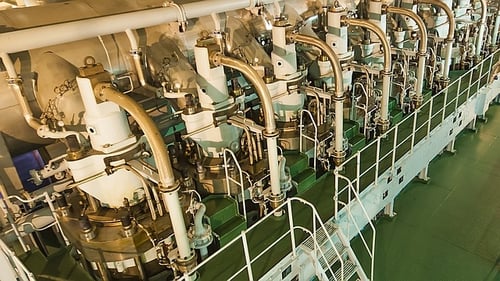
Our solutions can be used to:
- Optimize the performance of diesel and hybrid engine systems at component and system levels.
- Increase engine efficiency and reduce fuel consumption, helping to meet emissions regulations.
- Virtually develop and integrate electric motors and generators, ensuring high performance and reliability.
- Predict impact of modifications such as scrubbers on existing vessels.
- Design thermally efficient battery packs with optimized system design.
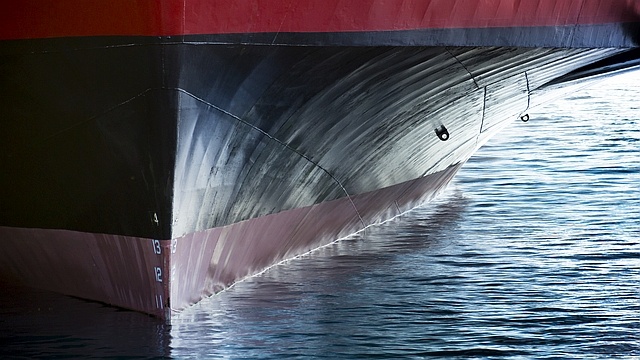
Hydrodynamics
Hydrodynamic performance engineering is critical to the optimal design of any vessel. Our solutions enable analysis of vessel hydrodynamics at full scale, and under realistic operating conditions. Use a virtual towing tank to examine any flow or performance aspect such as hull resistance, self-propulsion, maneuvering, vessel acceleration, or appendage shape, and alignment.
Growing competition and increasing awareness of the environmental impact caused by the marine industry drives a continuous need for more efficient design methods. Today simulation, in particular CFD, is widely used to perform analyses of ship hulls in calm water. However, real-life operating conditions include a wide range of sea states and, in many cases, the optimum design for rough seas differs significantly from that for calm water. A vessel’s hydrodynamic properties, including hull design and hull-propeller interaction, resistance, maneuvering, and seakeeping, must all be optimized together in order to achieve an energy-efficient design which can perform as required under these challenging conditions.
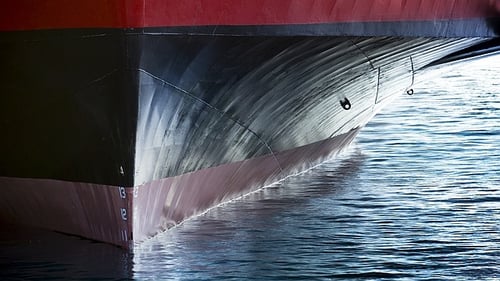
By developing a digital twin of the vessel in the design phase, our solutions allow early evaluation and optimization of hull forms under realistic conditions, helping the marine industry develop innovative, better designs faster.
Use our hydrodynamic solutions to:
- Perform full-scale CFD analysis of hull forms and appendages, removing any scaling uncertainties.
- Predict hull resistance under realistic operating conditions, including waves and open water.
- Analyze vessel performance when maneuvering, including self-propulsion.
- Ensure vessel designs meet seakeeping performance criteria.
- Examine wave loading and ensure structural stability.
- Optimize hull forms or appendages, including energy saving devices.
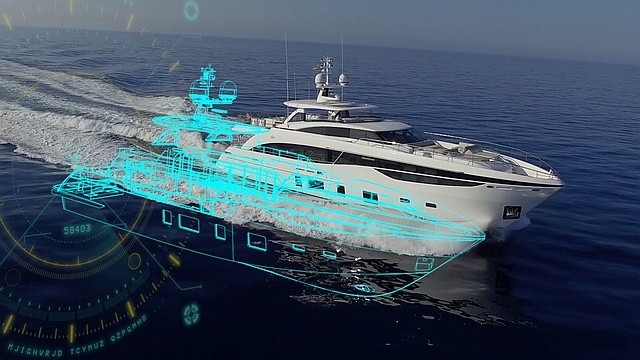
Structural Integrity & Dynamics
Sound structural integrity is critical for viable operation, crew and passengers’ safety and comfort, as well as minimal environmental impact. Our simulation and testing solutions can predict fatigue life and hotspots, and optimize a structure for durability, based on simulation from FEM-based stress results or measurement load data. Minimize the dynamic response of the structure early in the design cycle by simulating and optimizing the vibro-acoustic footprint of the vessel’s operation.
Long vessel lifetimes and high maintenance costs mean that safe, durable, and reliable construction is vital. Our portfolio of simulation and test solutions can be used as part of the design process to acquire and analyze physical data to virtually validate the structural integrity of a particular design.

Structural-borne noise and vibration need to be minimized for passenger comfort and reduced environmental impact. Our full suite of vibro-acoustics simulation, testing, and measurement tools ensures that you can minimize the structural dynamic impact of your vessel and its components early in the design phase.
Use our structural integrity and dynamics solutions to:
- Perform a wide range of structural analysis simulations, ensuring structural integrity.
- Examine thermal and stress responses on vessel components early in the design cycle.
- Determine vibro-acoustic effects and mitigate their influence.
- Optimize components while maintaining performance requirements.
- Determine vibro-acoustic effects and mitigate their influence.
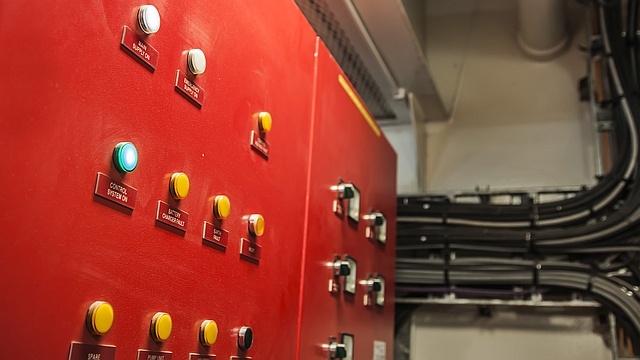
System Performance & Controls
Ensuring efficient vessel performance requires integration and optimization of multiple complex systems. Our solutions allow designers to check system architecture impacts on the complete vessel performance before any physical development takes place. Simulate and validate components early in the design cycle, and accurately predict the performance of systems including propulsion system architectures, hydraulic systems, and environmental control systems.
Reducing fuel consumption and emissions to meet environmental regulations requires optimal system performance and controls to design efficient, eco-friendly powertrain systems, including traditional, electric and hybrid. Marine system designers also need to improve overall performance, energy flow, NVH comfort and cargo capacity to differentiate from the competition.

Our system simulation solutions are designed for mechatronic system performance engineering from early design stage through to validation and controls calibration. Develop hybrid marine powertrains faster by selecting efficient architectures, component sizing and related control system strategy. Optimize engine efficiency and energy recovery systems with the early design of new system architectures reducing energy consumption and test costs while improving safety and durability. Our portfolio allows connected system simulation to perform full ship system performance analysis and find optimal fuel consumption for different scenarios.
Our system performance and controls solutions enable:
- Evaluate and optimize all marine engine subsystems, including air management, fuel injection and valvetrain systems.
- Improve energy management by validating the most efficient propulsion architecture over complete mission profiles.
- Design hydraulic systems efficiently via correct component sizing, ensuring optimal dynamic response.
- Optimize environmental control systems, including air conditioning and ventilation systems.
Schedule a Call today!
Uncover how our capabilities can propel your organization forward. Provide your focus areas, and we will deliver tailored solutions designed to meet your unique objectives.